A Dyson employee who was moving a 1.5 tonne milling machine has sustained injuries to his head and chest after it fell on top of him. The HSE found Barry Miles managed to avoid being crushed under the machine as it landed on a stack of toolboxes and concluded the company had failed to provide sufficient instructions and training for workers and had failed to assess and mitigate properly the risk of moving the machine.
Miles was moving the milling machine on 27 August 2019 when it fell on top of him. He sustained injuries to his head and chest but just about managed to avoid the machine falling completely on him. Whilst it was falling, the machine landed on a stack of toolboxes and the handle of an adjacent lathe machine.
The Health and Safety Executive’s investigation found that Dyson Technologies had failed to provide adequate information, instruction and training for its workers who were to manually handle the milling machine.
Dyson also failed to carry out a proper risk assessment for moving the machine as well as ensuring the work environment and work system was completely safe to carry out this action.
The court found that external specialist lifting contractors were required to move certain machinery. However, Dyson’s workshop support team usually responded to requests to move machinery within the prototyping department, and this included the movement of milling machines.
On the day that the incident took place, the supervisor of the workshop support team, Keith Cambridge, received an email requesting the milling machine be moved. Although he claimed he wanted to use a forklift truck for the movement of the machine, it was discovered that use of the forklift truck would have to be requested 72 hours before the movement was due to take place, along with a complete written risk assessment.
Cambridge was said to have had “no training in completing risk assessments of this nature”. Due to time constraints, Cambridge and Miles sought a different method of moving the milling machine as there was no forklift available and the space where the milling machine resided was too small in any case, resulting in difficulty in the use of the forklift in that space.
The employees utilised two sets of three-tonne jacks, a five-tonne jack, one steering skate, two roller skates and wooden blocks.
Neither Cambridge nor Miles had been trained in the process of machine movement, and no risk assessment, method statement or lifting plan by a competently trained person had been completed.
In the moment the machine fell over and hit Miles, both Cambridge and Miles were using the five-tonne jack to lift the 1.5 tonne machine, then using the wooden blocks to replace the fixed roller skates.
Miles injured his rib and shoulders and head. The court concluded that, had the machine completely toppled over Miles, crushing him, he would have most likely died or have had significant life-threatening injuries.
Dyson Technologies pleaded guilty to breaching section 2(1) of the Health and Safety at Work etc. Act 1974.
In court, Dyson Technologies claimed it had put in place policies at the company to reduce risk. However, these policies were not followed and implemented at the local level.
Dyson argued the company policy when the incident occurred was that the moving of the milling machine had to be carried out using the forklift, following a complete risk assessment. The alternative option was to bring in external contractors specialised in machinery lifting to complete the job.
When pressed, Dyson then accepted in court that in truth, “there was no such policy in existence at the time”. The policy has since been implemented at the company. Dyson also accepted there was no specific policy at the time indicating employees were not to use the jacks and skates and other equipment for machine handling. Moreover, this equipment was readily made available to employees “to move heavy equipment without the requirement for risk assessments, training or supervision”.
Judge Joanna Dickens said the tech firm “fell far short of the appropriate standard” and the incident “could have caused death or very serious injury”.
It was therefore concluded the offence was high culpability and fell within harm category 2, but the Judge moved the case up to harm category 1, where the starting point of a company’s turnover is £2.4 million increasing to £6 million.
Dyson’s excellent safety record was considered by the judge when assessing the offence, as well as its full cooperation with the HSE’s investigation, and its early guilty plea.
The company was ordered to pay a fine of £1.2 million and £11,511 in costs.
Ben Compton QC, who represented Dyson Technologies, argued the tech firm had taken “immediate steps to resolve the situation after the incident”. He also brought up its introduction of a new training programme and a new risk assessment system.
HSE inspector, James Hole, said:
“Those in control of work have a duty to assess the risks, devise safe methods of working and to provide the necessary information, instruction and training to their workforce.”
You may also be interested in
RELATED CONTENT
RELATED COURSES
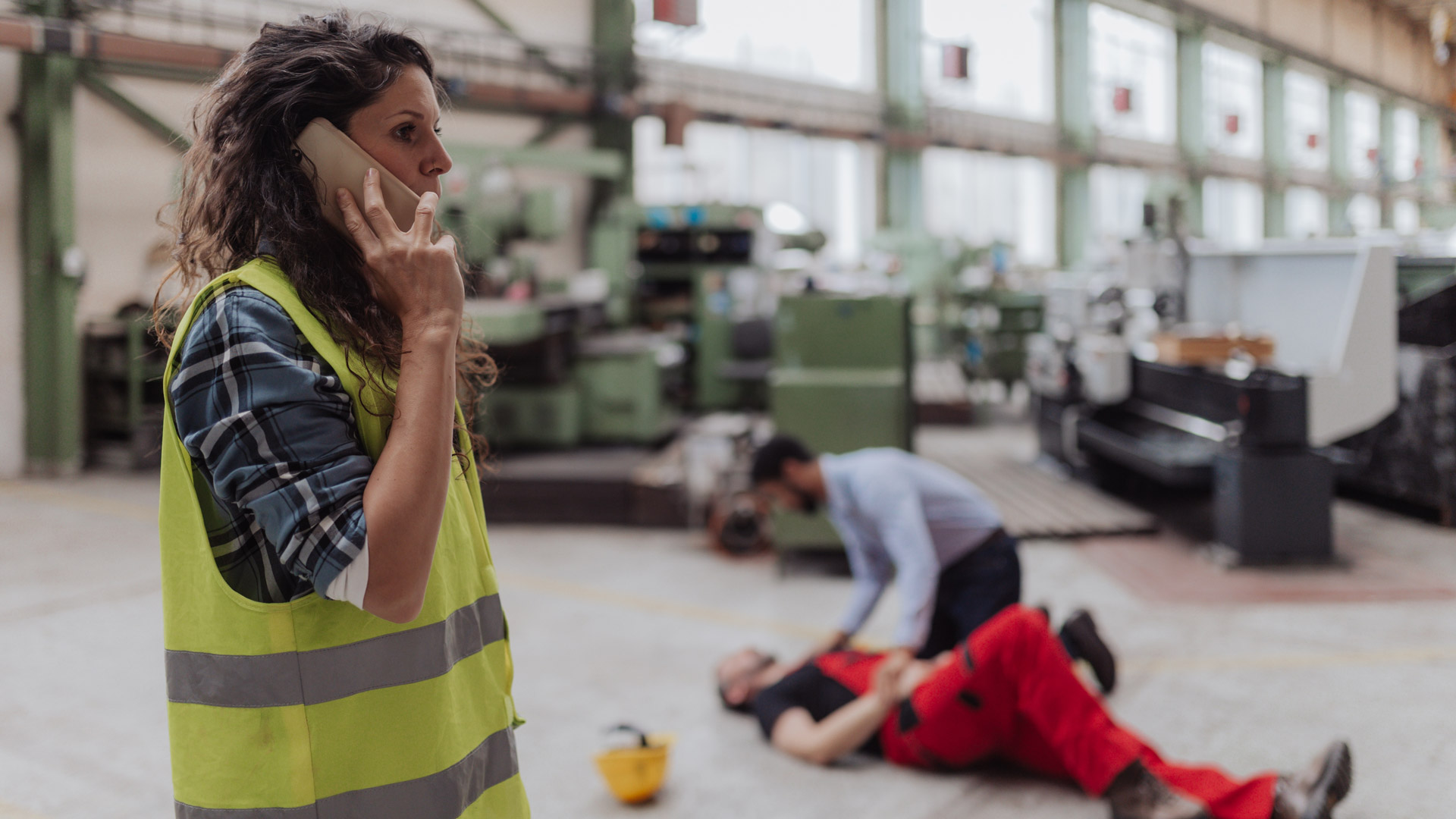
The Emergency first aid course offers learners the skills and knowledge to deal with emergency first aid situations at work.
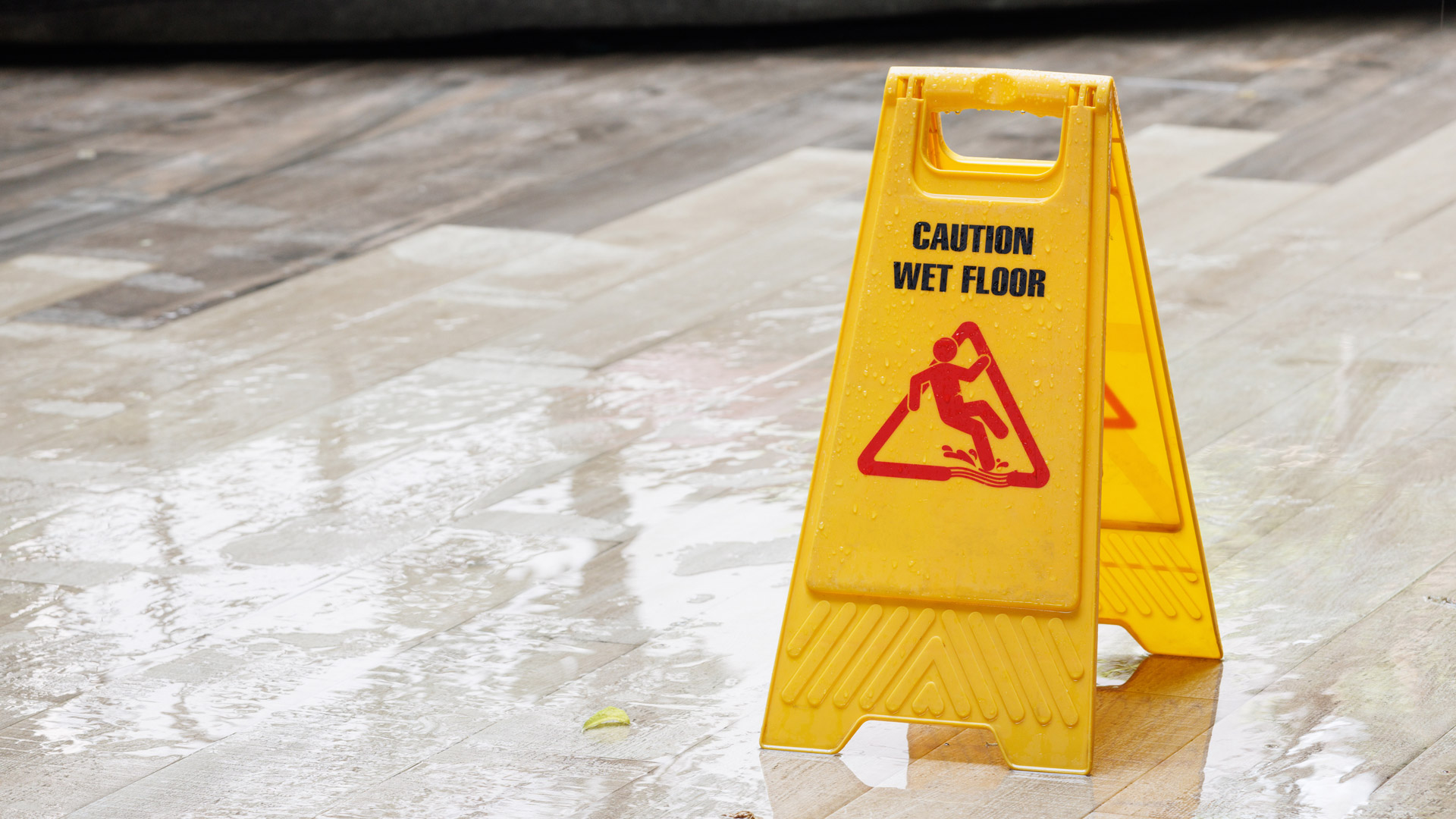
The Slips, trips and falls course explains the measures that can be implemented to prevent slips, trips and falls in the workplace.
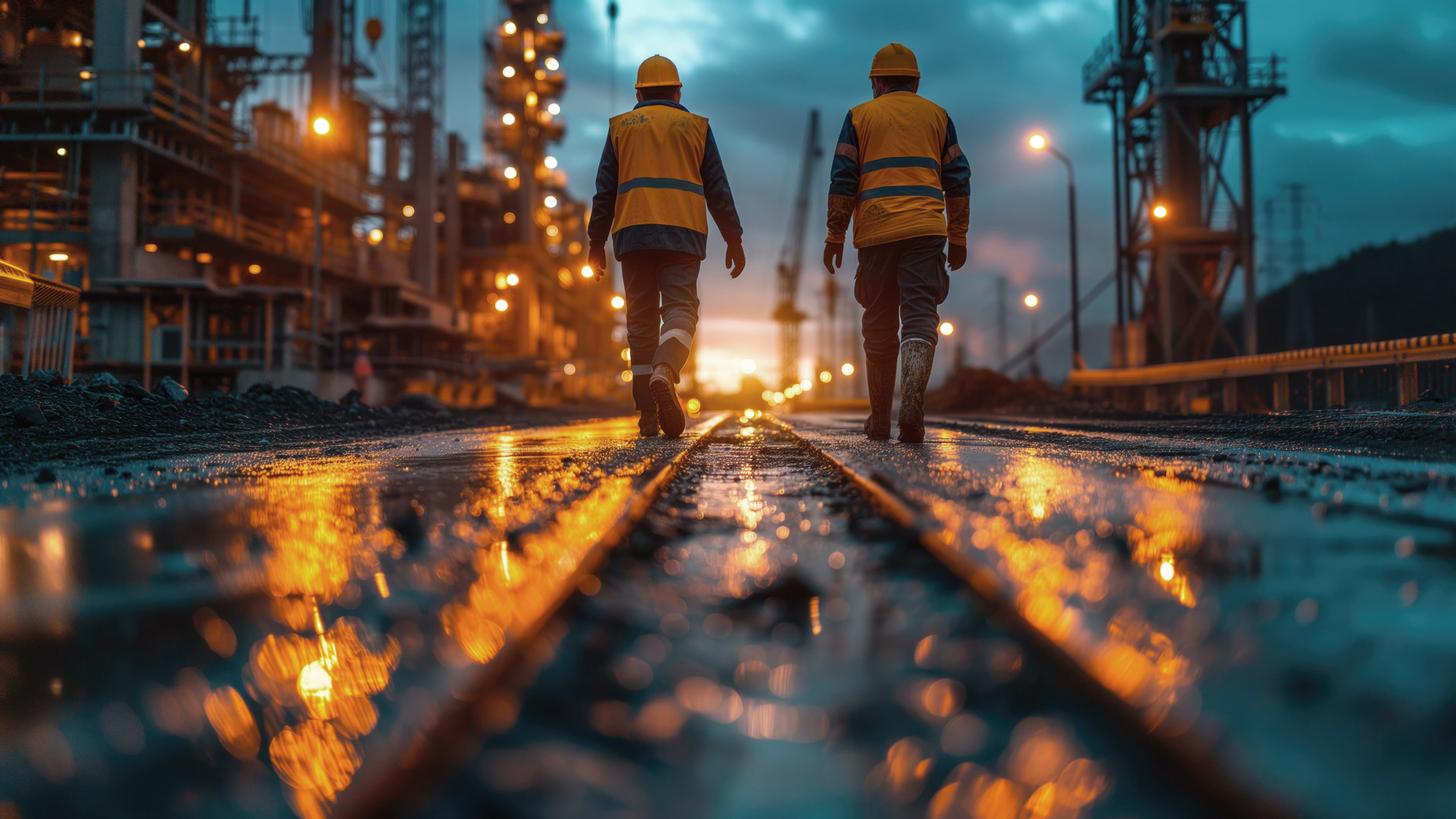
Introduction to health and safety gives learners a basic introduction to managing safety in their workplace.
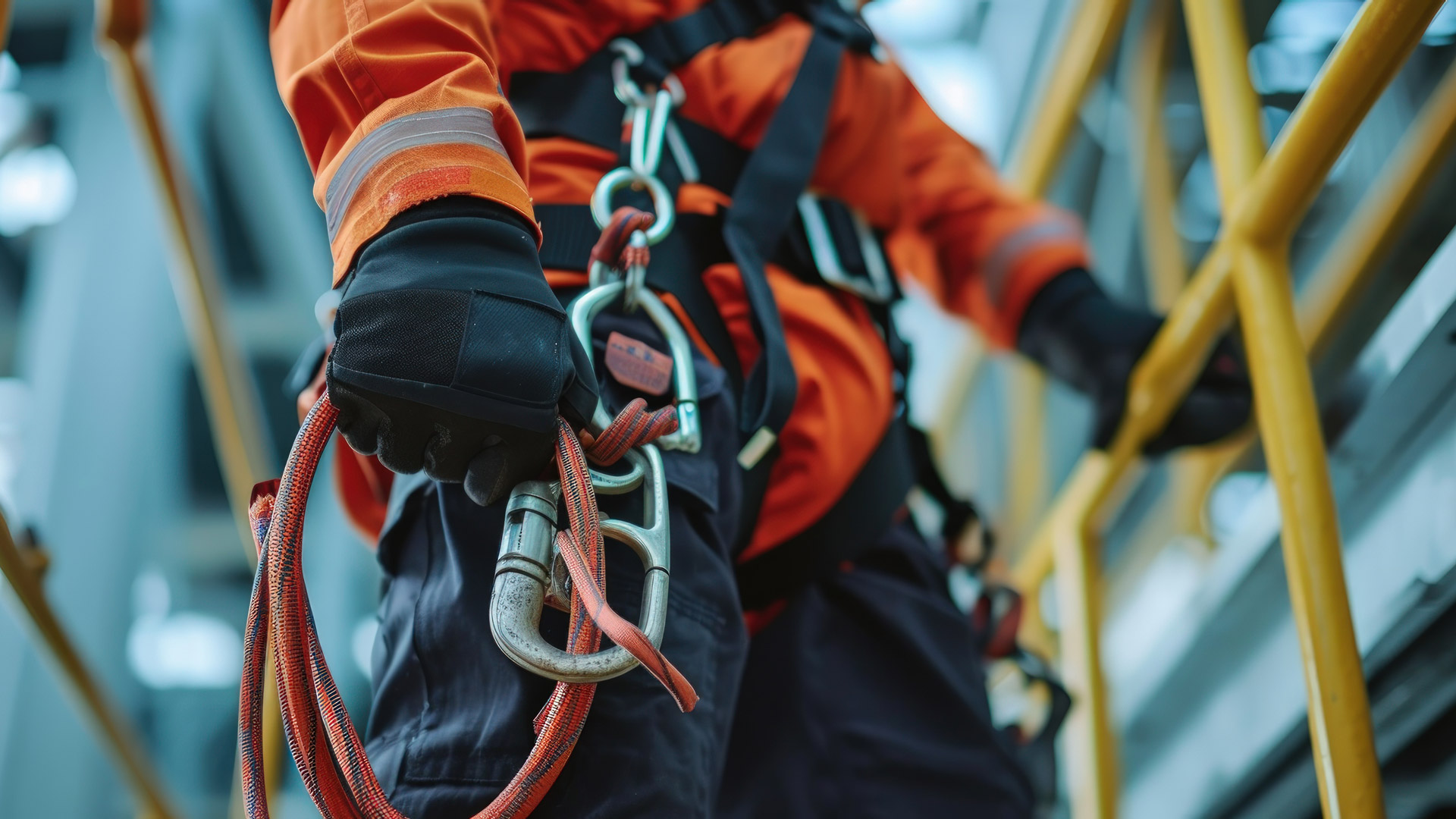
The Working at height course helps learners understand the dangers associated with working at height and ways to control the risks
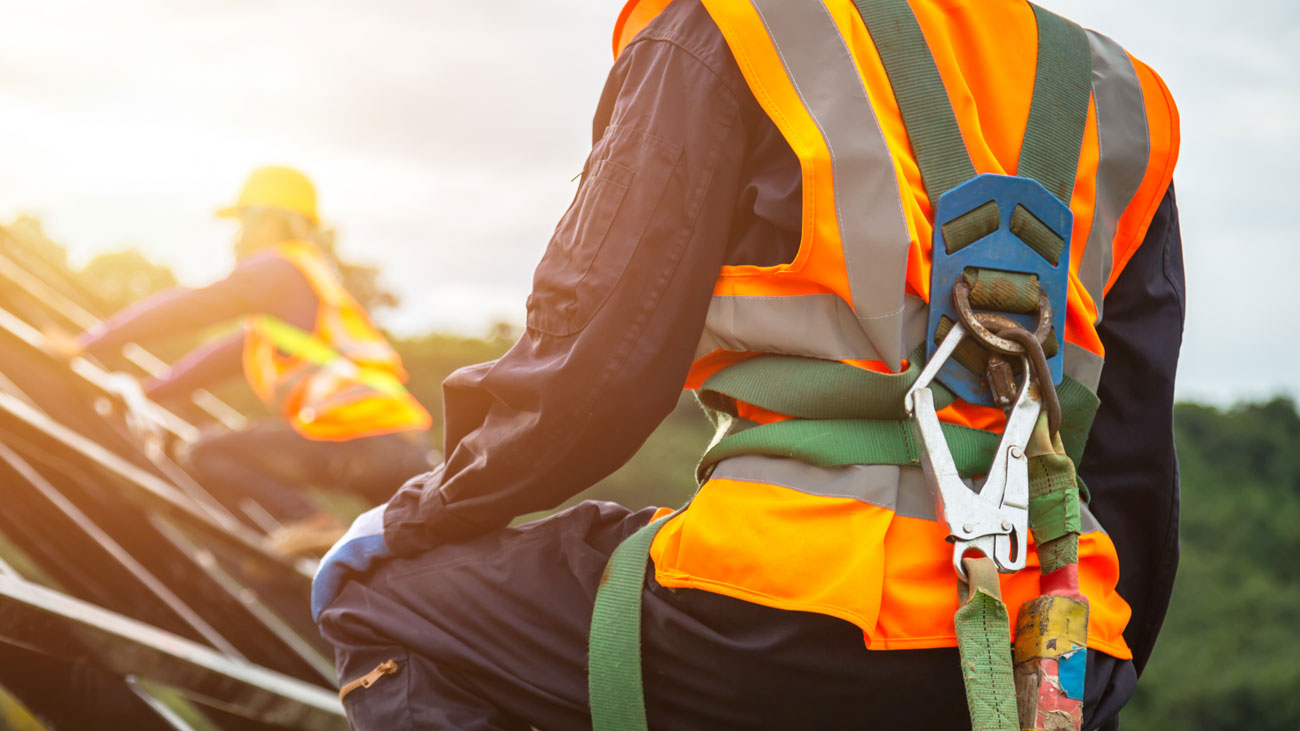
The Access Industry Forum (AIF), the forum that represents the principal work at height trade associations and federations, is calling for clearer rep...
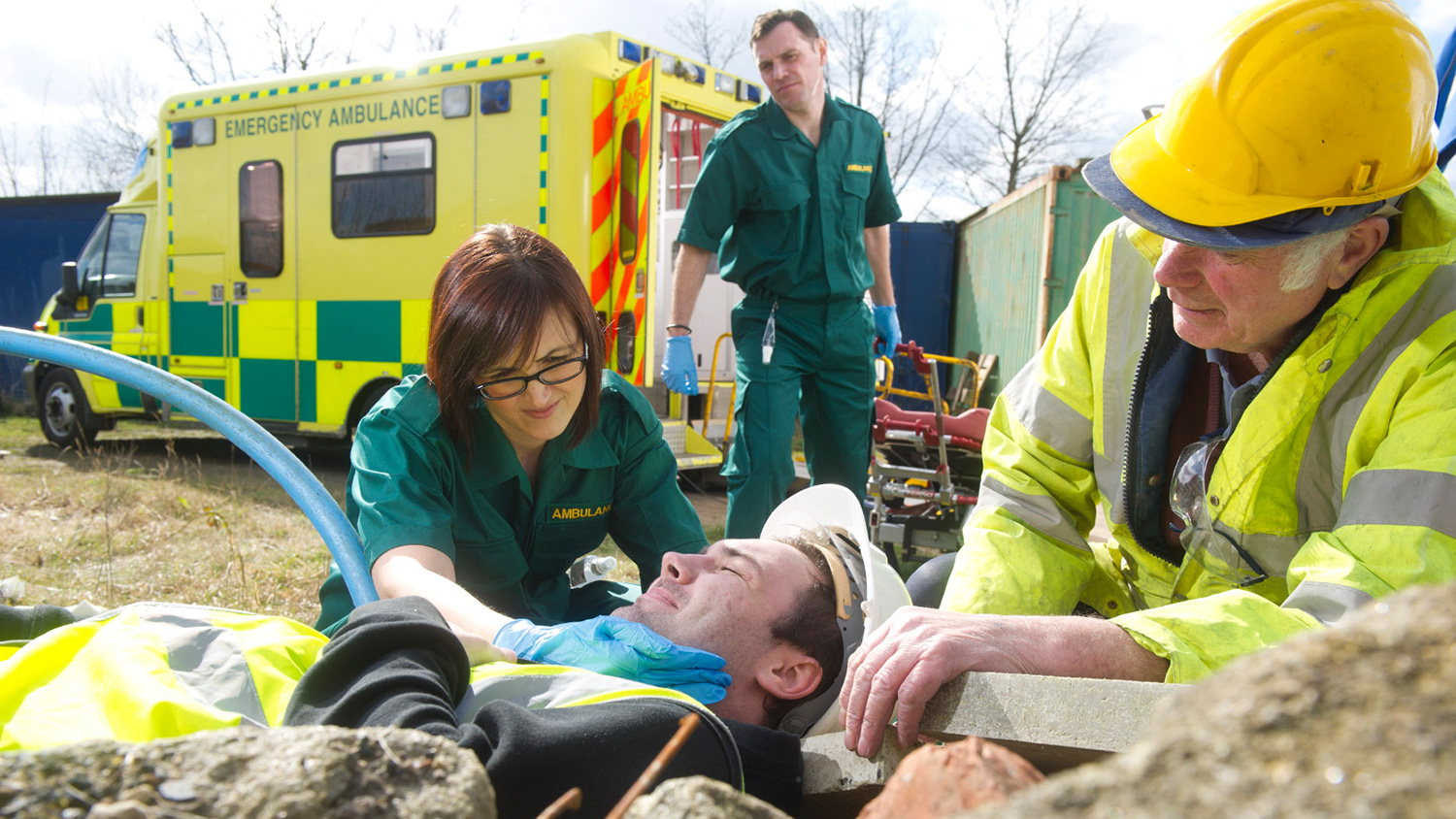
New IOSH President Stuart Hughes is calling on the profession to challenge itself to develop new ways of tackling the “unacceptably high” number of wo...
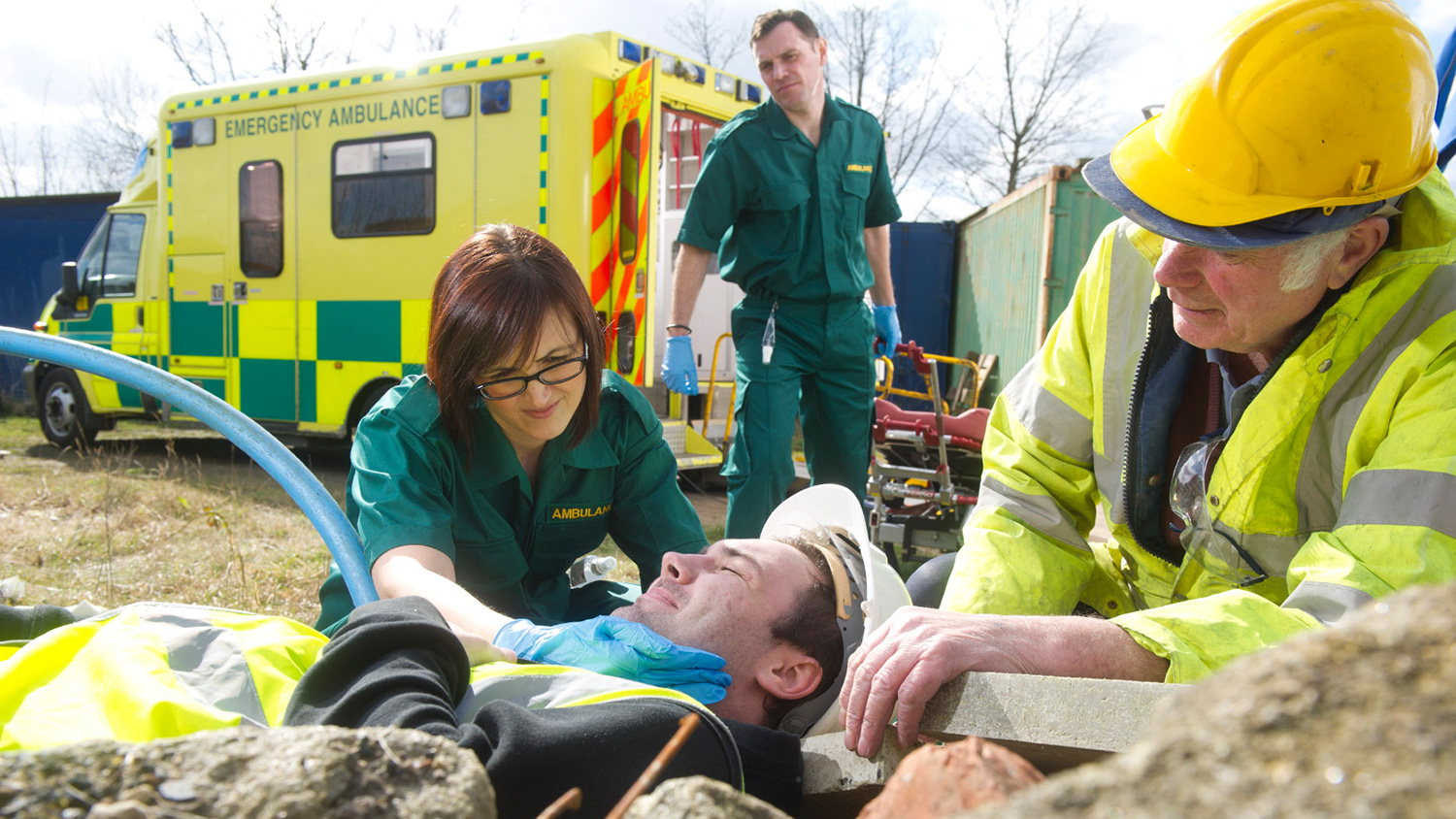
You may not realise it but there’s no legal duty on an employer to carry out an investigation into an incident in the workplace. But, says law firm rr...
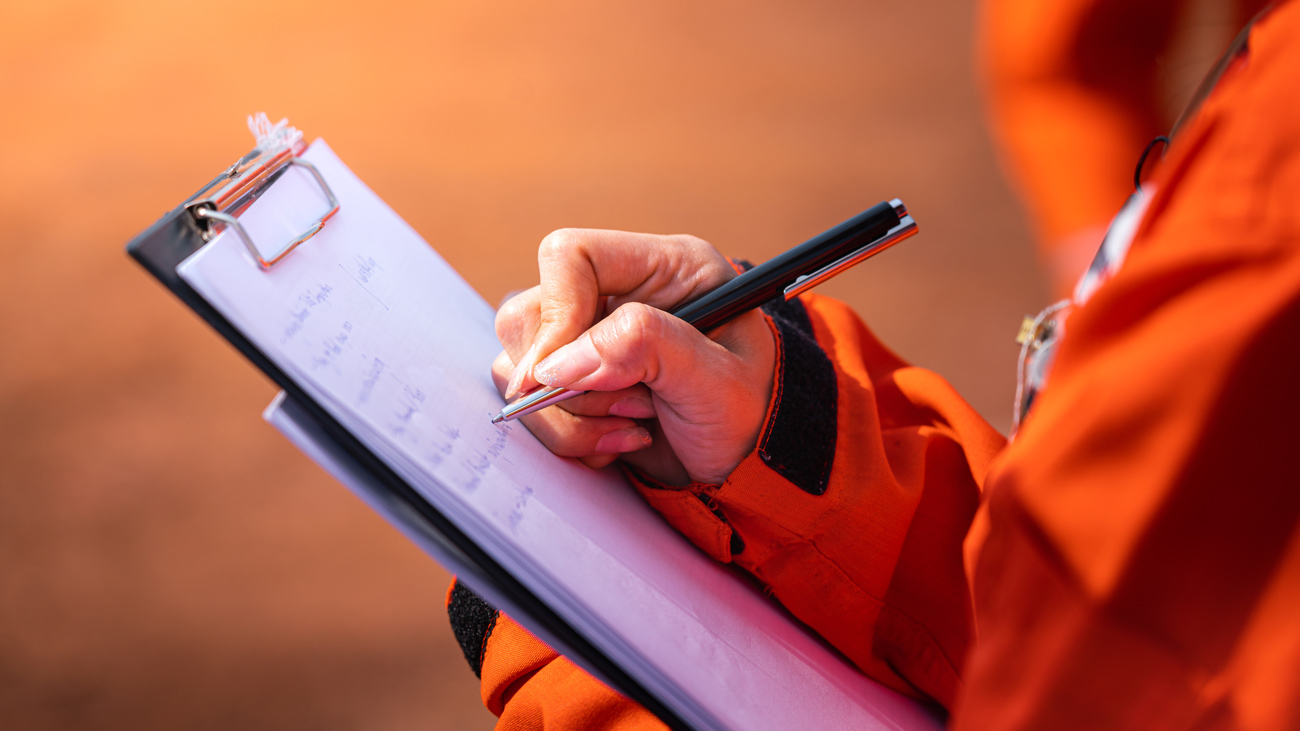
Employers are increasingly likely to go unpunished after workplace accidents it seems, as research by Prospect Union reveals the number of investigati...