The manufacturing sector in the UK is a cornerstone of the economy, offering numerous opportunities for young workers. However, this industry presents various hazards, making the safety of young employees a top priority. This article explores the measures necessary to safeguard young workers in UK manufacturing, highlighting the risks, legal framework, and best practices for creating a safe working environment.
Understanding the risks
Young workers, defined in the UK as those aged 16-24, are particularly vulnerable in manufacturing settings due to their inexperience and, often, lack of training. Common risks include:
- Machinery and equipment. Young workers may be tasked with operating complex machinery, which can lead to severe injuries if not handled properly.
- Chemical exposure. Manufacturing often involves the use of hazardous substances, and without proper training, young workers might not fully understand the dangers of exposure.
- Manual handling. Improper lifting techniques and repetitive tasks can result in musculoskeletal injuries, which are common in physically demanding jobs.
- Slips, trips and falls. The manufacturing environment frequently has wet or uneven surfaces, increasing the likelihood of accidents.
Legal framework and regulations
The UK has stringent regulations to protect young workers, primarily governed by the Health and Safety at Work Act 1974 and specific guidelines under the Health and Safety (Young Persons) Regulations 1997. Key provisions include:
- Risk assessments. Employers must carry out thorough risk assessments considering the specific vulnerabilities of young workers.
- Restricted work. There are restrictions on the types of work young people can undertake, particularly concerning hazardous activities.
- Work hours. Regulations limit the number of hours and types of shifts young workers can work, especially those still in compulsory education.
- Training and supervision. Adequate training and supervision are mandatory to ensure young workers can perform their duties safely.
Best practices for ensuring safety
- Tailored training programmes. Training should be comprehensive and specifically designed for young workers, emphasising the recognition of hazards, safe working practices, and emergency procedures. Interactive and hands-on training sessions can significantly enhance understanding and retention.
- Mentorship and supervision. Assigning experienced mentors to young workers provides them with guidance and a point of contact for safety concerns. Regular supervision helps ensure adherence to safety protocols.
- Clear and effective communication. Safety instructions should be communicated clearly and concisely. Using visual aids, simple language, and practical demonstrations can help young workers understand safety measures better.
- Fostering a safety culture. Encouraging a culture where safety is prioritised and valued can make a significant difference. Young workers should feel comfortable reporting hazards and participating in safety discussions.
- Ergonomic interventions. Implementing ergonomic solutions can reduce the risk of injuries. Adjustable workstations, appropriate tools, and mechanical aids are essential to minimise physical strain.
- Provision of Personal Protective Equipment (PPE). Ensure that young workers are provided with the necessary PPE and trained in its correct use. Regular checks should be conducted to ensure PPE is in good condition and used properly.
The role of technology
Technological advancements can play a crucial role in enhancing the safety of young workers in manufacturing. Examples include:
- Wearable technology. Wearable devices that monitor environmental conditions and workers’ health can provide real-time alerts to prevent accidents.
- Automation and robotics. Utilising robots for hazardous tasks can significantly reduce the risk of injury. Robots can handle dangerous materials and perform repetitive tasks, minimising young workers' exposure to risks.
- Virtual Reality (VR) training. VR technology can simulate hazardous scenarios, allowing young workers to practice safety procedures in a controlled environment.
Conclusion
Protecting young workers in the UK manufacturing sector requires a comprehensive approach that includes strict adherence to legal regulations, robust training programmes, effective communication, and the integration of advanced technologies. Employers must prioritise the safety of young workers, recognising that a safe working environment not only complies with legal obligations but also enhances overall productivity and morale. By investing in the safety and wellbeing of young workers, the manufacturing industry can foster a more secure and efficient workforce.
You might also be interested in
RELATED CONTENT
RELATED COURSES
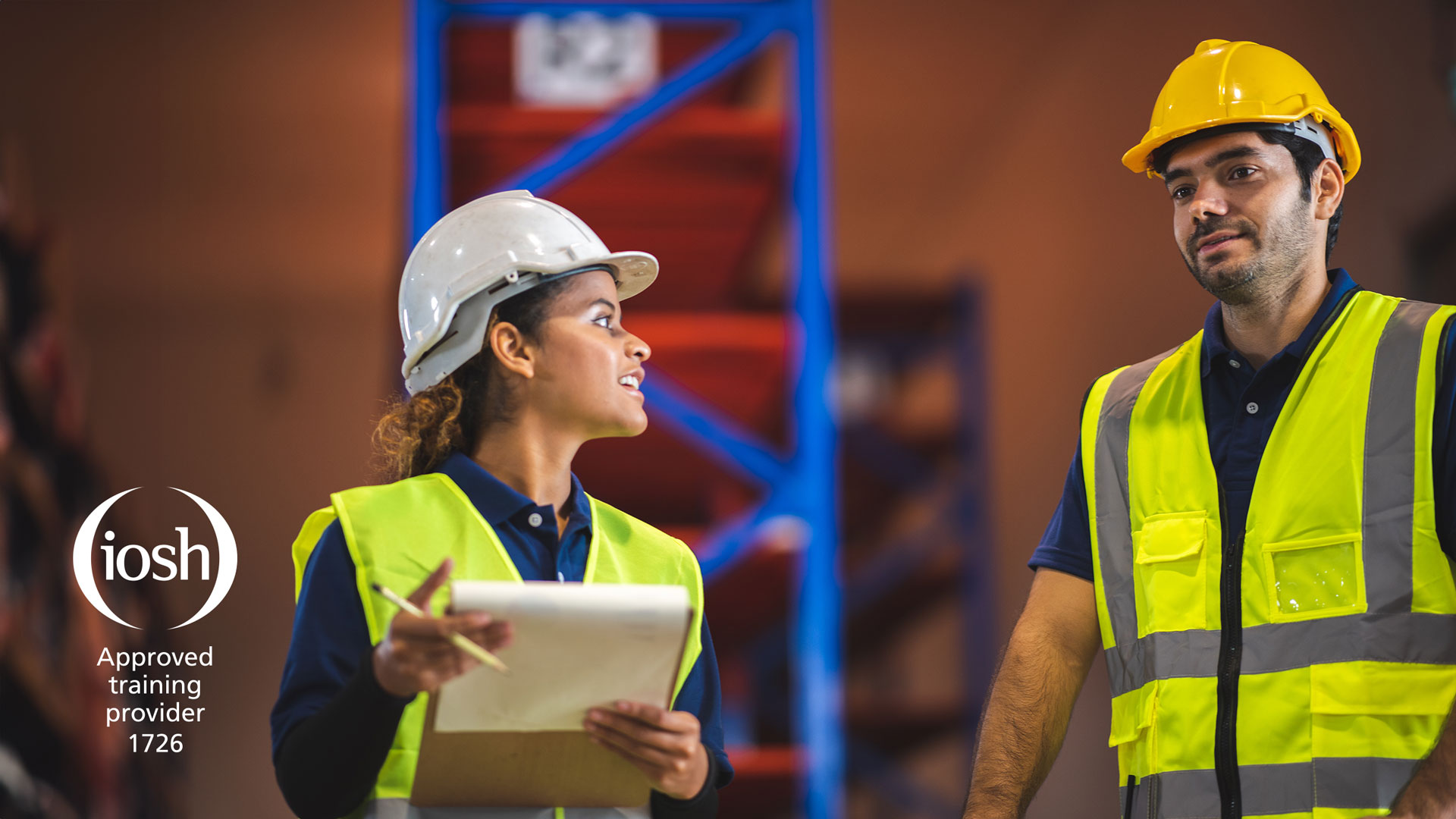
The world’s best-known health and safety certificate, designed for managers and supervisors in any sector or organisation.
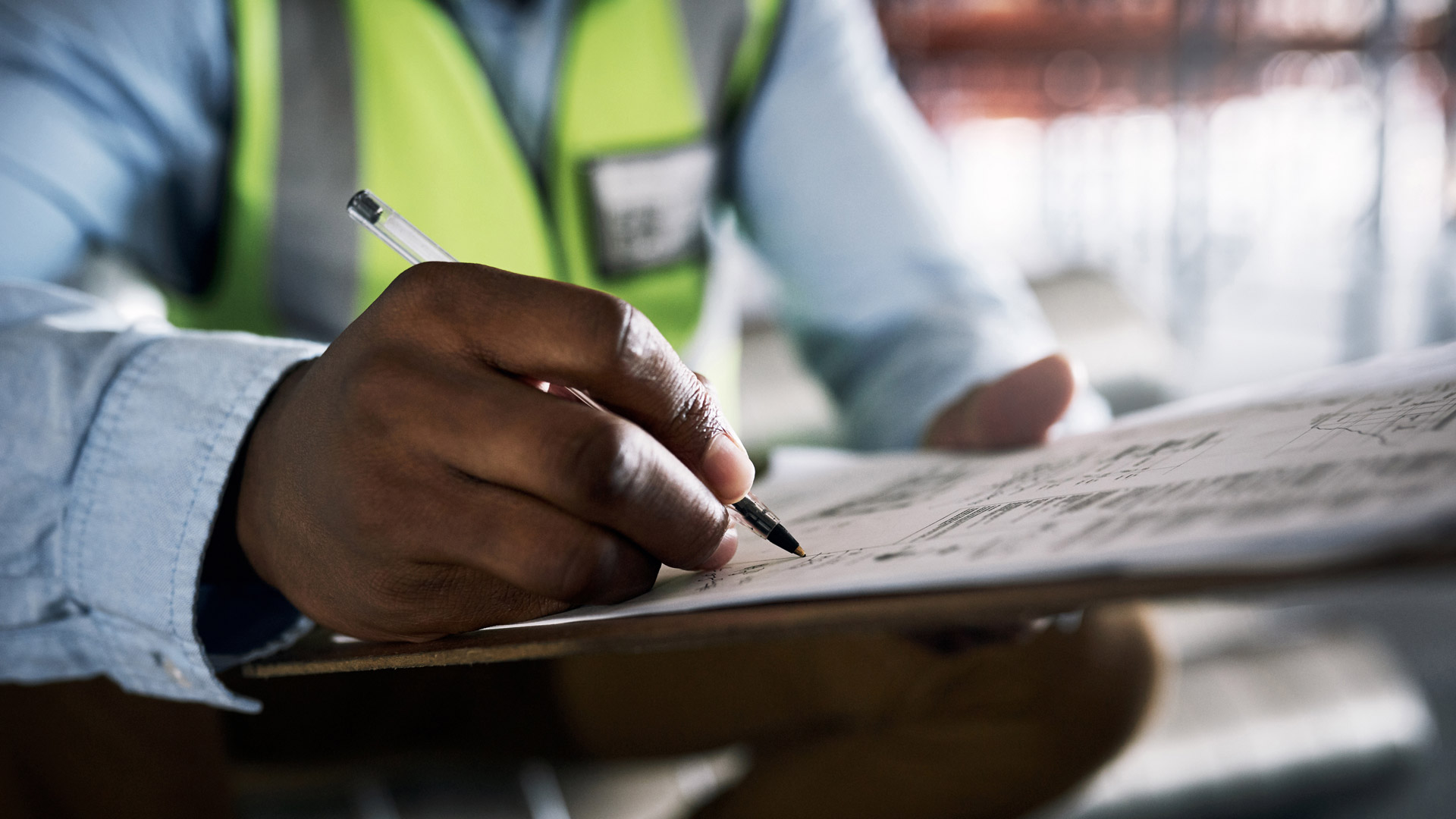
The Risk Assessment and Method Statement (RAMS) course examines the HSE’s recognised five-step approach to risk assessment.
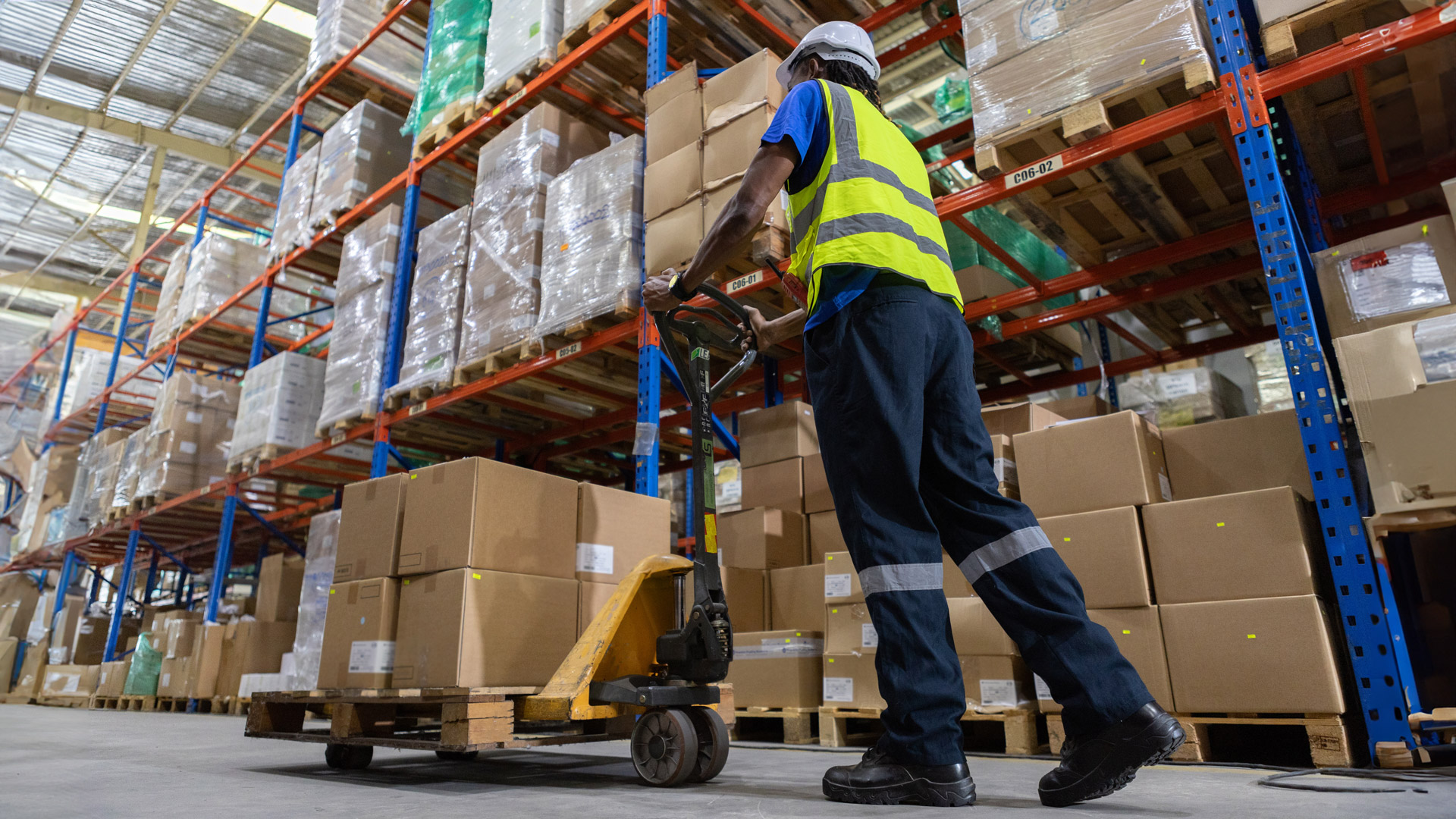
The Manual handling course helps learners understand the risks and dangers associated with lifting and handling in the workplace.
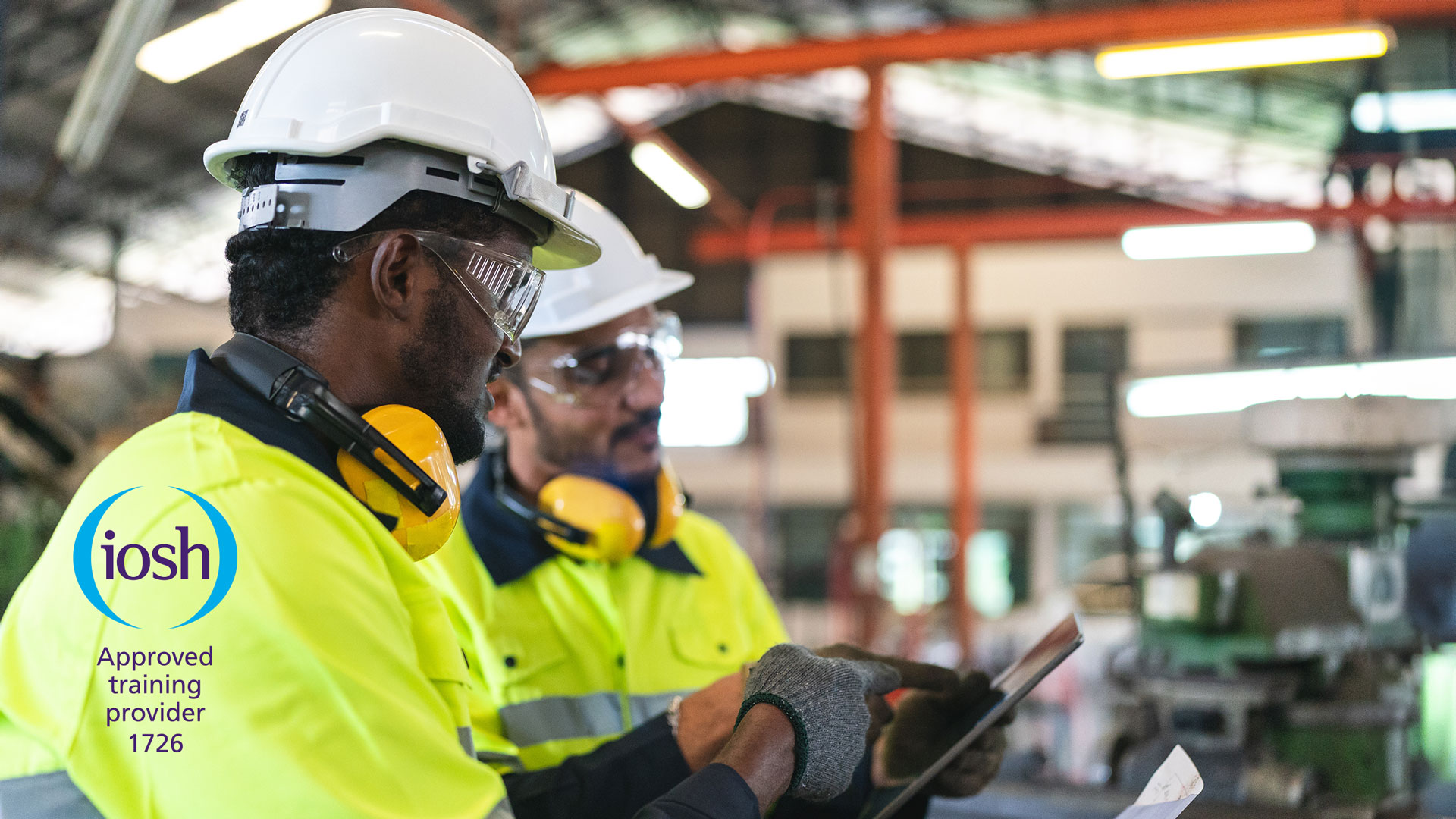
IOSH Working Safely is a one-day introductory health and safety training course for people at any level, in any sector.
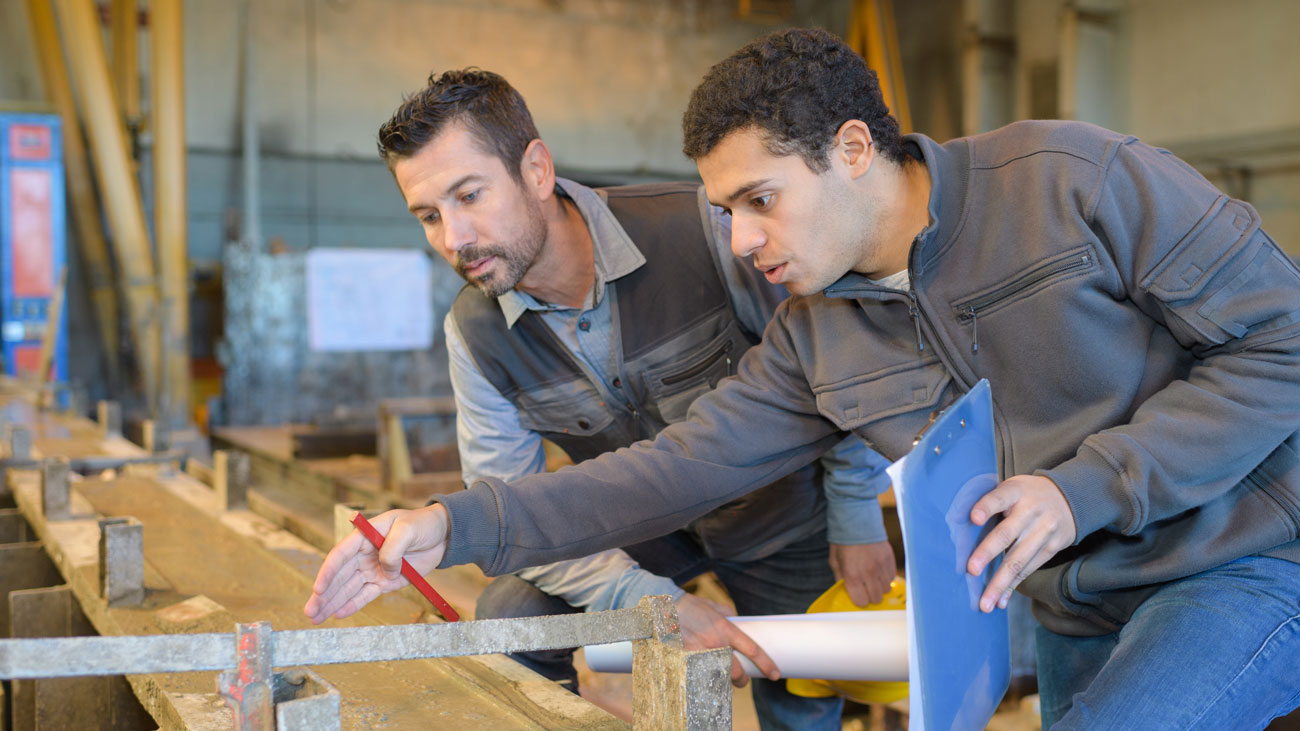
The prime minister has suggested the government could guarantee apprenticeships for all young people as part of efforts to boost employment as the cou...
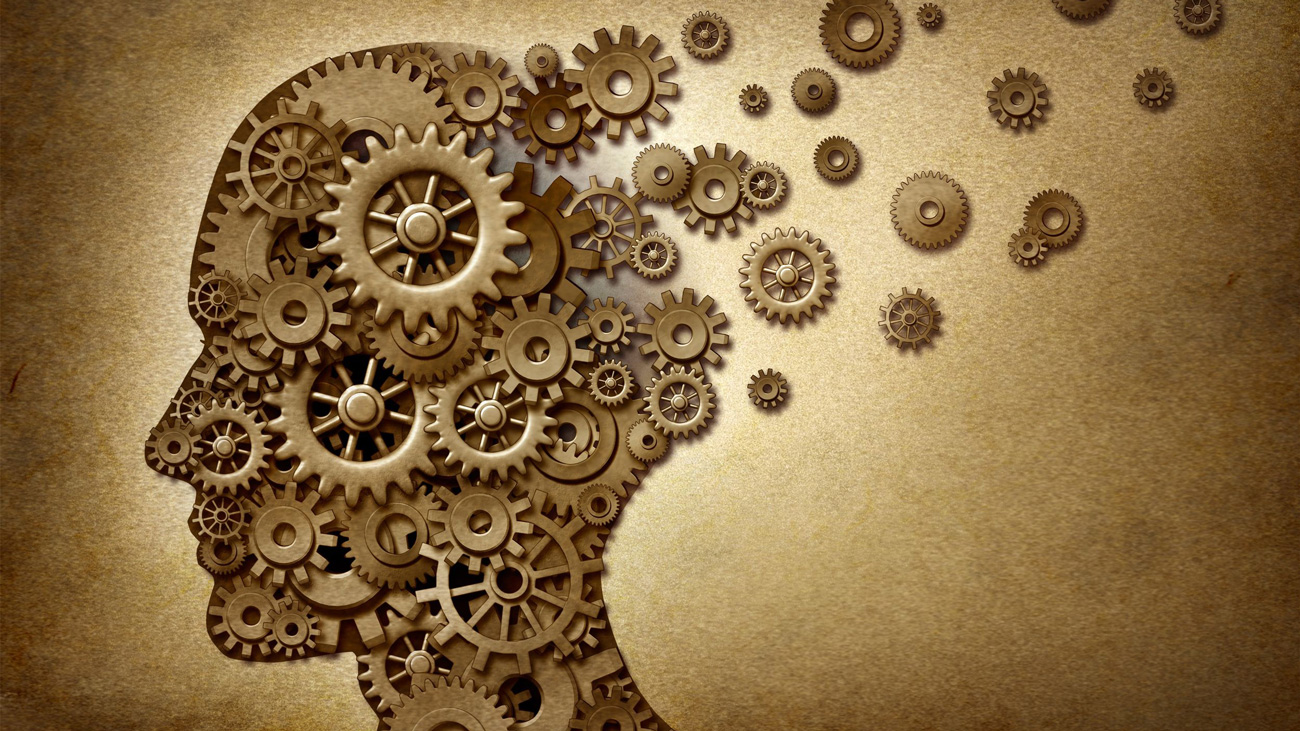
Many of us are aware of dementia in older generations; however, we may be less familiar with early onset dementia.
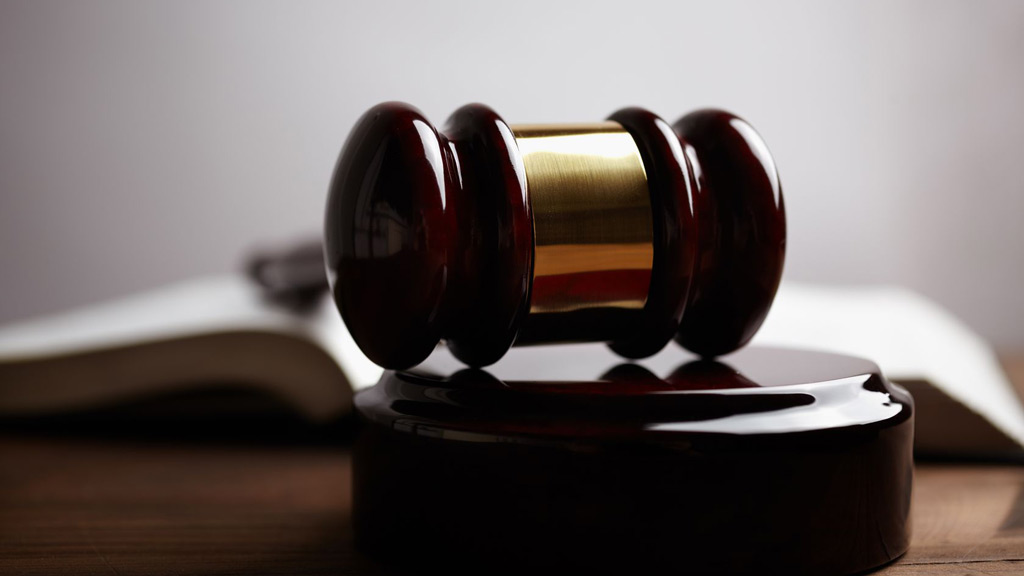
A 14-year-old schoolgirl has become Britain's youngest winner of an age discrimination claim after she was sacked for being too young.
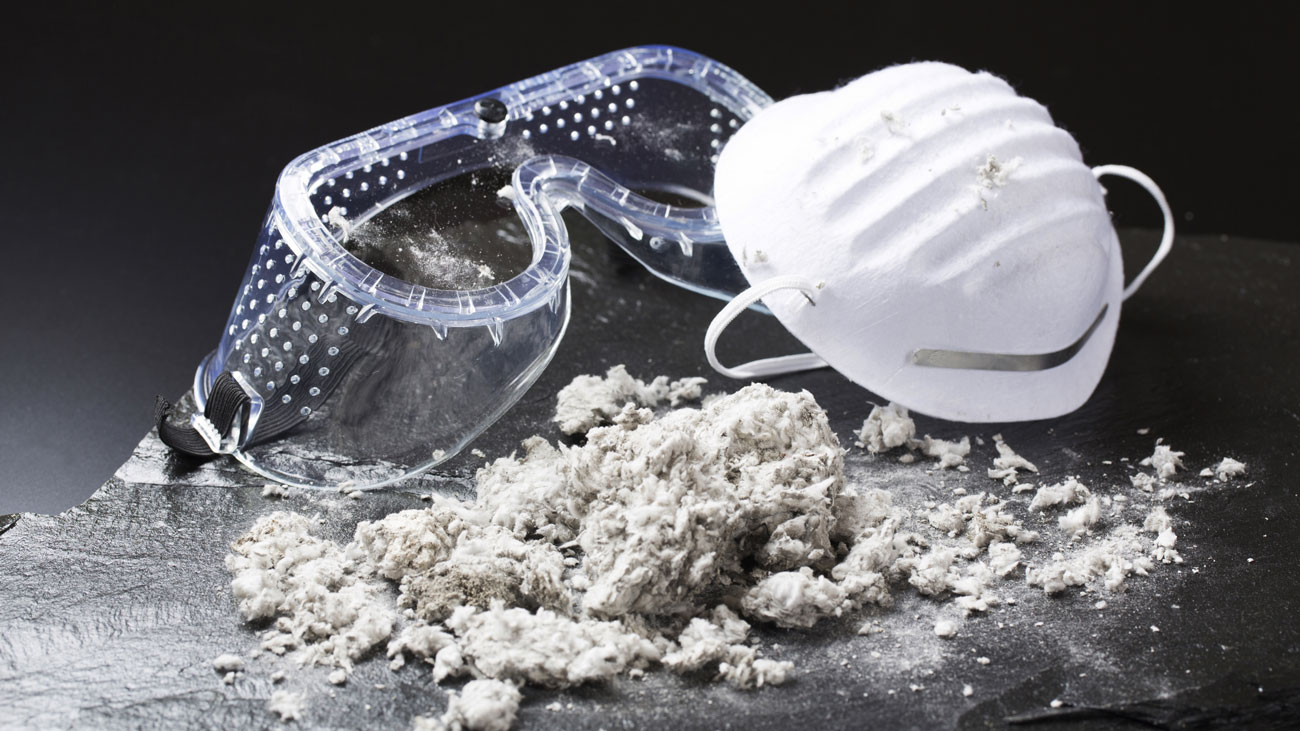
Millennials, gen Z workers and other younger people who work as plumbers, electricians, and in other trades need to take the risk of asbestos much mor...