Everyone can make errors, no matter how well trained and motivated they are. However, in the workplace, the consequences of such human failure can be severe. Analysis of accidents and incidents shows that human failure contributes to almost all accidents and exposures to substances hazardous to health. Many major accidents - such as Texas City, Piper Alpha and Chernobyl - were initiated by human failure. In order to avoid accidents and ill health, companies need to manage human failure as robustly as the technical and engineering measures they use for that purpose.
The HSE says the challenge is to develop error-tolerant systems and to prevent errors from initiating; to manage human error proactively it should be addressed as part of the risk assessment process, where:
- Significant potential human errors are identified.
- Those factors that make errors more or less likely are identified (such as poor design, distraction, time pressure, workload, competence, morale, noise levels and communication systems).
- Control measures are devised and implemented, preferably by redesign of the task or equipment.
Types of human failure
It is important to be aware that human failure is not random; understanding why errors occur and the different factors that make them worse will help you develop more effective controls. There are two main types of human failure: errors and violations.
The HSE defines human error as an action or decision that was not intended; a violation is a deliberate deviation from a rule or procedure.
Some errors are slips or lapses, often "actions that were not as planned" or unintended actions. They occur during a familiar task and include slips (e.g. pressing the wrong button or reading the wrong gauge) and lapses (e.g. forgetting to carry out a step in a procedure). These types of error occur commonly in highly-trained procedures where the person carrying them out does not need to concentrate on what they are doing. These cannot be eliminated by training, but improved design can reduce their likelihood and provide a more error-tolerant system.
Other errors are mistakes or errors of judgement or decision-making where the "intended actions are wrong", i.e. where we do the wrong thing, believing it to be right. These tend to occur in situations where the person does not know the correct way of carrying out a task, either because it is new and unexpected, or because they have not been properly trained (or both). Often in such circumstances, people fall back on remembered rules from similar situations, which may not be correct. Training based on good procedures is the key to avoiding mistakes.
Violations (non-compliances, circumventions, shortcuts and work-arounds) differ from the above in that they are intentional but usually well-meaning failures where the person deliberately does not carry out the procedure correctly. They are rarely malicious (sabotage) and usually result from an intention to get the job done as efficiently as possible. They often occur where the equipment or task has been poorly designed and/or maintained. Mistakes resulting from poor training (i.e. people have not been properly trained in the safe working procedure) are often mistaken for violations. Understanding that violations are occurring and the reason for them is necessary if effective means for avoiding them are to be introduced. Peer pressure, unworkable rules and incomplete understanding can give rise to violations.
The HSE advises there are several ways to manage violations, including designing violations out, taking steps to increase their detection, ensuring that rules and procedures are relevant/practical and explaining the rationale behind certain rules. Involving the workforce in drawing up rules increases their acceptance. Getting to the root cause of any violation is the key to understanding, and hence preventing, the violation.
Understanding these different types of human failure can help identify control measures but the HSE warns you need to be careful to not oversimplify the situation. In some cases, it can be difficult to place an error in a single category – it may result from a slip or a mistake, for example. There may be a combination of underlying causes requiring a combination of preventative measures. It may also be useful to think about whether the failure is an error of omission (forgetting or missing out a key step) or an error of commission (e.g. doing something out of sequence or using the wrong control), and taking action to prevent that type of error.
Key principles in managing human failure
The HSE highlights the following key points:
- Human failure is normal and predictable. It can be identified and managed.
- Industry should tackle error reduction in a structured and proactive way, with as much rigour as the technical aspects of safety. Managing human failure should be integral to the safety management system.
- A poorly designed activity might be prone to a combination of errors and more than one solution may be necessary.
- Involve workers in design of tasks and procedures.
- Risk assessment should identify where human failure can occur in safety critical tasks, the performance influencing factors which might make it more likely, and the control measures necessary to prevent it.
- Incident Investigations should seek to identify why individuals have failed rather than stopping at 'operator error'.
Common pitfalls in managing human failure
There is more to managing human failure in complex systems than simply considering the actions of individual operators. However, there is obvious merit in managing the performance of the personnel who play an important role in preventing and controlling risks, as long as the context in which this behaviour occurs is also considered.
When assessing the role of people in carrying out a task, the HSE says, be careful that you do not:
- Treat operators as if they are superhuman, able to intervene heroically in emergencies.
- Assume that an operator will always be present, detect a problem and immediately take appropriate action.
- Assume that people will always follow procedures.
- Rely on operators being well-trained, when it is not clear how the training provided relates to accident prevention or control.
- Rely on training to effectively tackle slips/lapses.
- State that operators are highly motivated and thus not prone to unintentional failures or deliberate violations.
- Ignore the human component completely and failing to discuss human performance at all in risk assessments.
- Inappropriately apply techniques, such as detailing every task on site and therefore losing sight of targeting resources where they will be most effective.
- In quantitative risk assessment, provide precise probabilities of human failure (usually indicating very low chance of failure) without documenting assumptions/data sources.
Analysis of accidents and incidents, and the causes behind them, is explored in detail in the IOSH Managing Safely course. Designed to provide all managers with the confidence to apply knowledge to the workplace, this course is ideal for those who want to increase their health and safety knowledge and inspire their teams to work more safely. Find out more here.
You may also be interested in
RELATED CONTENT
RELATED COURSES
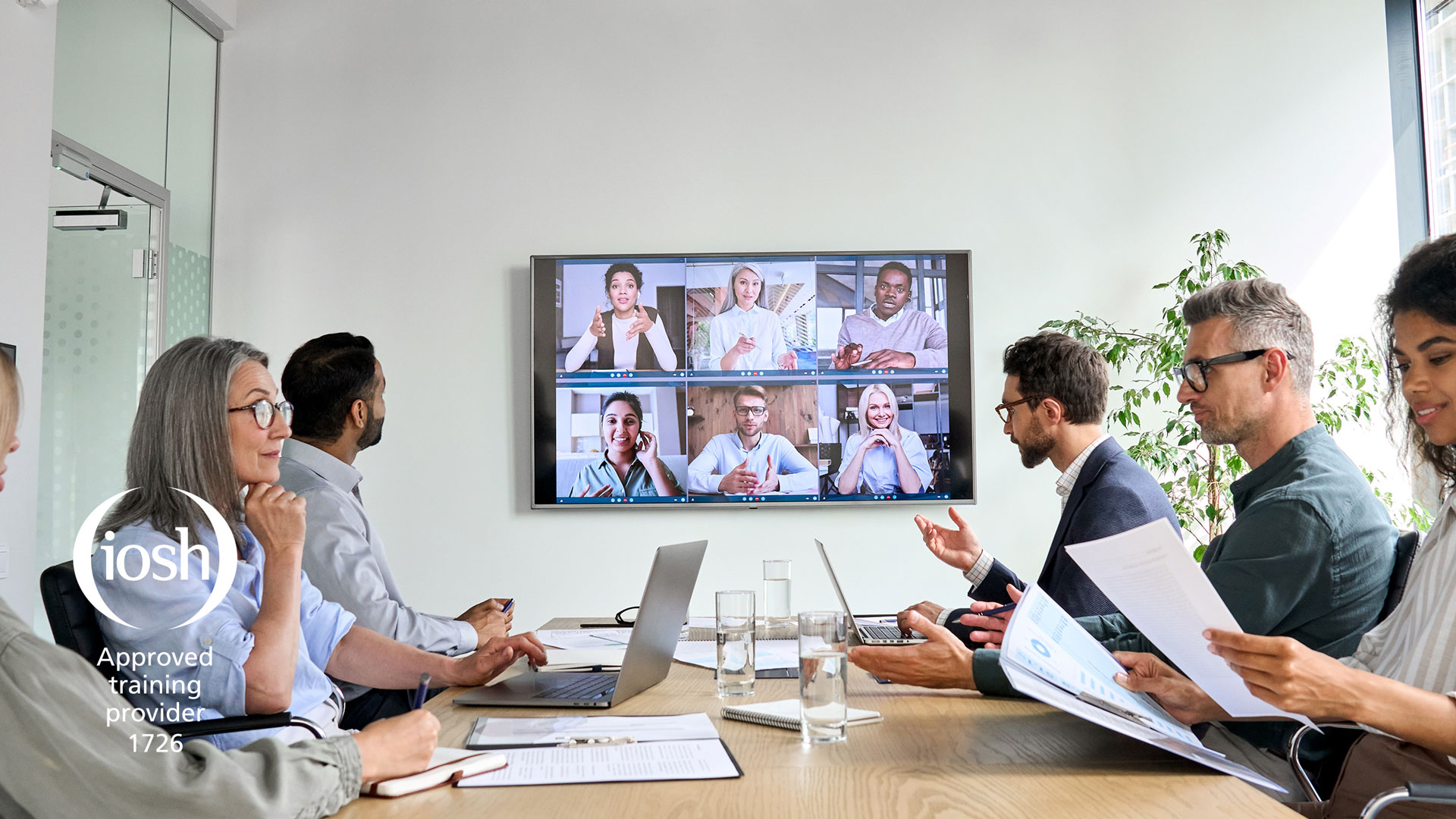
IOSH Safety for Executives and Directors is designed for those who have operational or strategic accountability for a company.
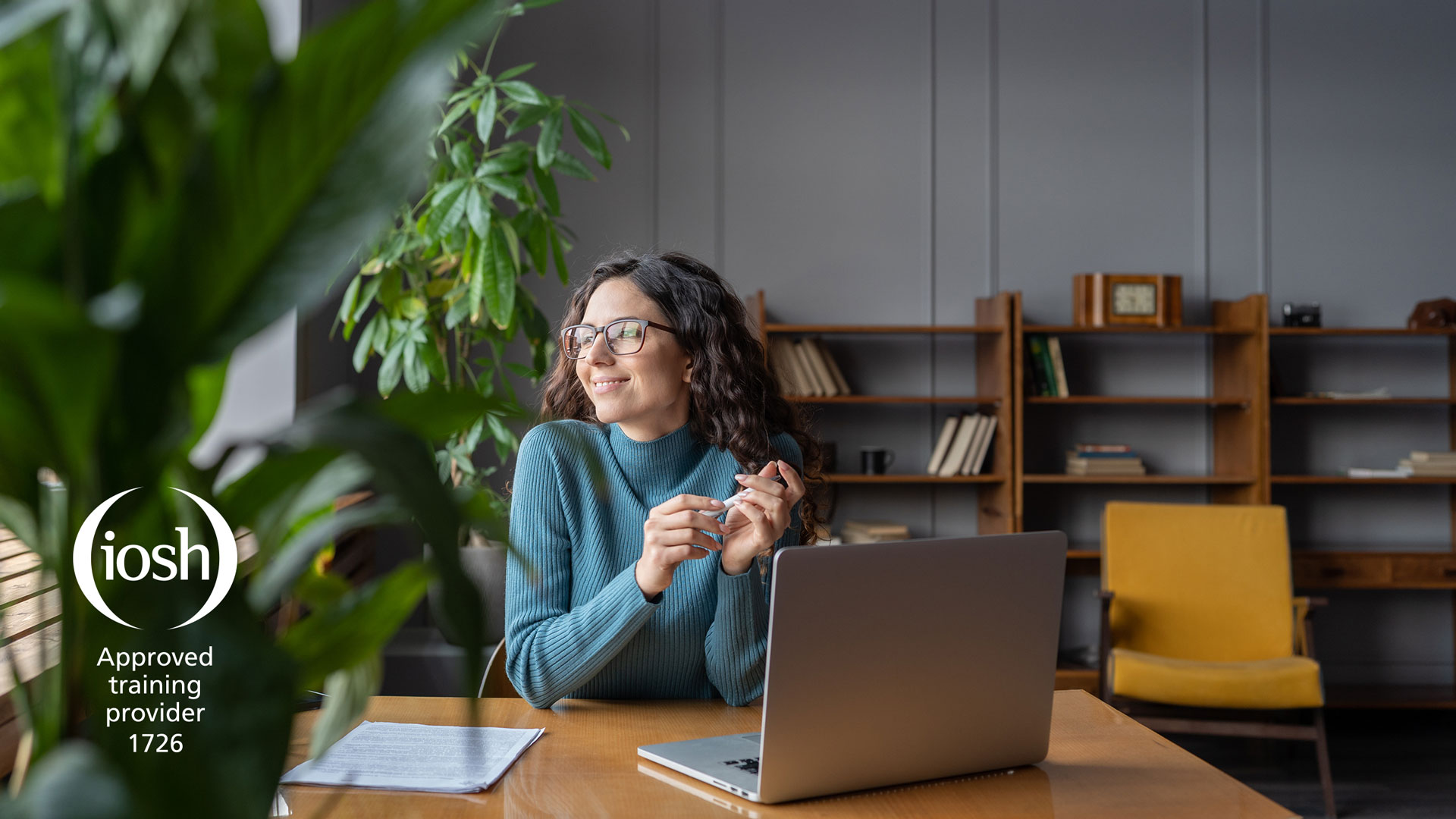
IOSH Managing Occupational Health and Wellbeing is designed to help managers improve health and wellbeing in their organisation.
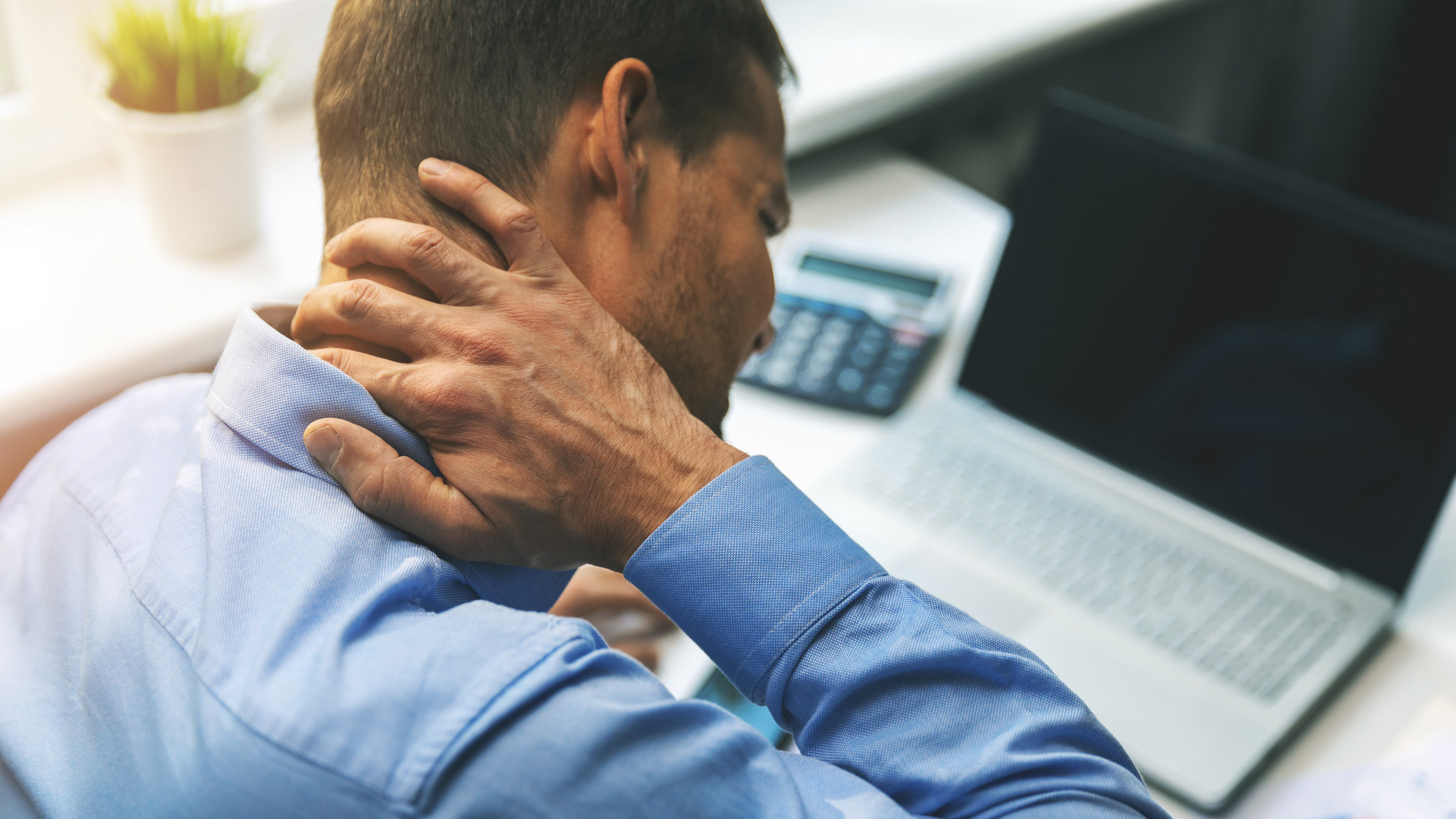
The DSE course covers the risks of display screen equipment use and identifies ways to reduce the risk of injury or ill health.
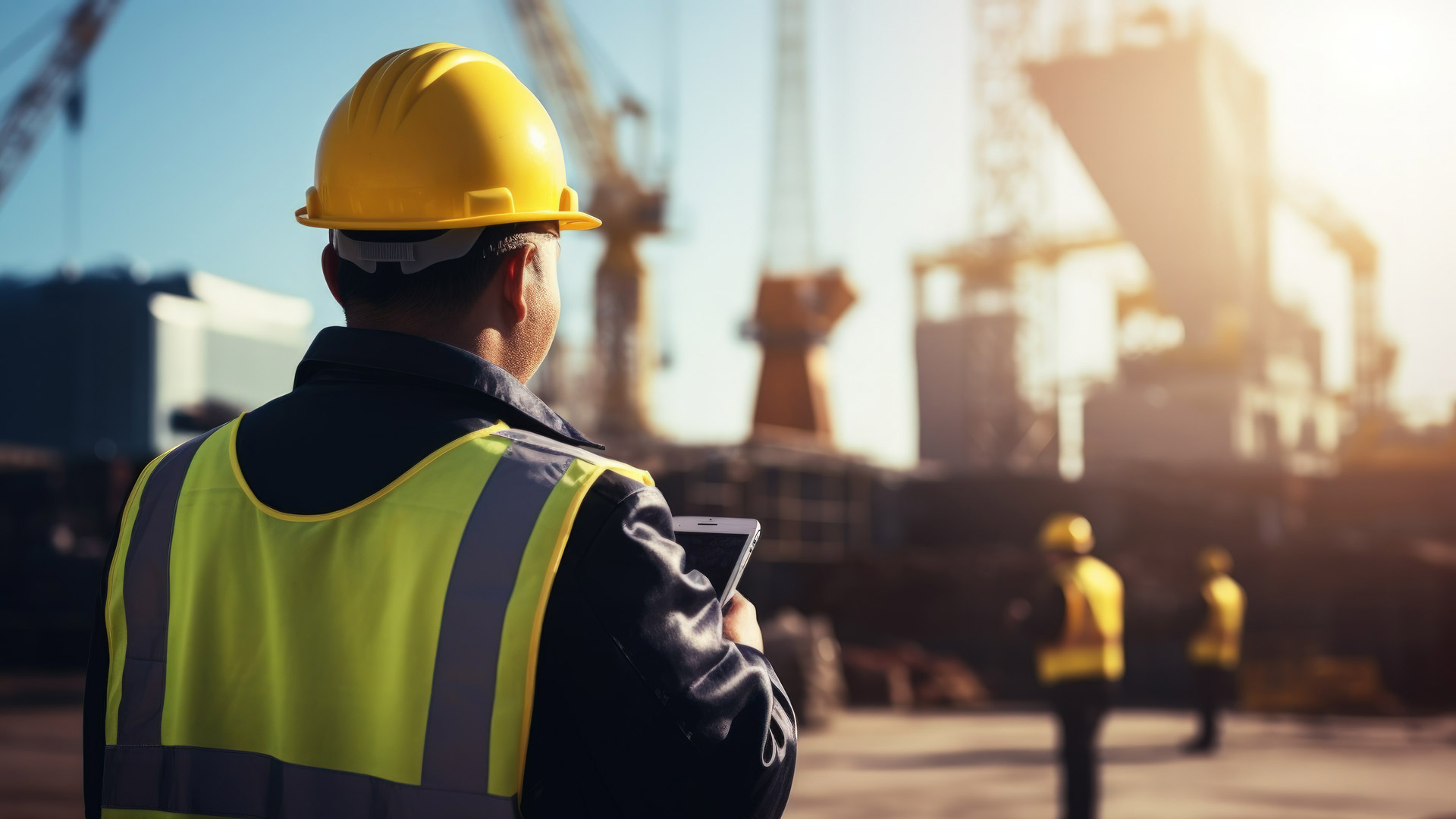
The Selection and control of contractors course is designed for individuals who are responsible for selecting and managing contractors in the workplac...
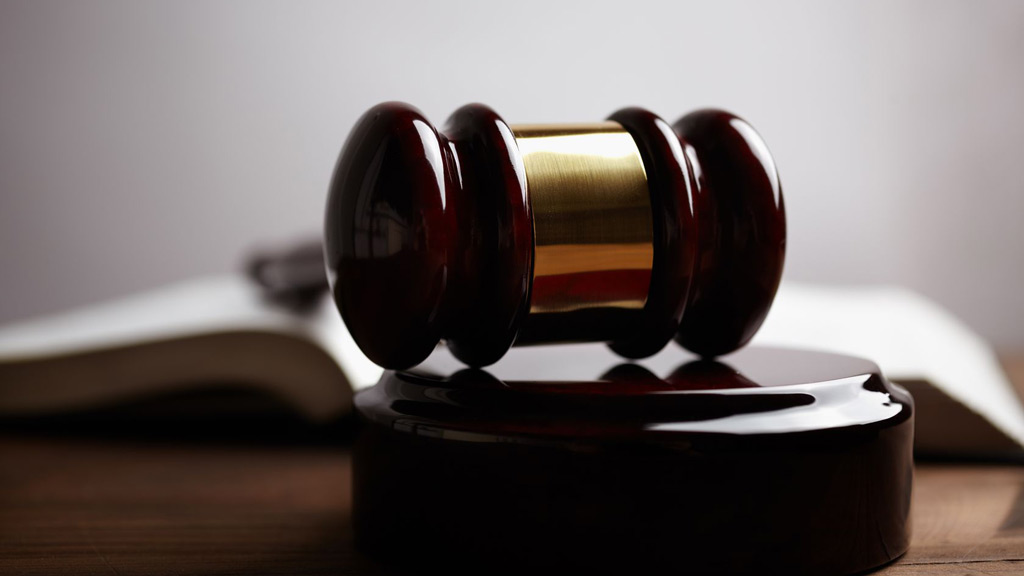
The decision made by P&O Ferries to sack 800 workers without notice appears to have broken UK employment law, the prime minister has said. If found gu...
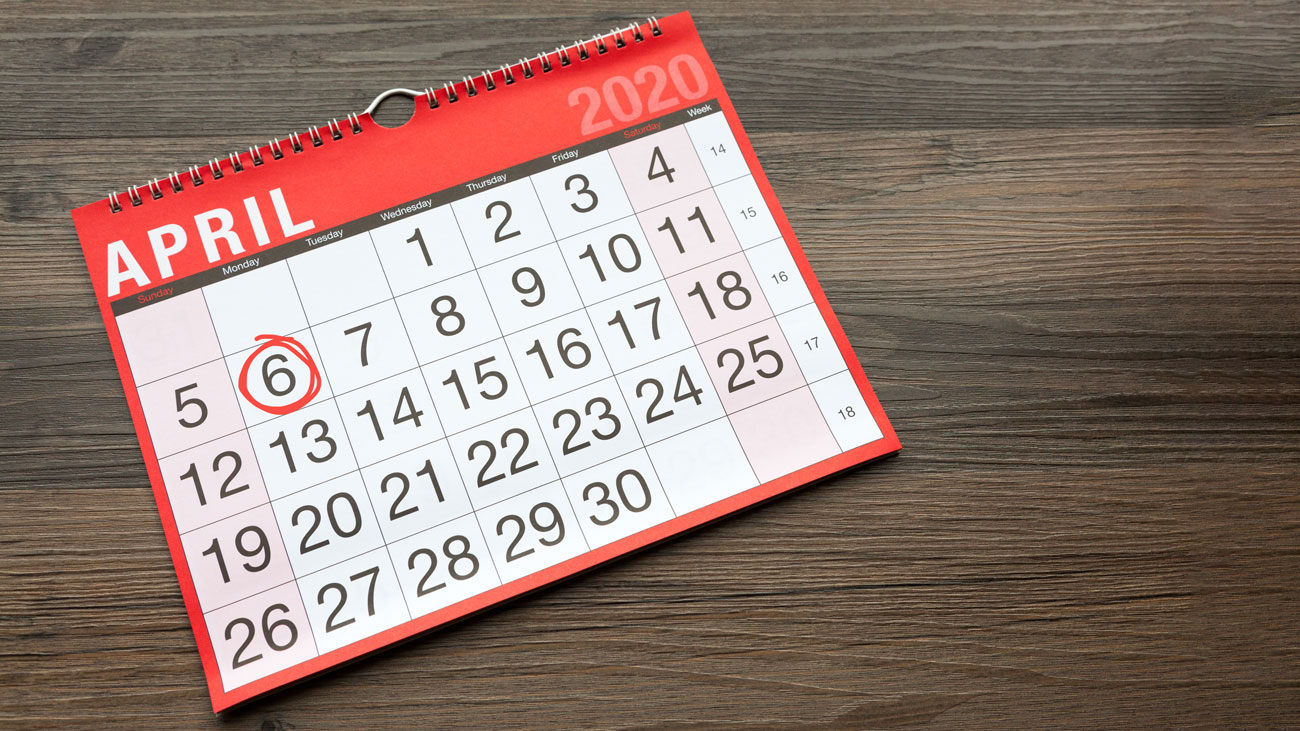
On 6 April each year, new and amended employment laws and deadlines come into force.
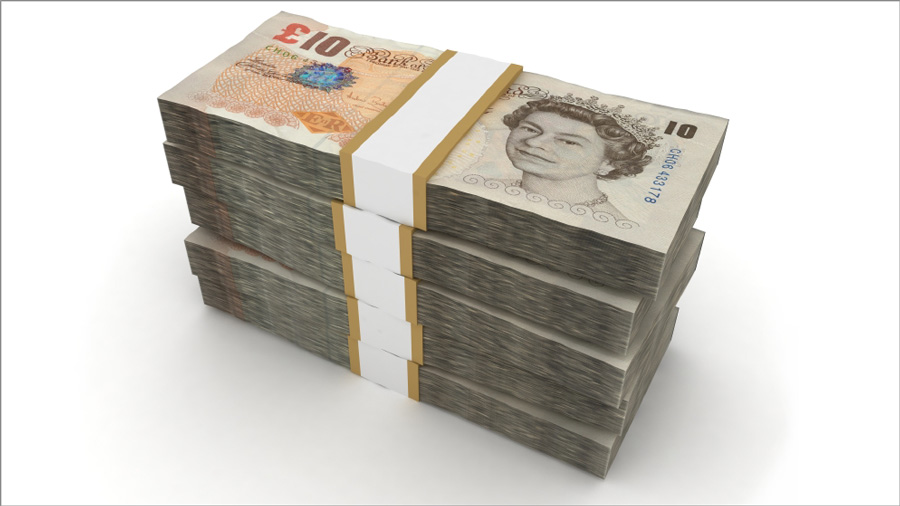
It’s that time of the year when employment law changes traditionally take effect, and this year there have been significant increases in several rates...
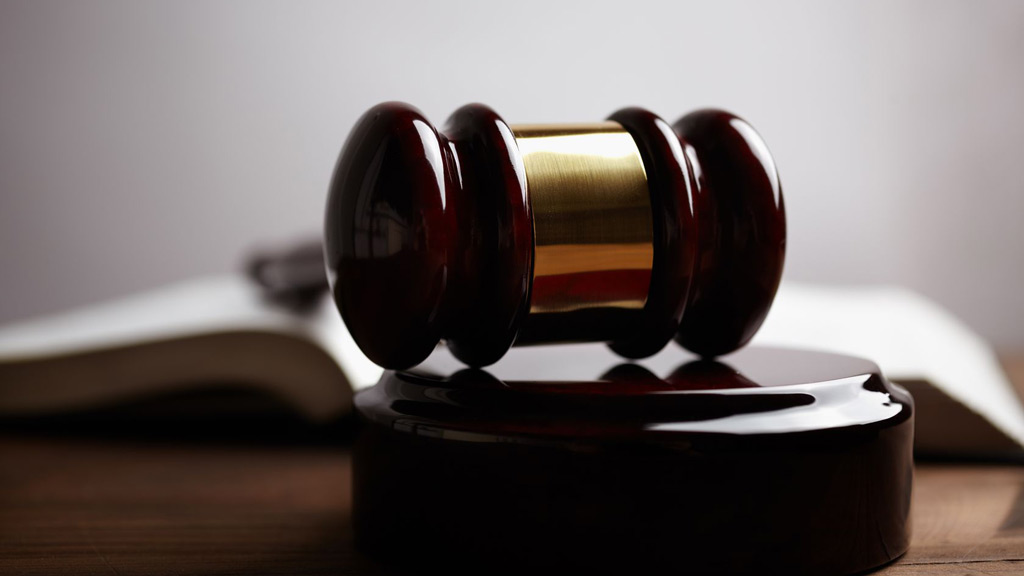
Following a nine-year-long legal battle, former Pimlico Plumbers engineer Gary Smith has lost his Employment Appeals Tribunal (EAT) case over his enti...