A case involving a multi-national food company has highlighted the significance of machine safety in the manufacturing industry.
Kerry Ingredients (UK) Limited was fined more than £300,000 after one of its workers lost four fingers on his right hand while unblocking a machine at a site in Glasgow. The man was working on a mixer at the site, where dry seasoning blends and mixes are manufactured for the food industry.
During the mixing process the machine began to develop a blockage, which the worker attempted to clear by inserting his right hand into the machine. However, as he did so, it came into contact with the rotating blades which resulted in the amputation of four of his fingers. Since the incident, the man has had to re-learn how to do everything with his left hand.
An investigation by the Health and Safety Executive (HSE) established that there were no fixed guards preventing access to the blades from the underside. It also found there were not any interlocked guards which would stop the rotating parts if any component on the underside of the mixer were to be removed.
In the UK's manufacturing sector, machine safety is a critical concern that impacts not only the wellbeing of workers but also the overall productivity and compliance of businesses. The complexity and power of machinery used in manufacturing pose significant risks if not properly managed. Below, we explore the importance of machine safety in UK manufacturing, the legal framework governing it, common hazards and best practices to mitigate risks.
Importance of machine safety
Machine safety in manufacturing is essential for several reasons:
- Worker protection: The primary concern is the safety of workers who operate or work near machinery. Accidents involving machinery can result in severe injuries, long-term disabilities, or even fatalities.
- Legal compliance: UK law mandates strict safety standards for machinery in the workplace. Non-compliance can lead to legal repercussions, including fines, penalties, and potential closure of businesses.
- Productivity: Unsafe machinery can lead to frequent breakdowns, accidents, and downtime, which can disrupt production schedules and increase costs.
- Reputation: Companies that prioritise safety are more likely to attract and retain employees and gain trust from clients and partners.
Legal framework governing machine safety
In the UK, machine safety is governed by a combination of regulations and directives, primarily under the Health and Safety at Work Act 1974. The key regulations include:
- Provision and Use of Work Equipment Regulations (PUWER) 1998: PUWER mandates that employers ensure work equipment is safe for use, properly maintained, and only operated by competent individuals.
- Supply of Machinery (Safety) Regulations 2008: These regulations require that new machinery supplied in the UK meets essential health and safety requirements, including proper design, guarding, and risk assessment.
- The Control of Vibration at Work Regulations 2005: These regulations address the risks associated with the use of vibrating machinery and tools, which can cause long-term health issues.
- The Control of Noise at Work Regulations 2005: Noise generated by machinery can lead to hearing loss, so these regulations mandate employers to assess and control exposure to noise.
- The Personal Protective Equipment at Work Regulations 1992: Employers are required to provide appropriate protective equipment to reduce risks associated with machinery use.
Common machine-related hazards
Manufacturing machinery presents a variety of hazards, including:
- Mechanical hazards: These include moving parts that can cause cuts, crush injuries, or entanglement. Examples are rotating shafts, gears, and conveyor belts.
- Electrical hazards: Faulty wiring or poor insulation can result in electric shocks, burns, or even explosions in some cases.
- Thermal hazards: High temperatures generated by machinery can cause burns or fires if not properly controlled.
- Noise and vibration: Prolonged exposure to high noise levels or vibration can lead to hearing loss and conditions like Hand-Arm Vibration Syndrome (HAVS).
- Chemical hazards: Machinery that involves the use of chemicals can expose workers to toxic substances, leading to respiratory issues, burns, or poisoning.
Best practices for ensuring machine safety
To mitigate the risks associated with machinery in manufacturing, companies must adopt a proactive approach to safety. Key practices include:
- Risk assessment: Conducting regular risk assessments to identify potential hazards and implement appropriate control measures. This includes evaluating the entire lifecycle of machinery from installation to disposal.
- Machine guarding: Installing physical guards to prevent contact with dangerous parts of the machinery. Guards should be robust, tamper-proof, and regularly inspected for effectiveness.
- Training and competency: Ensuring that all operators and maintenance personnel are adequately trained in the safe use of machinery. Continuous training programmes can help keep workers updated on new safety procedures.
- Preventive maintenance: Regular maintenance schedules should be established to prevent machinery failures that could lead to accidents. This includes checking for wear and tear, lubrication, and replacement of faulty parts.
- Emergency procedures: Establishing clear emergency stop procedures and ensuring that all employees are aware of how to activate them. Emergency stop buttons should be easily accessible and tested regularly.
- Personal Protective Equipment (PPE): Providing appropriate PPE, such as gloves, safety goggles, and hearing protection, and ensuring that employees use them consistently.
- Signage and warnings: Displaying clear warning signs around hazardous machinery to alert workers of potential dangers. This can include instructions for safe operation and warnings about specific risks.
- Safety interlocks and automation: Utilising safety interlocks that automatically shut down machinery if a safety guard is removed or if a fault is detected. Automation can also reduce the need for manual handling of machinery, thereby reducing risk.
Conclusion
Machine safety is a critical aspect of manufacturing in the UK, with significant implications for worker safety, legal compliance, and business productivity. By adhering to the legal framework and implementing best practices, manufacturers can create a safer work environment, reduce the likelihood of accidents, and maintain a strong reputation in the industry.
You might also be interested in
RELATED CONTENT
RELATED COURSES
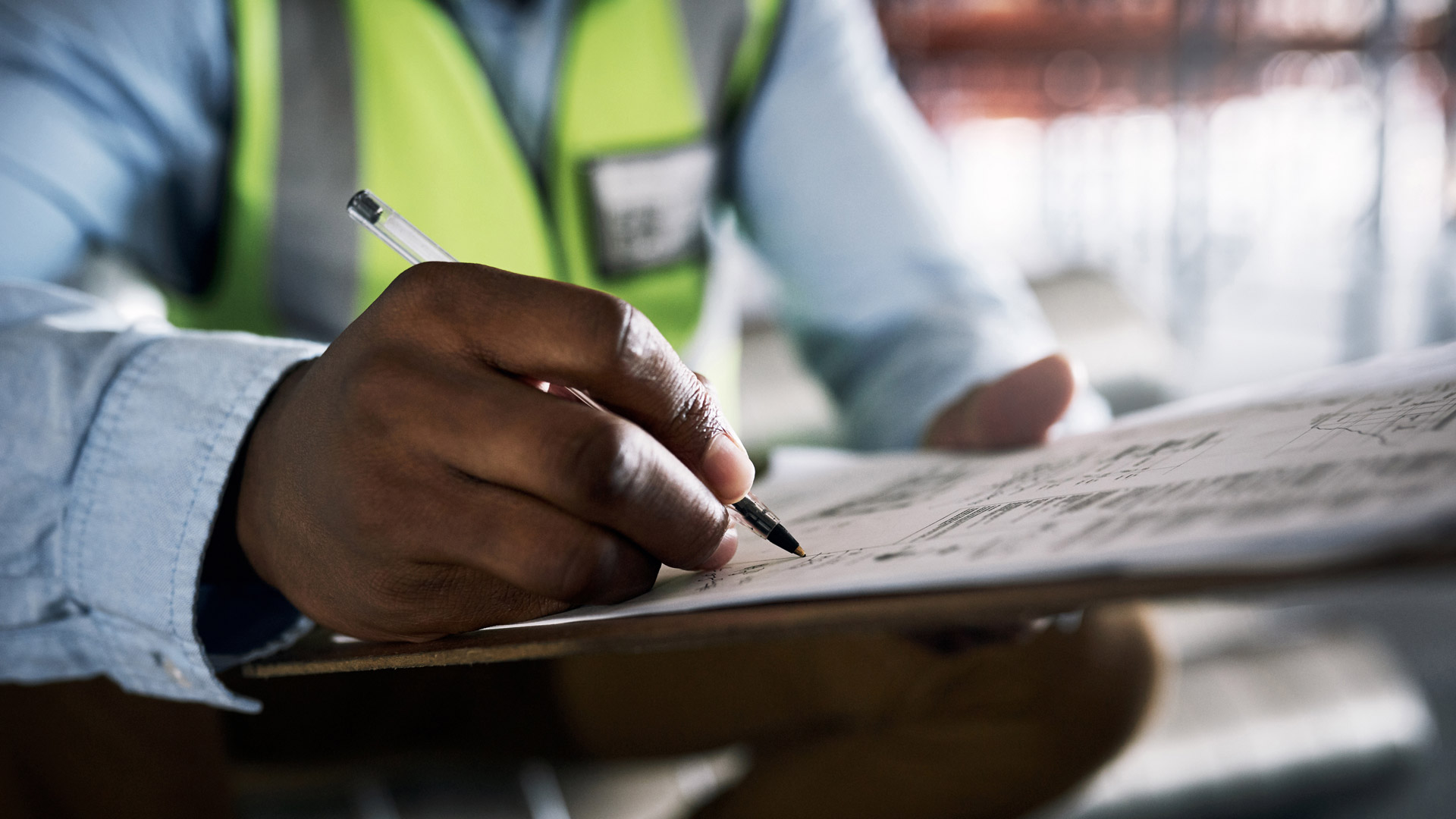
The Risk Assessment and Method Statement (RAMS) course examines the HSE’s recognised five-step approach to risk assessment.
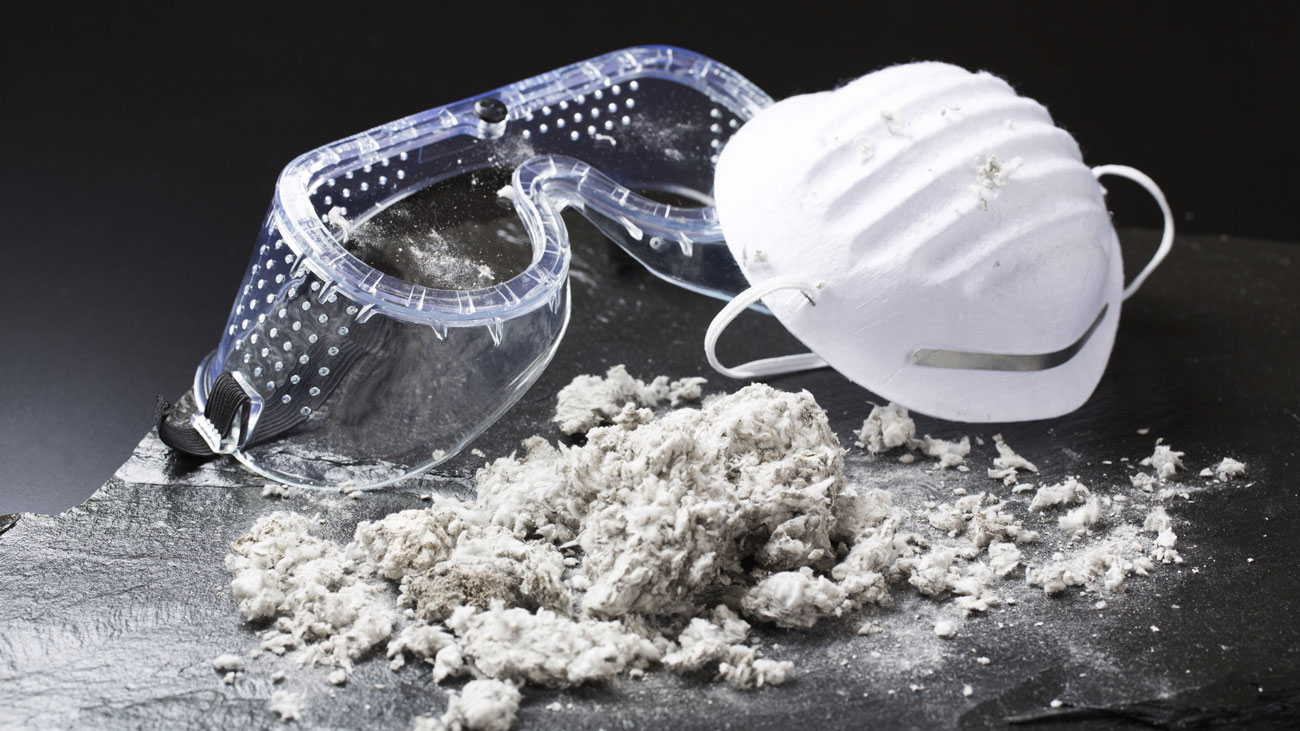
The Dust and silica exposure course looks at the risks of exposure to hazardous dusts and how they can be controlled and managed.
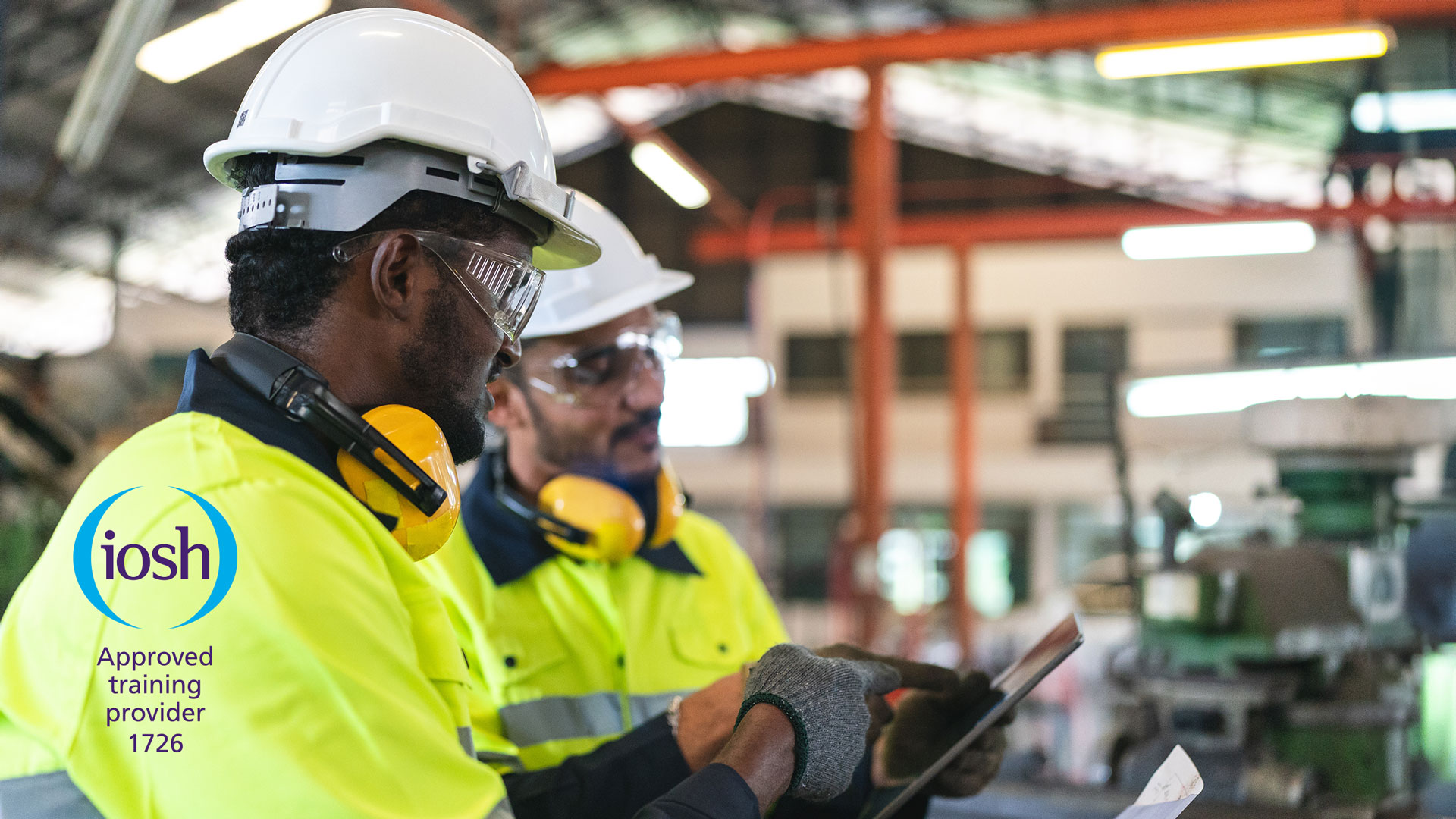
IOSH Working Safely is a one-day introductory health and safety training course for people at any level, in any sector.
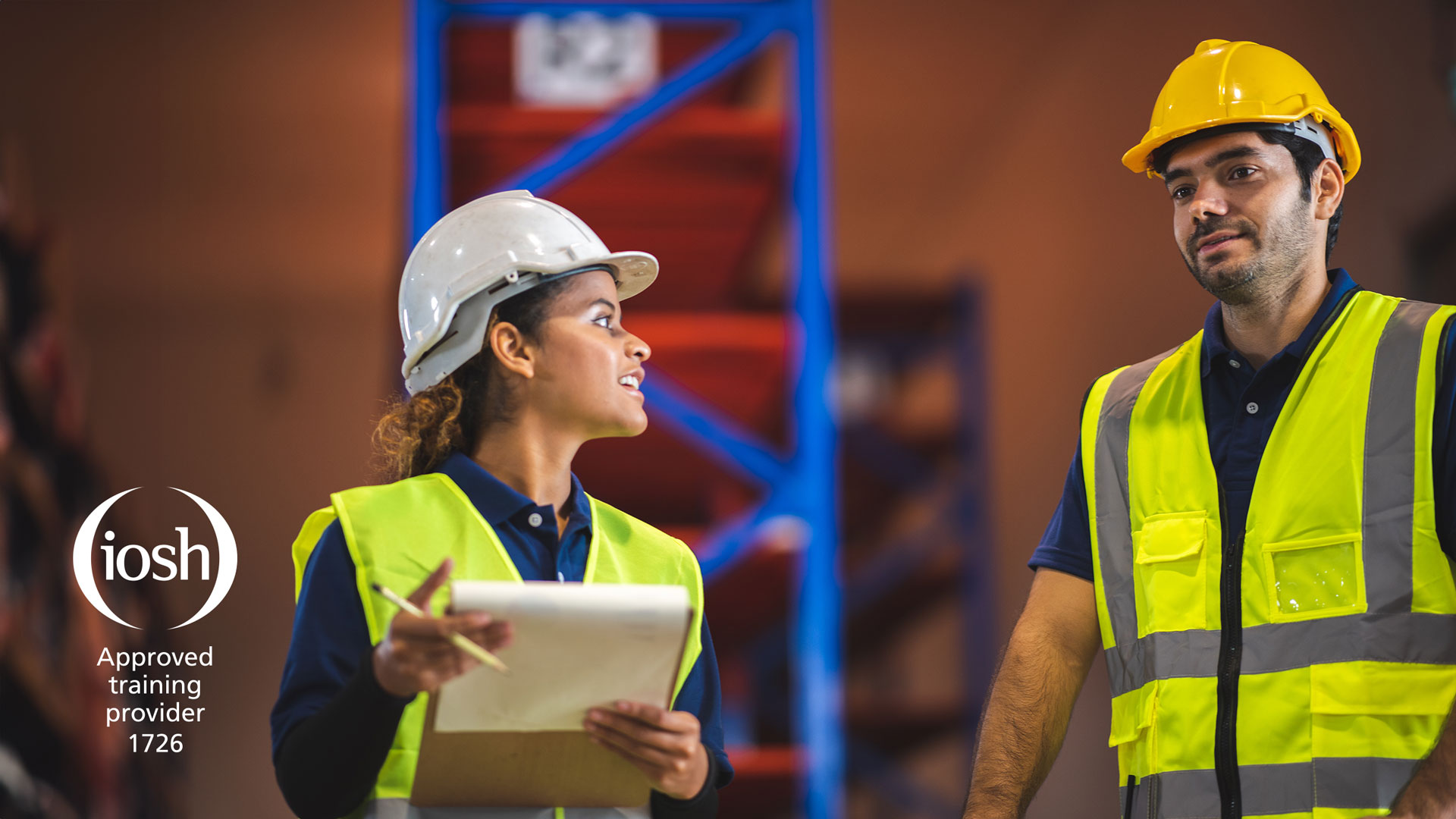
The world’s best-known health and safety certificate, designed for managers and supervisors in any sector or organisation.
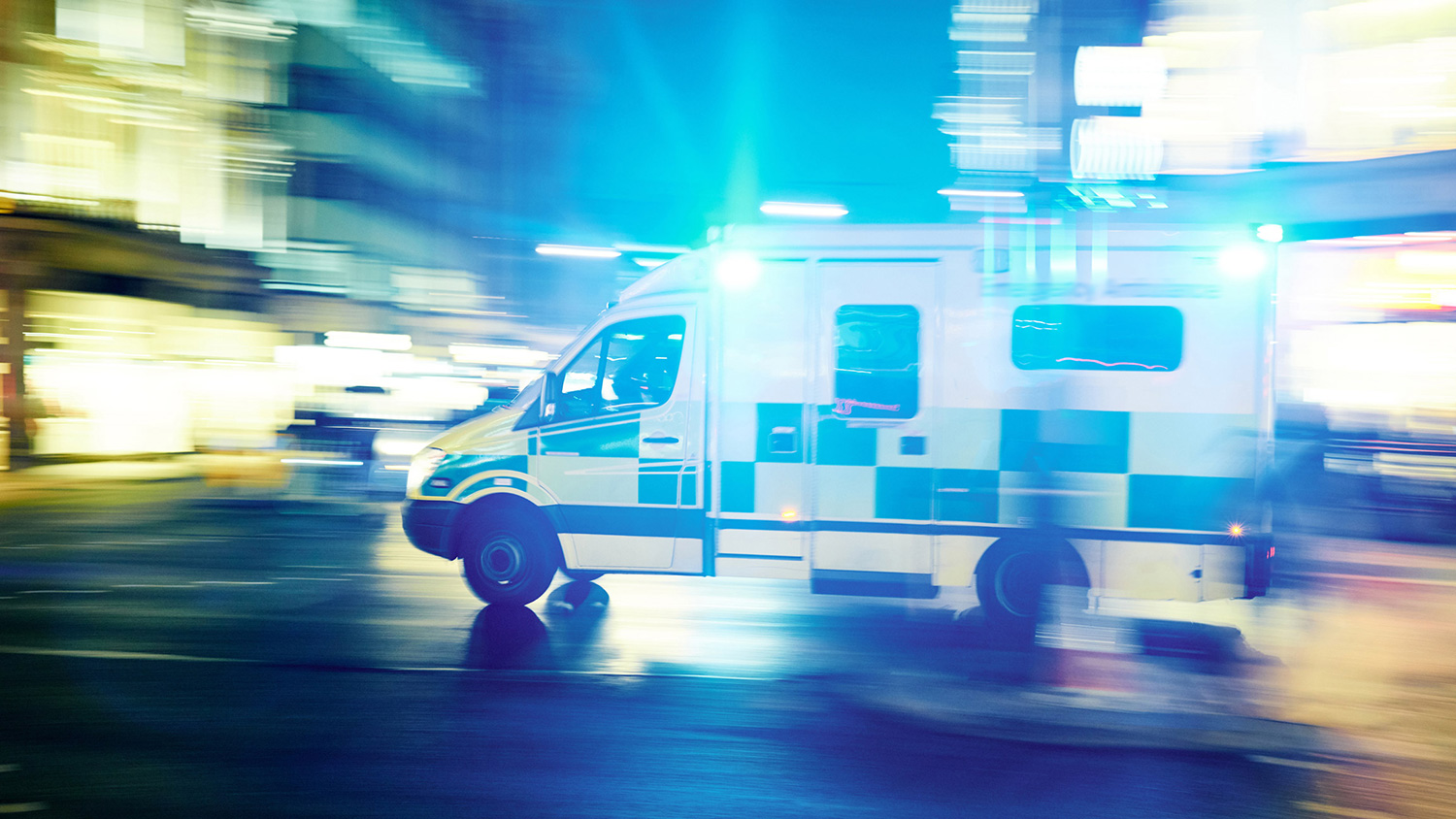
A worker whose hand was cut off while he was repairing a factory machine has said his injuries are so bad he struggles to pick up his granddaughter fo...
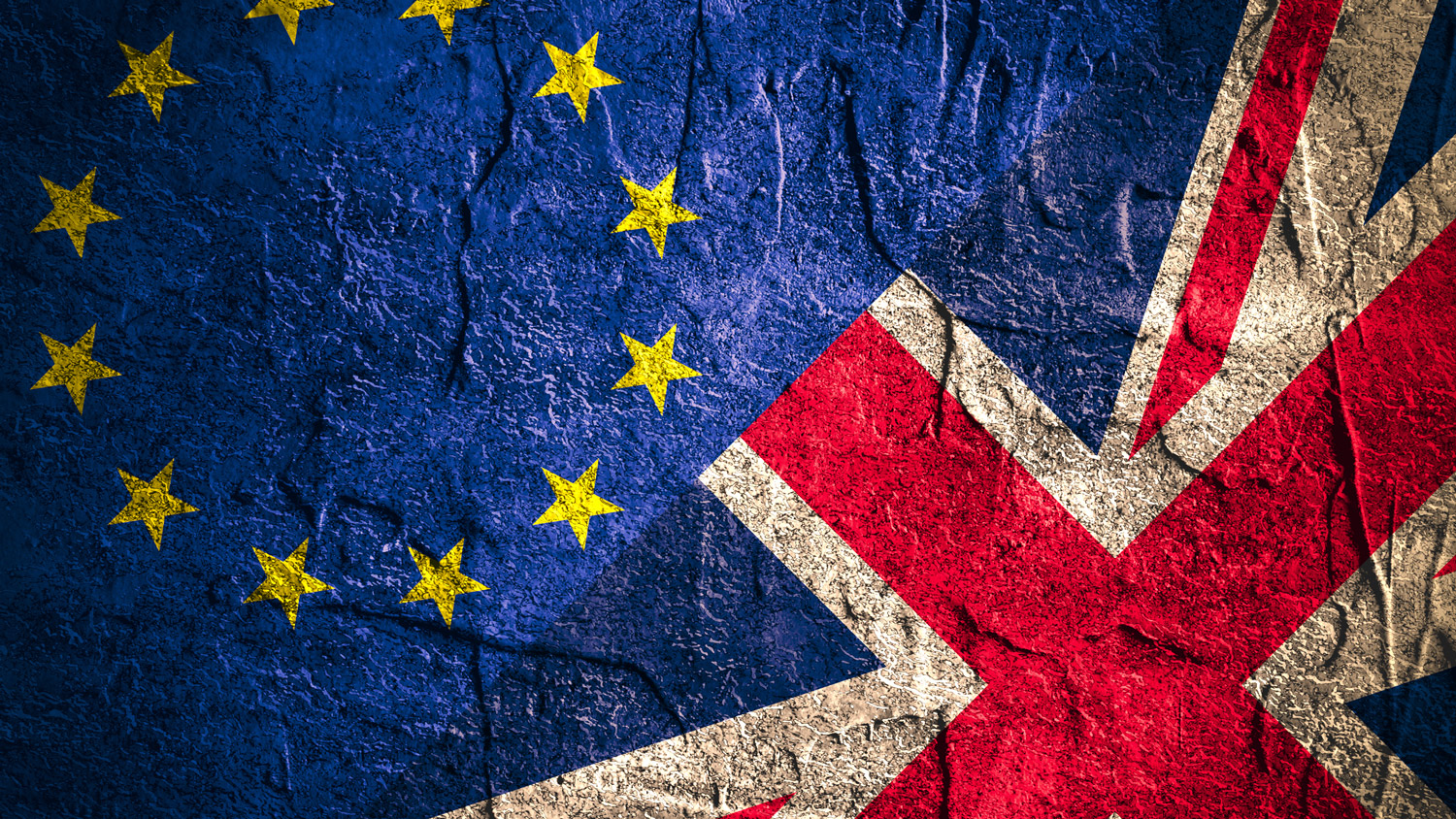
Following the departure of the UK from the EU, and the transition period which comes to an end on 31 December 2020, new rules from January 2021 will e...
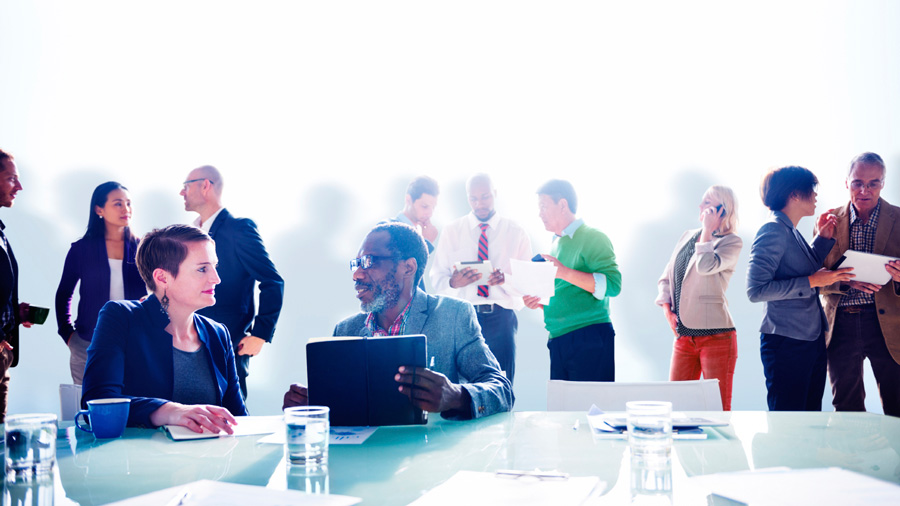
Manufacturing can be a dangerous business, it is one of the industries with the most workplace injuries and fatalities. It accounts for only 10% of th...
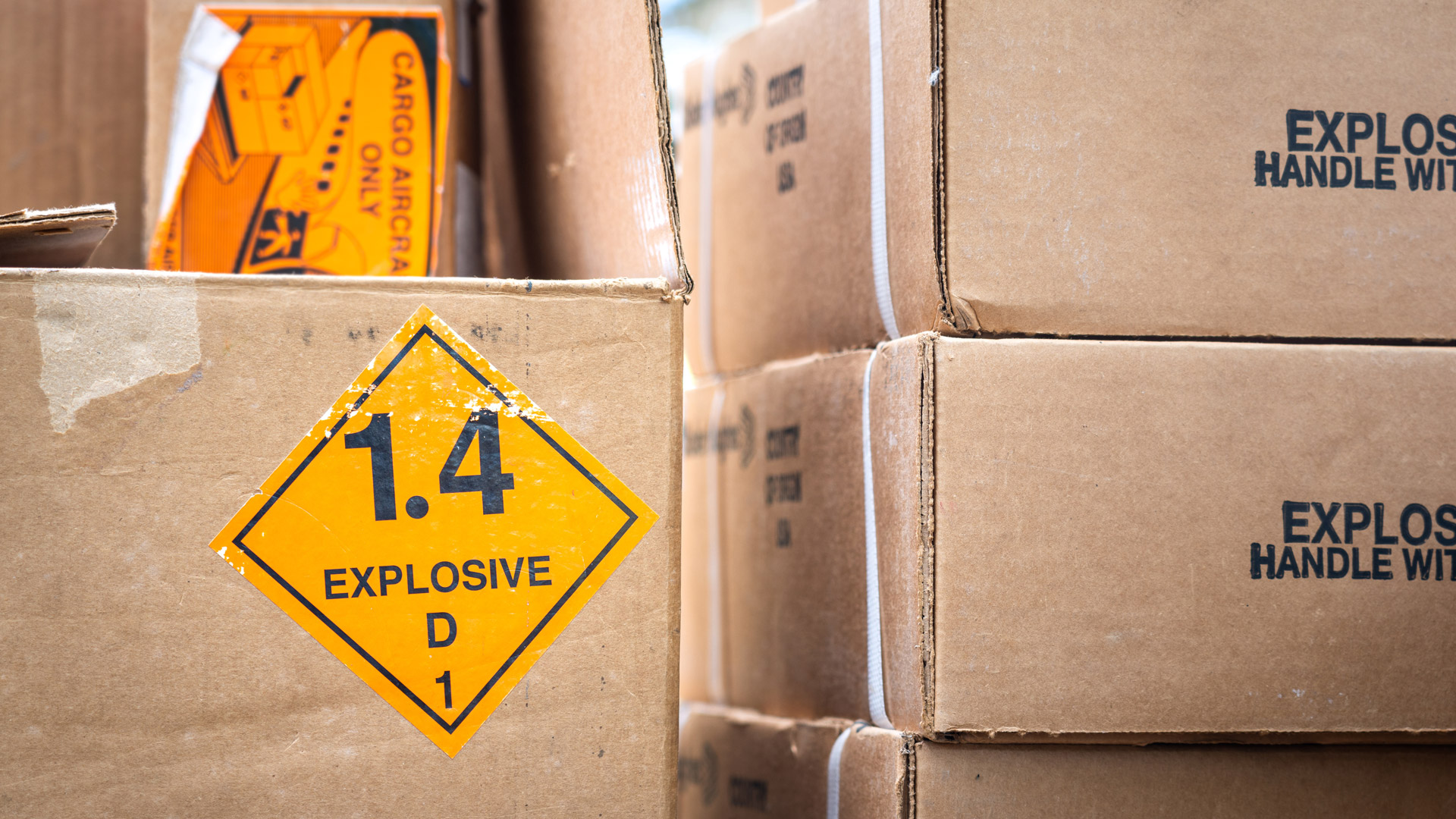
A manufacturer of military explosives has been fined £670,000 after an employee was killed and another seriously injured in an explosion at its factor...