Bernard Matthew’s Food Ltd has been fined £400,000 following two separate incidents where employees were seriously injured. Colin Frewin was left permanently paralysed and spent six months in hospital following an incident at the company’s Suffolk manufacturing plant. Frewin suffered multiple serious injuries, including a pierced left lung, several broken ribs, four fractured vertebrae and a spinal bleed. He was put in an induced coma for three weeks and is now classed as a T6 paraplegic and has been diagnosed with autonomic dysreflexia (AD).
Chelmsford Crown Court heard how Frewin suffered the injuries on 28 January 2020. He’d been tasked with cleaning a large screw conveyor used to move poultry turkeys along and chill them. While working on the gantry between the spin chillers he noticed a turkey stuck at the bottom of it. As he attempted to dislodge the turkey using a squeegee, Frewin was drawn into the machine. It was only when a colleague noticed Frewin was missing from the gantry and heard his cries for help, the emergency stop was pulled.
The HSE investigation found an unsafe system of work meant the chillers remained running as Frewin went to dislodge the turkey. In a victim personal statement, Mr Frewin described how his horrific injuries left him feeling “isolated” and in need of daily care. He said:
“I will never walk again and so I will be in a wheelchair permanently. I now have a suprapubic catheter, which was inserted via an operation. The district nurse has to give me bowel care every day and visits me daily at home. I also suffer from AD – a condition which is life threatening, as my body doesn’t register if I’m ill. I have moved from my flat overlooking the sea, to a bungalow. However, I miss seeing the sea and being close to the seafront and all the amenities. I feel isolated as I cannot go out when I want as I need people to assist me.”
Frewin, who lives on his own, is visited by carers at least three times a day and can’t even shower on his own. He added:
“I can’t socialise with my friends and family as much as I used to, as I can’t fit my wheelchair into their homes. Physical relationships are very hard as I can’t get out much. The accident has affected my life and my family’s lives. When I talk about the incident, I sometimes find this upsetting and then have restless nights.”
Another incident occurred at the same plant five months earlier, on 12 August 2019, when a turkey deboning line had to be shut down after developing a fault. As a result, Adriano Gama, along with the rest of the employees, were moved to a surplus production line to continue the process. Whilst working on the surplus production line, one of the wings became stuck in the belt under the machine. Gama attempted to push it out of the way, but as he did do, his gloved hand became caught in the exposed sprocket of the conveyer and was drawn into the machine.
He was eventually freed and taken to hospital having suffered a broken arm and severe damage to the muscles in his forearm. An investigation by the HSE found that on the day of the incident pre-start checks were only completed on the production lines that were regularly used. Therefore, when workers were asked to move to the surplus deboning line there was no system in place to ensure that it was checked prior to it being put into operation. The investigation uncovered that two safety guards had been removed and a team leader responsible for the production lines had verbally reported this issue to the engineering team, but it was not followed up by either party.
Bernard Matthews Food Ltd pleaded guilty to breaching section 2(1) of the Health and Safety at Work etc. Act 1974. The company was fined £400,000 (£300,000 for the incident in relation to Colin Frewin and £100,000 for that involving Adriano Gama) and ordered to pay costs of £15,000.
After the sentencing, HSE Principal Inspector Adam Hills said:
“Both incidents could have been avoided – the consequences were devastating for Mr Frewin in particular. If Bernard Matthews had acted to identify and manage the risks involved and put a safe system of work in place they could have easily been prevented. Fundamentally, you should not clean a machine while it is running. Companies need to ensure that risk assessments cover activities including cleaning and blockages, and that where appropriate, robust isolation and lock off mechanisms are in place for these activities. Prior to use you can put in place some pre-start checks and if faults such as missing guards are identified they need to be formally reported, tracked, rectified and closed out.”
The introduction of safe systems of work will often make activities much safer. The extent of the safe system of work will depend on the nature of the activity and how dangerous the activity might be.
Permit-to-work systems are detailed formal written systems that are used for controlling works that are particularly hazardous, such as working with high voltage electricity or in confined spaces. The permit specifies the exact work that is to be carried out, along with the precautions that must be taken.
All employees must understand the importance of following safe working procedures. The level of training will vary depending on the nature of the job, the level of risk and the competency of the person.
You may also be interested in
RELATED CONTENT
RELATED COURSES
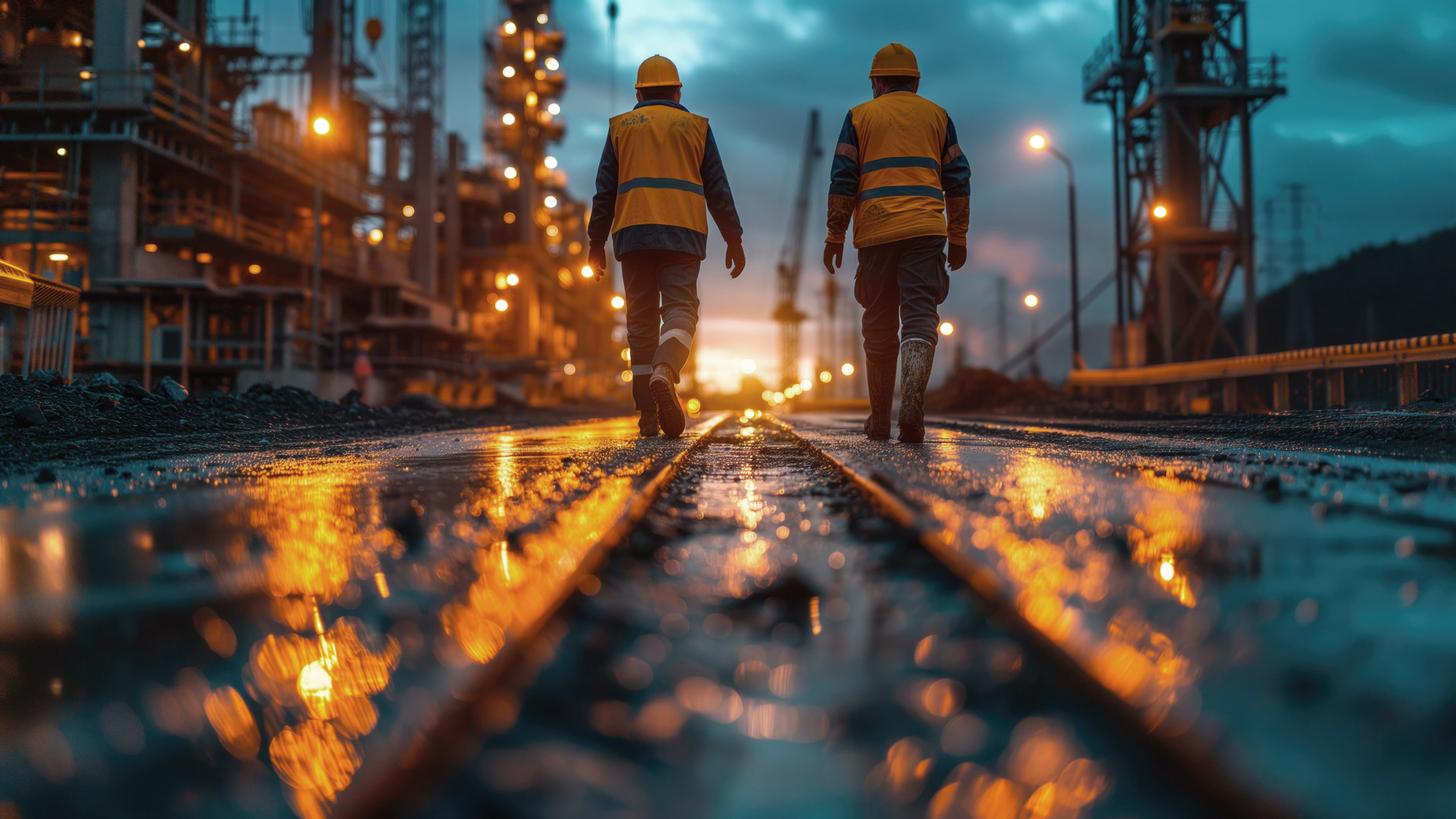
Introduction to health and safety gives learners a basic introduction to managing safety in their workplace.
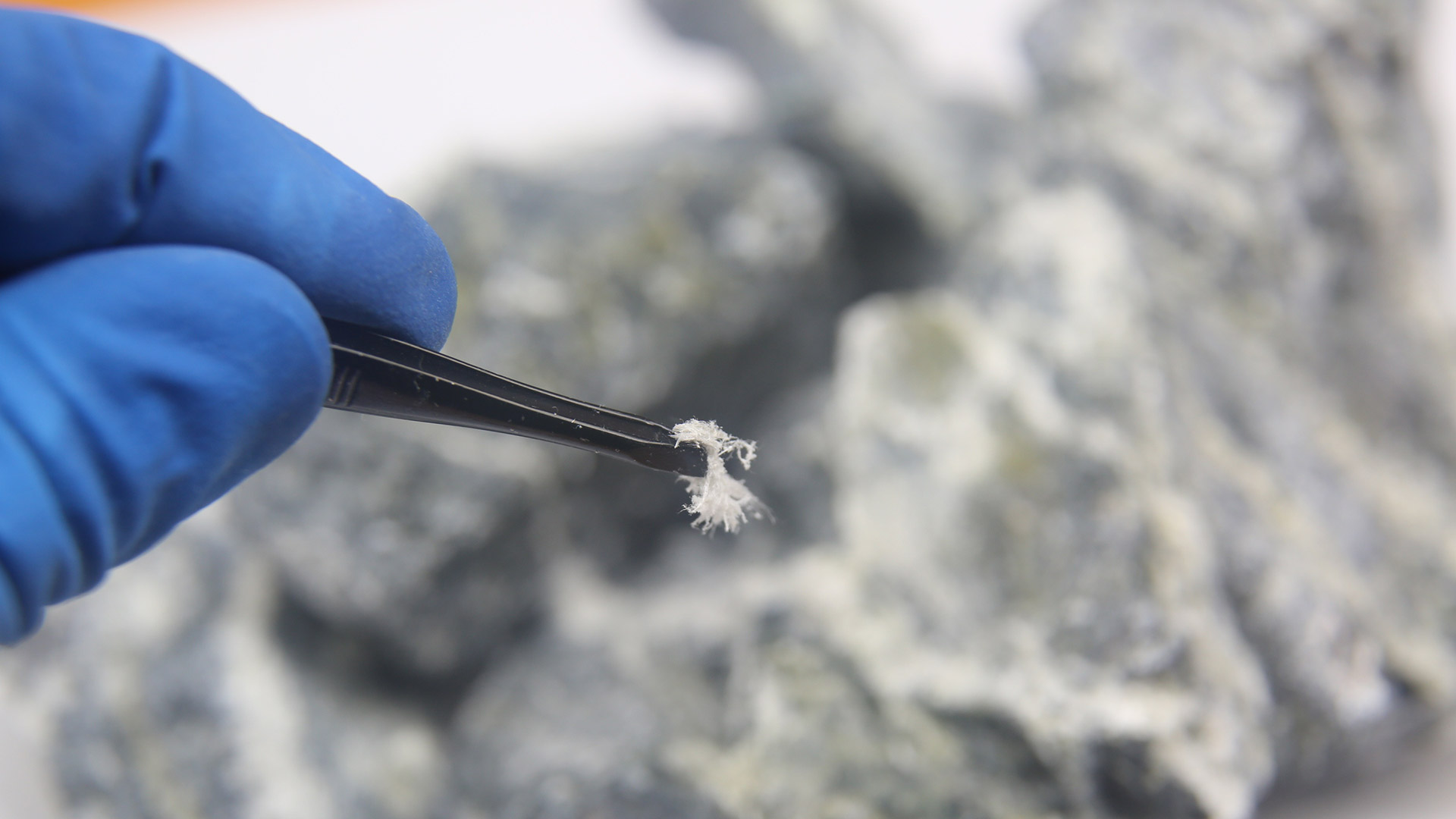
The asbestos course looks at how to manage asbestos in the workplace and recognise the risks.
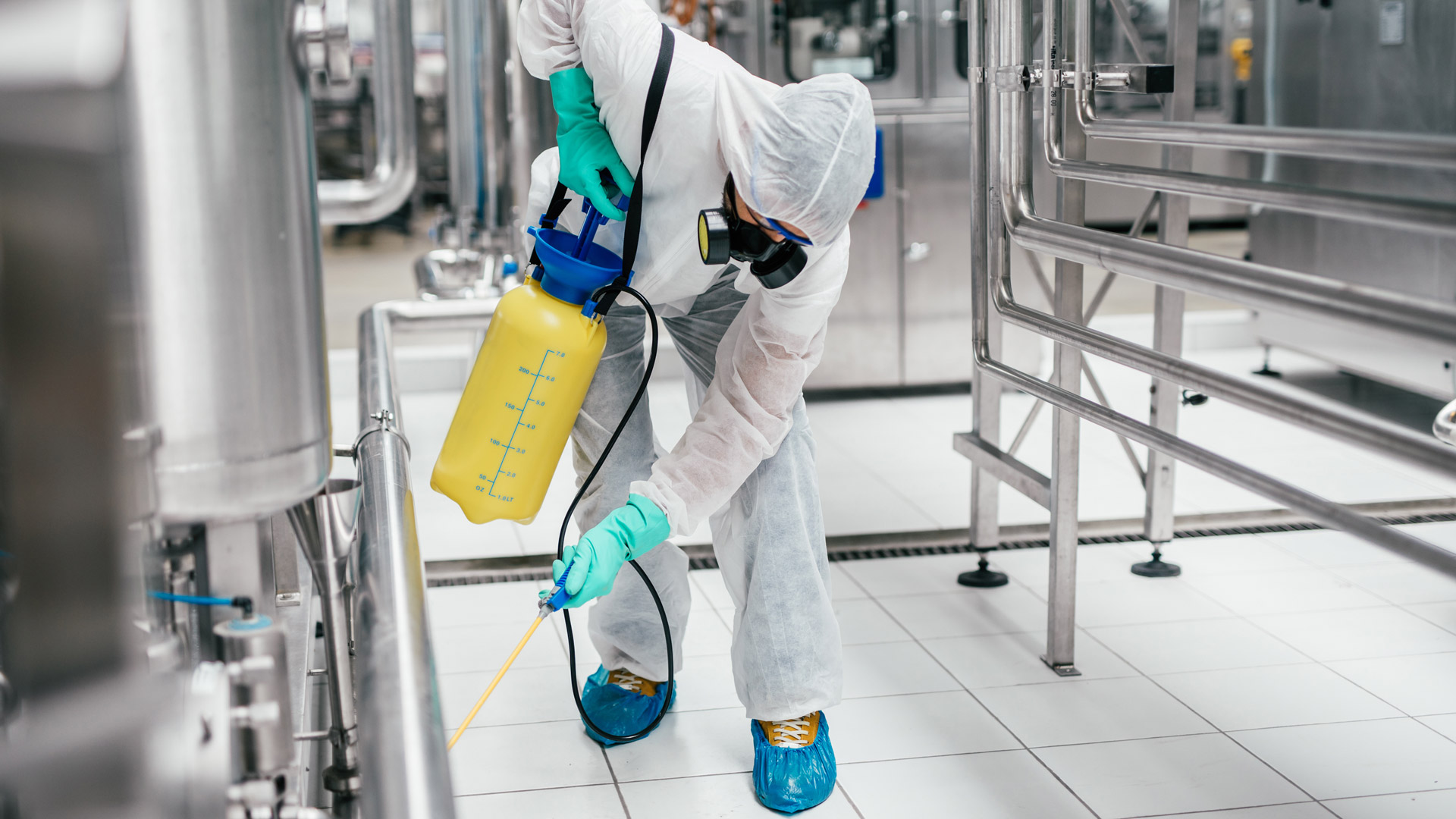
The Control of Substances Hazardous to Health (COSHH) course helps learners carry out work involving hazardous substances safely.
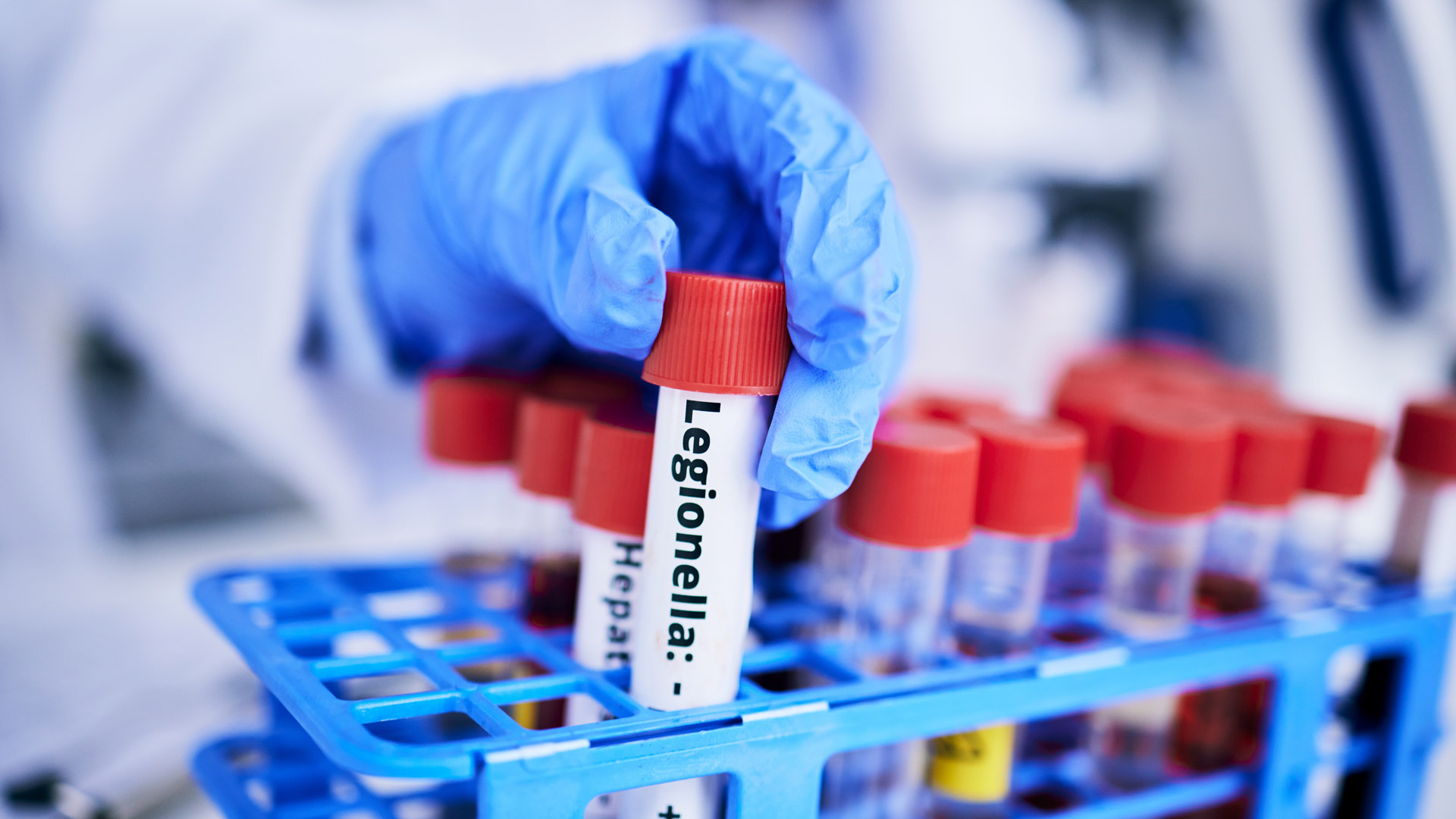
The Legionella course ensures people understand the risk of legionella and are aware of the requirements of the L8 ACoP.
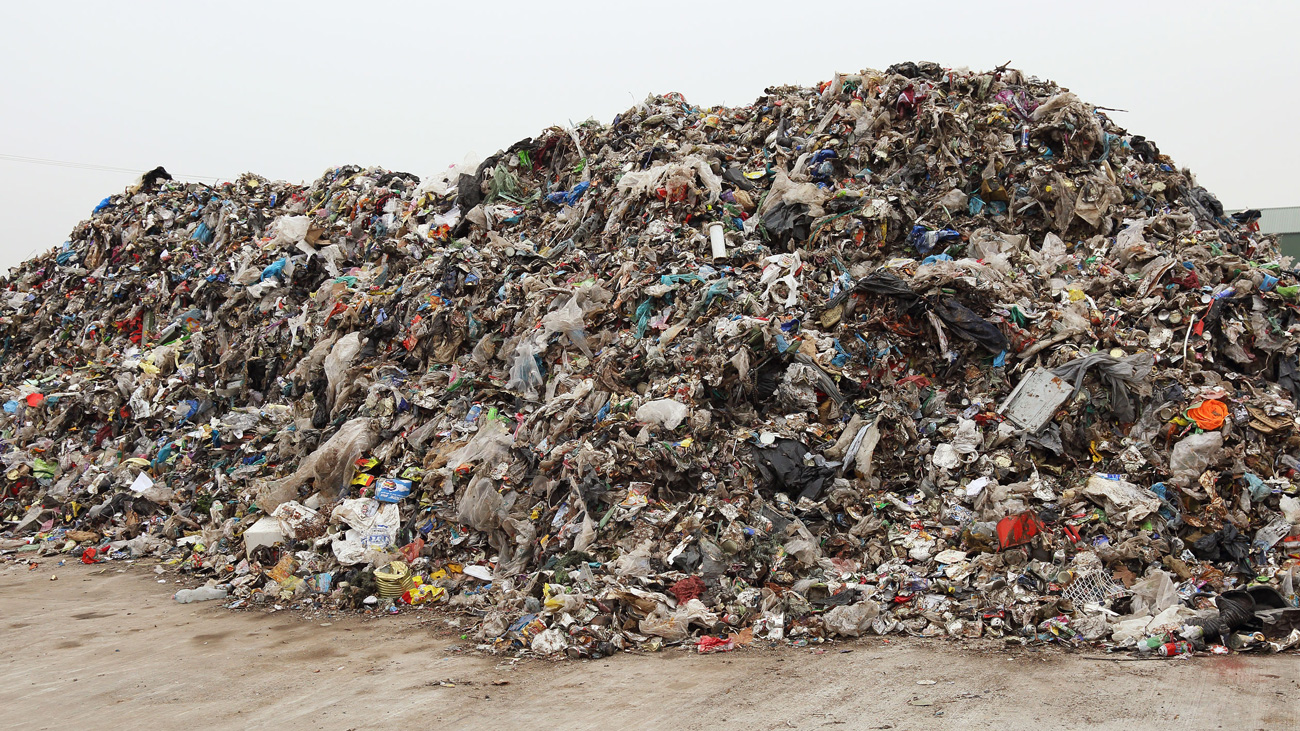
A survey of nearly 1,700 people across the recycling and waste management sector by the Environmental Services Association (ESA) has suggested the ind...
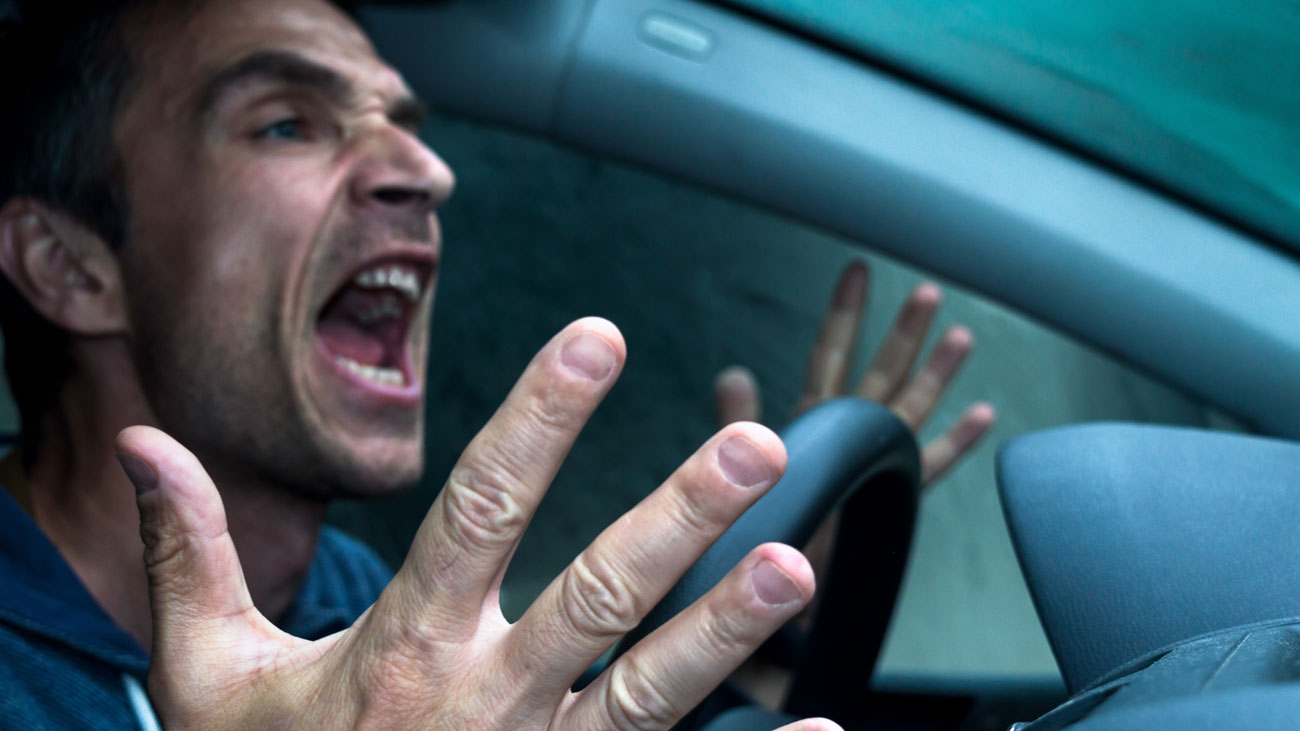
Friday is the most hazardous day of the week for fleet drivers with the highest number of accidents, speeding events, and incidences of aggressive dri...
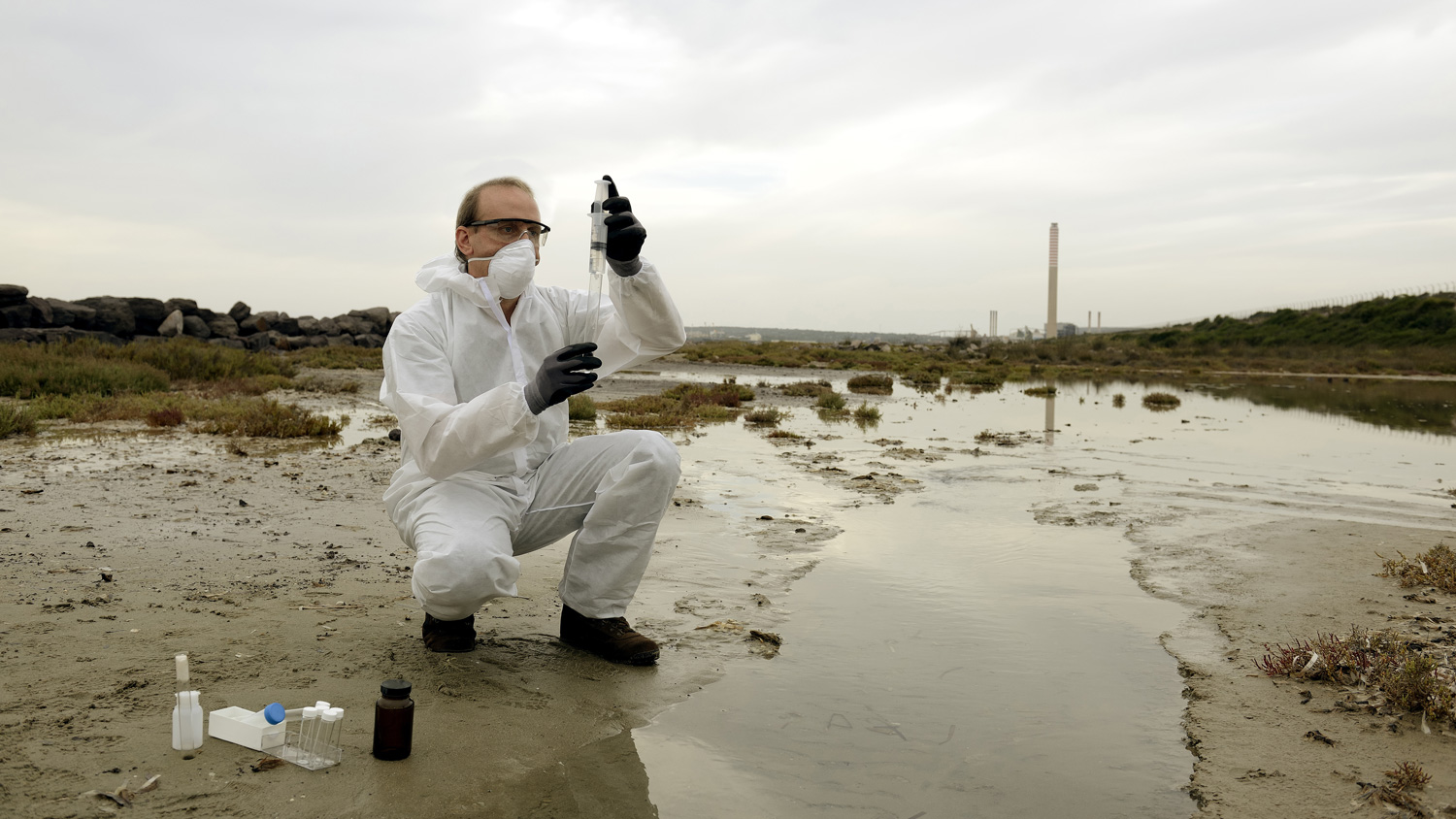
The UK government has announced it will not match new EU restrictions on various potentially hazardous chemicals, including the “rubber crumbs” used t...
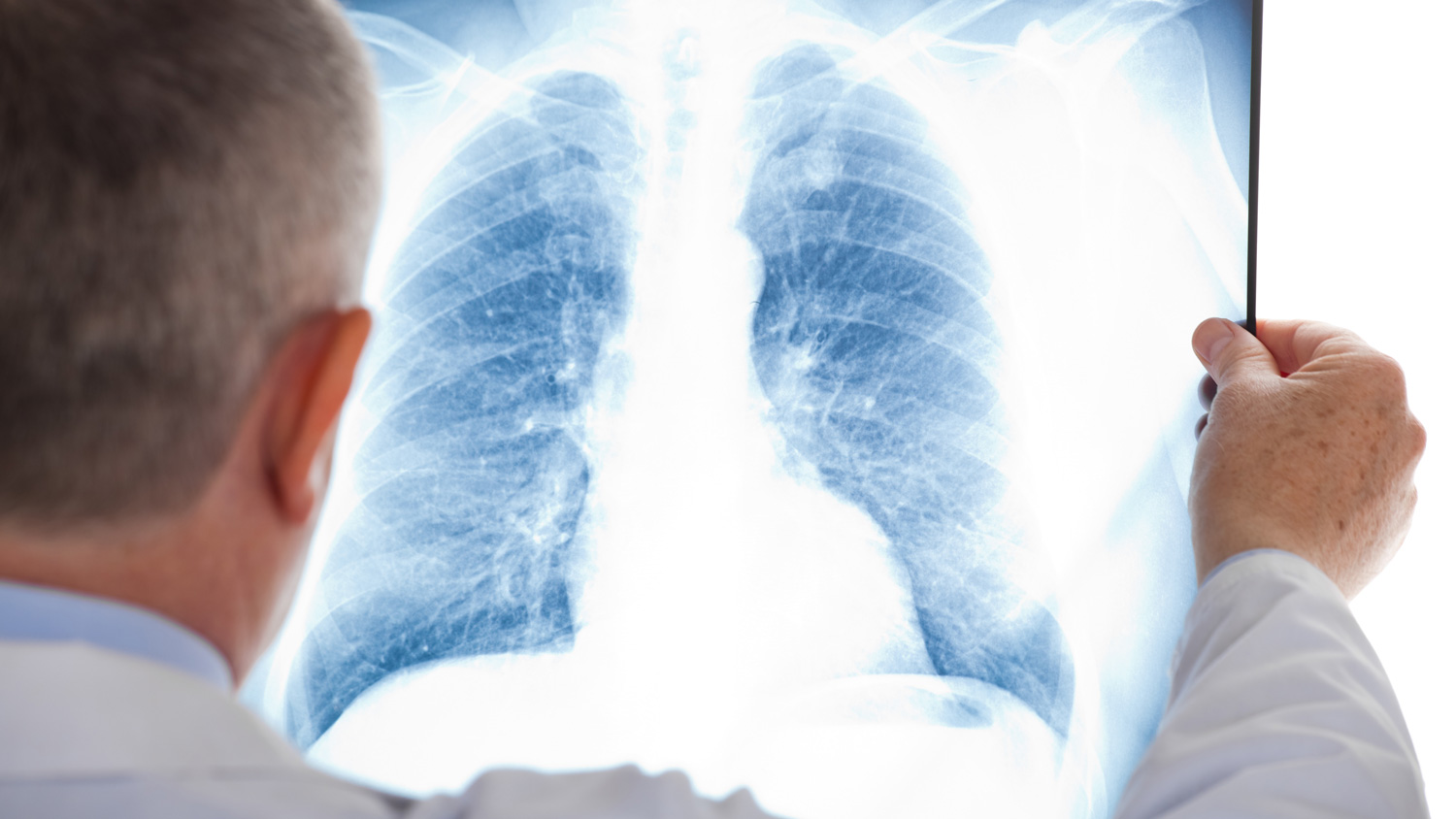
Global Asbestos Awareness Week 2023, organised by the Asbestos Disease Awareness Organisation, takes place this week (1-7 April), aiming to raise awar...