What we’re breathing in is has become a very real concern in 2020 as we don masks to prevent the transmission of the coronavirus. However, recent research reveals that there are other air pollutants that too many workers are still being exposed to.
A new whitepaper by Global Action Plan and Zehnder Clean Air Solutions has found that the quality of the air in the manufacturing sector continues to be underplayed and not acted upon, with workers in the UK still being exposed to unhealthy levels of airborne hazards and pollution. The whitepaper further presents a renewed case for tackling air pollution in industry workplaces with urgent actions for policy-makers, regulators and manufacturers.
The whitepaper – With Every Breath We Make: Ensuring Healthy Air for Manufacturing Workers – identifies:
- An estimated 440,000 workers with health conditions that are exacerbated by air pollution are still being exposed to unhealthy levels of airborne hazards and pollution in manufacturing workplaces.
- The presence of airborne hazards causes production issues, which impacts profit margins.
- Current regulation allows levels of airborne hazards and pollution that are dangerous to manufacturing workers’ health.
- Regulation enforcement is not meeting the necessary standards.
Global Action Plan believes urgent action is required to protect workers who are unable to work remotely, given that increasing evidence shows that poor air quality worsens underlying health conditions, which make a person more vulnerable to complications if they contract COVID-19, and workers in the manufacturing sector are at greater risk of being exposed to dust, toxic particles and pollution.
The most urgent action from the whitepaper, which is supported by the Trade Unions Clean Air Network (TUCAN), the Hazards campaign and Chartered Institute of Environmental Health (CIEH), is to call on the government to update regulation to lower the acceptable limits for air pollutants in the industrial workplace, echoing the call from the Institute of Occupational Medicine (IOM) and Trades Union Congress (TUC) that limits be changed to 1mg/m3 for respirable dust from the current 4mg/m3 COSHH trigger.
Chris Large, Co-CEO at Global Action Plan, says:
“Manufacturers are increasingly paying attention to employee wellbeing, especially as workplaces look to become COVID-secure, but the quality of the air and the working environment continues to be underplayed as a foundation of good employee wellbeing. Regulators must enforce lower limits to protect the hidden heroes who have continued to work throughout the pandemic, especially given ongoing research increasingly links poor air quality to the worsening of COVID-19 symptoms. Current regulation continues to allow unacceptable levels of airborne hazards and pollution that are dangerous to manufacturing workers’ health.”
As an employer, you can manage exposure to hazards, but you must first be aware of them, and how they pose a risk. You then need to implement control measures so that they are less likely to cause harm.
To help decide what safety precautions should be considered, there is a simple process known as the hierarchy of risk control:
- Eliminate the hazard
- Reduce the hazard
- Preventing people coming into contact with the hazard
- Safe systems of work
- Personal protective equipment
Controls at the top of the hierarchy are the preferred options and are often referred to as Safe Place Controls because they are less reliant on people doing something and they generally can protect more people. Safe systems of work and PPE are often referred to as Safe Person Controls.
In addition to these systems, there may also be times when you need to limit a person’s exposure to a particular hazard (chemicals, noise and dust etc.). The longer their exposure, the greater the likelihood of developing health problems. This could be achieved by having several people working for short periods rather than one person working for several hours; however, it relies very much on each individual sticking to a specific time allocation.
You may also be interested in
RELATED CONTENT
RELATED COURSES
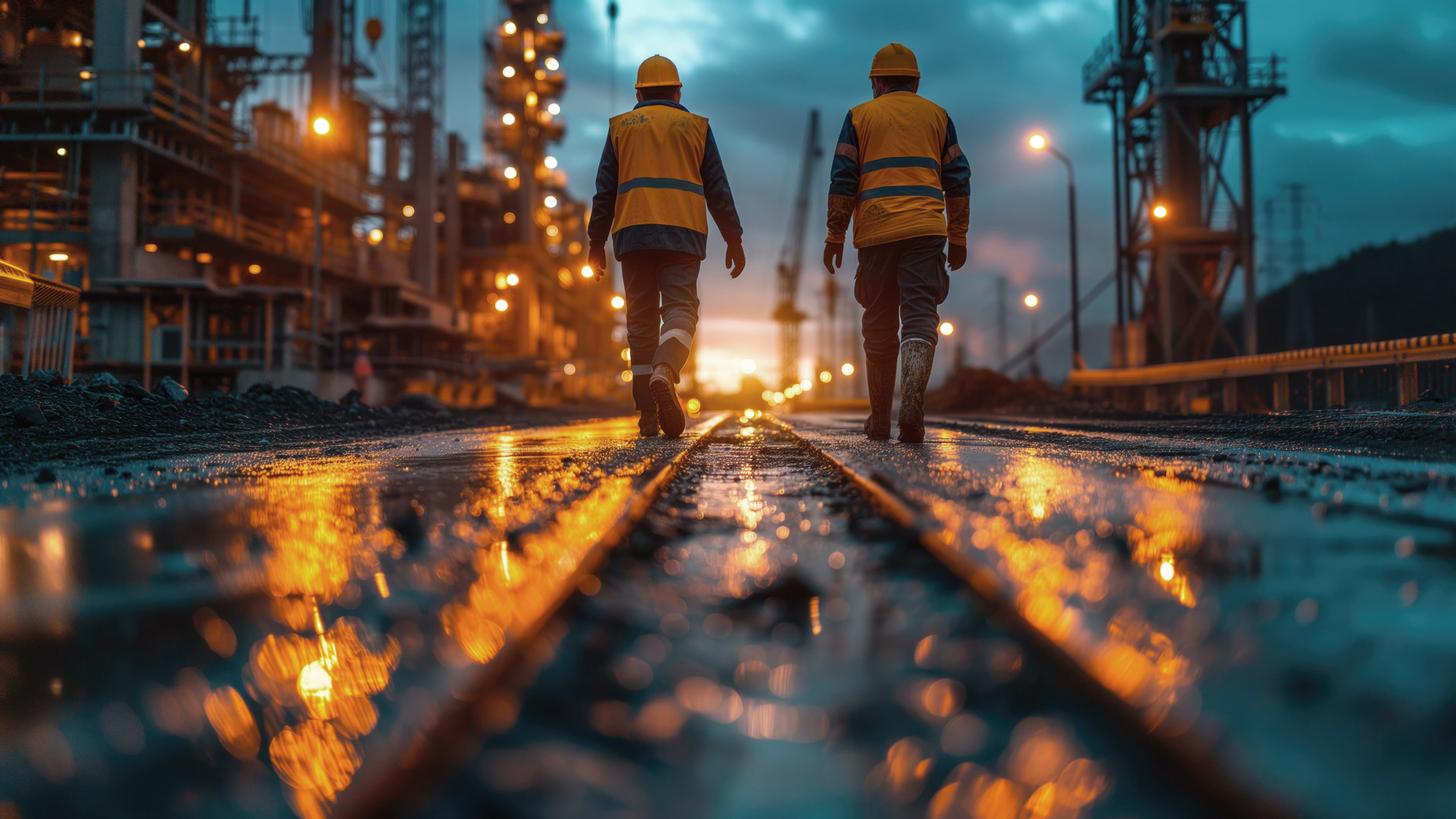
Introduction to health and safety gives learners a basic introduction to managing safety in their workplace.
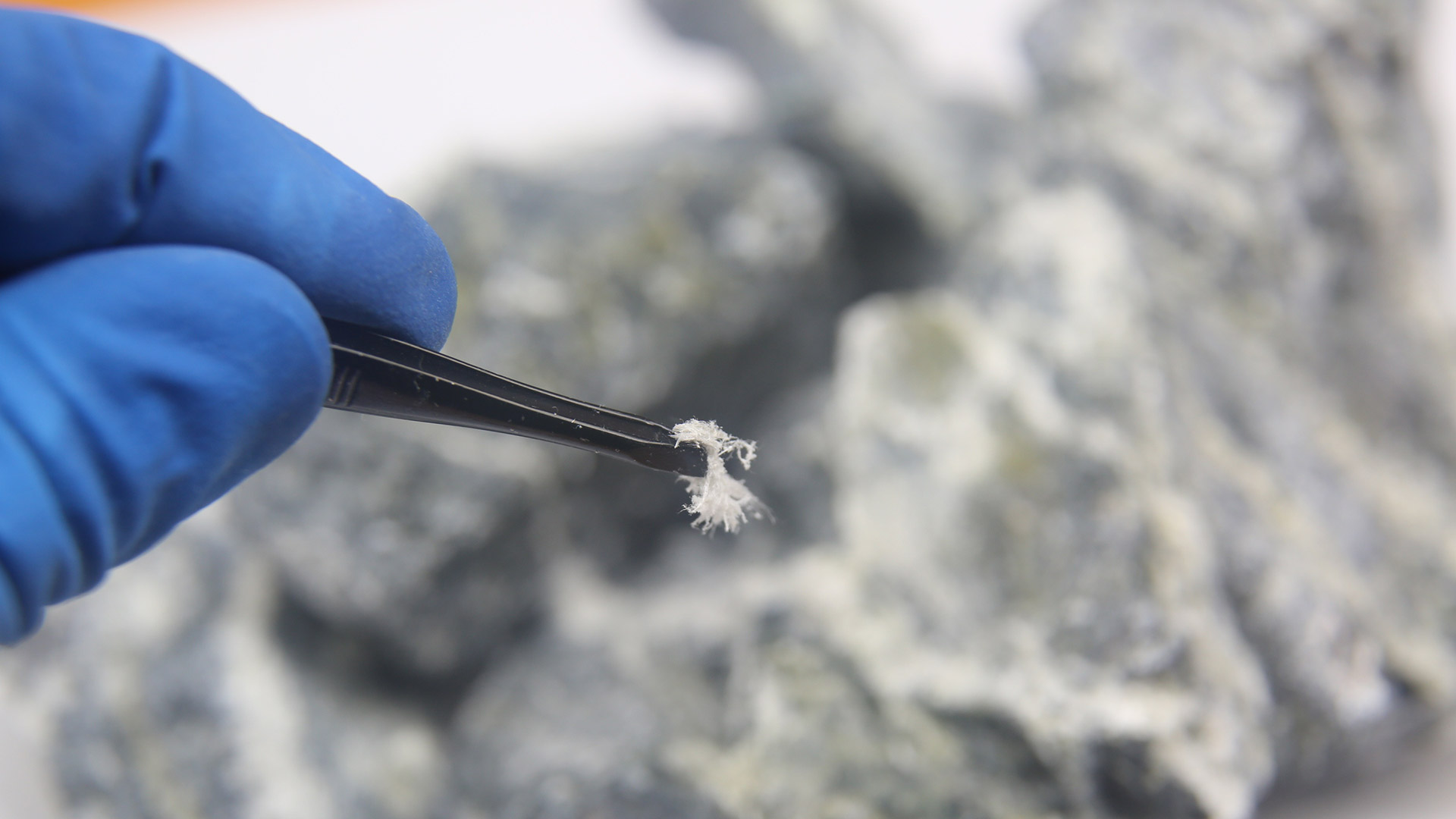
The asbestos course looks at how to manage asbestos in the workplace and recognise the risks.
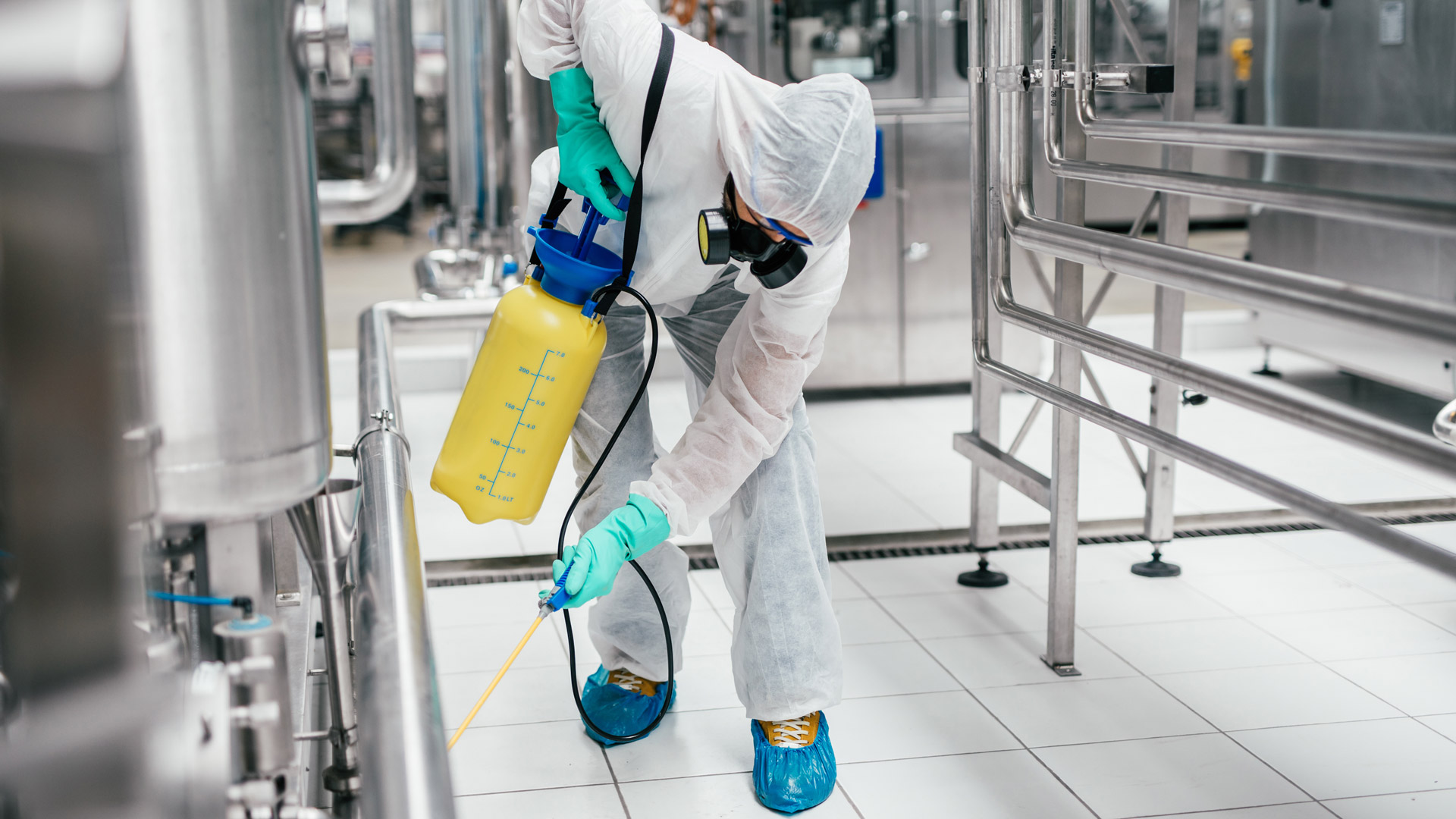
The Control of Substances Hazardous to Health (COSHH) course helps learners carry out work involving hazardous substances safely.
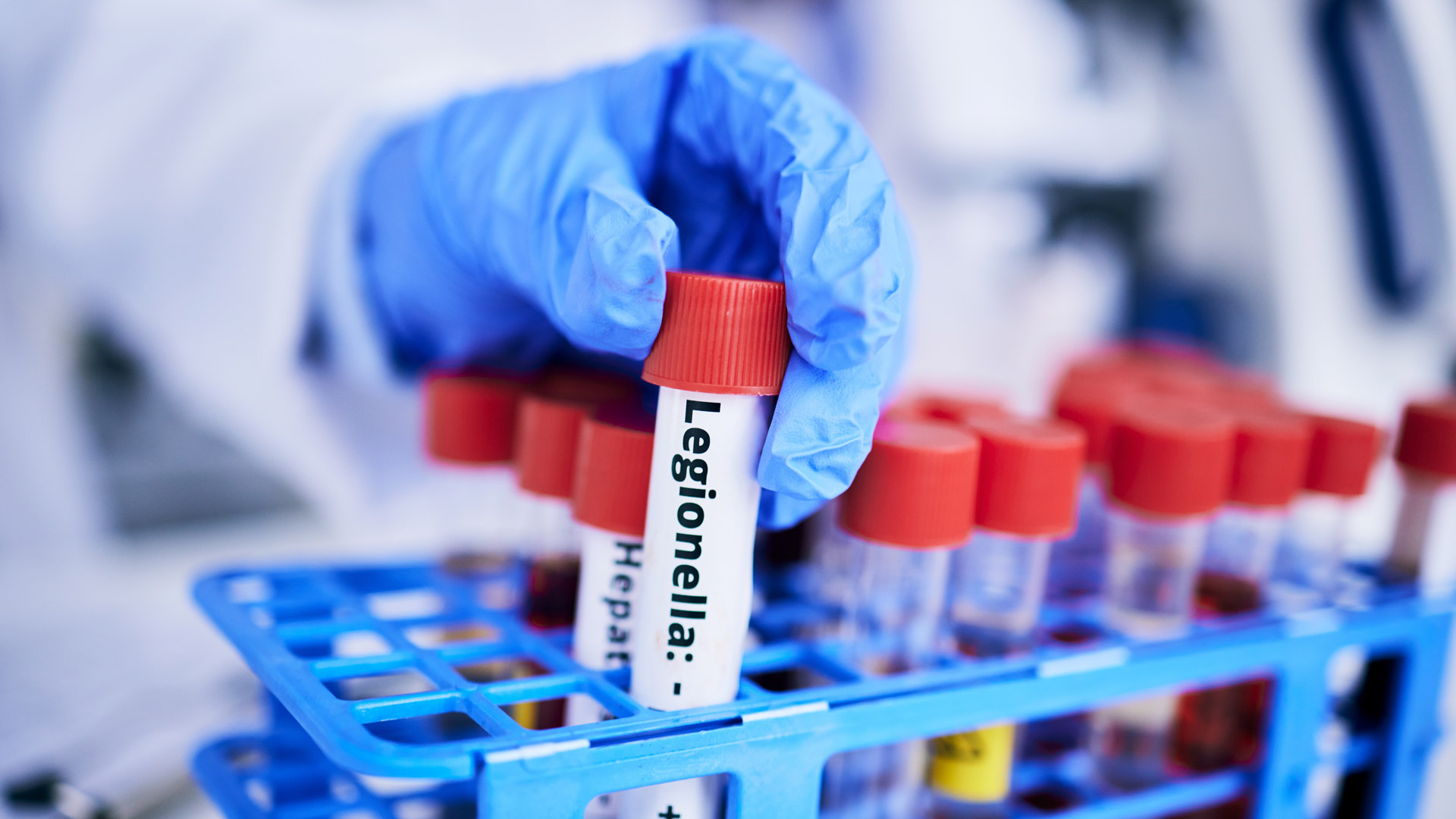
The Legionella course ensures people understand the risk of legionella and are aware of the requirements of the L8 ACoP.
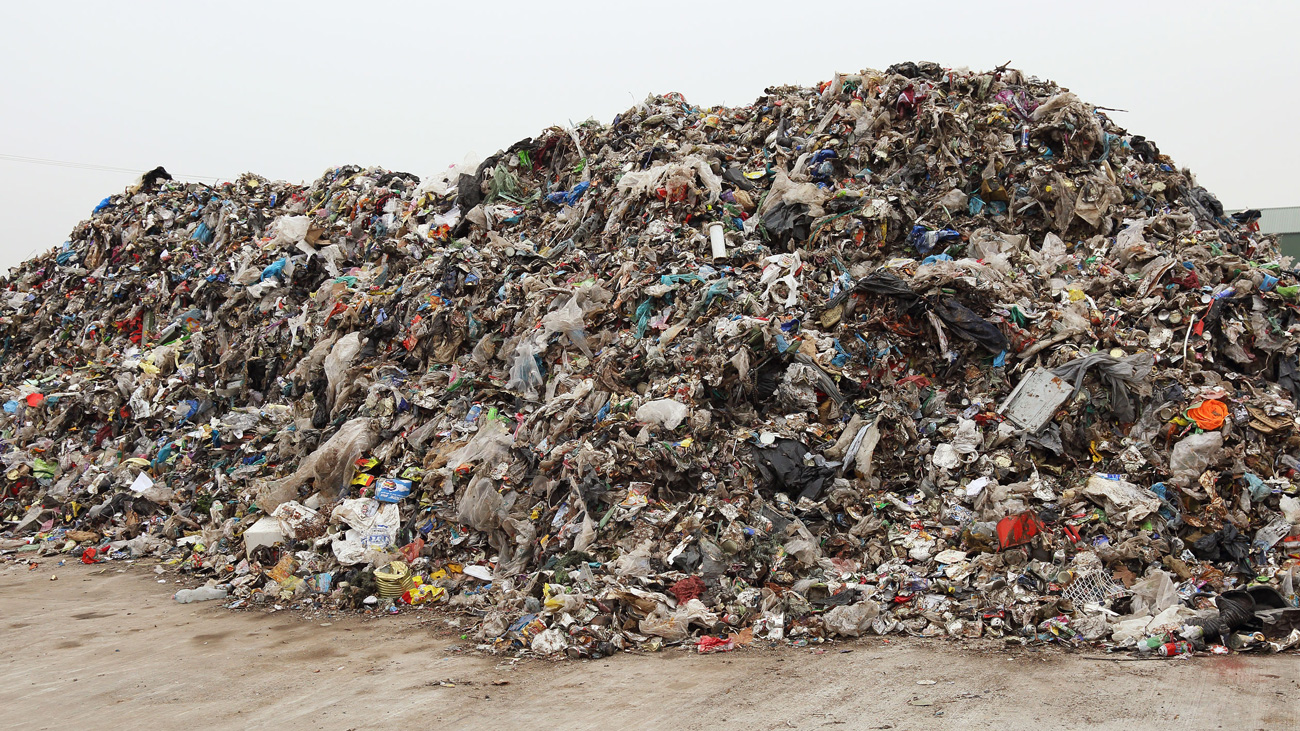
A survey of nearly 1,700 people across the recycling and waste management sector by the Environmental Services Association (ESA) has suggested the ind...
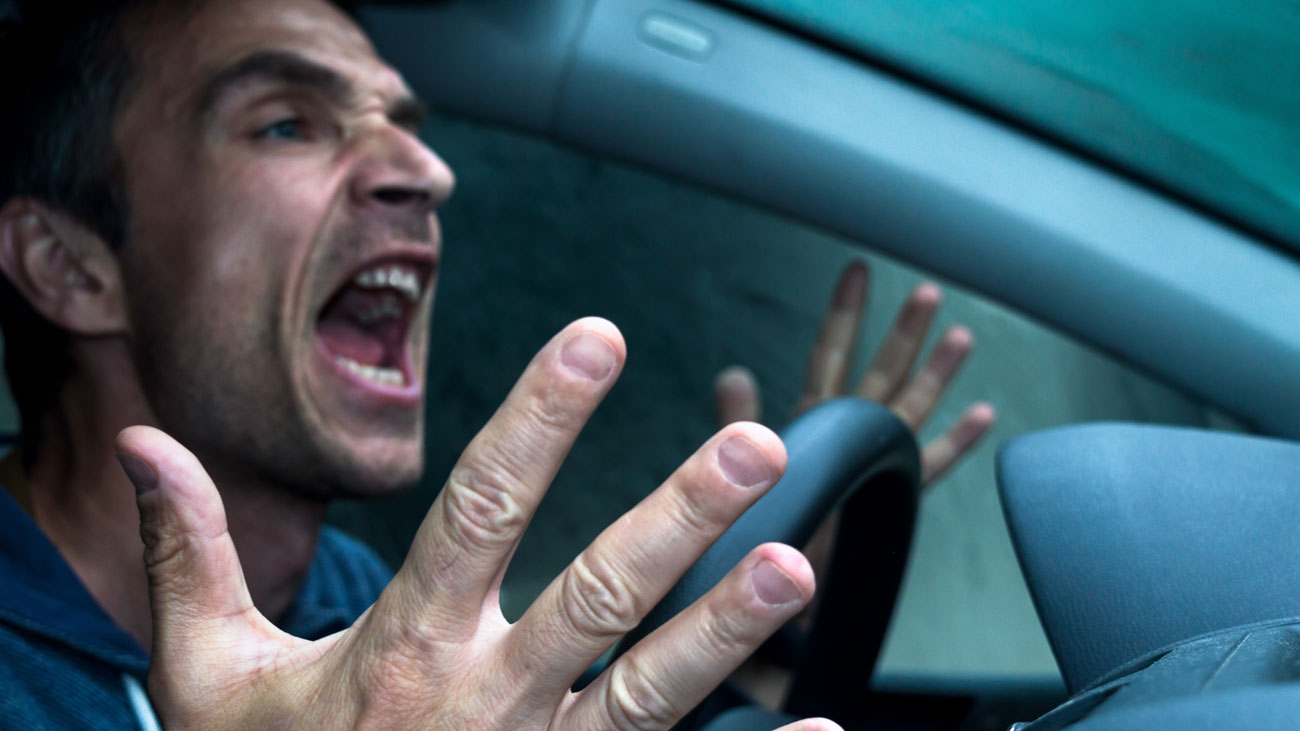
Friday is the most hazardous day of the week for fleet drivers with the highest number of accidents, speeding events, and incidences of aggressive dri...
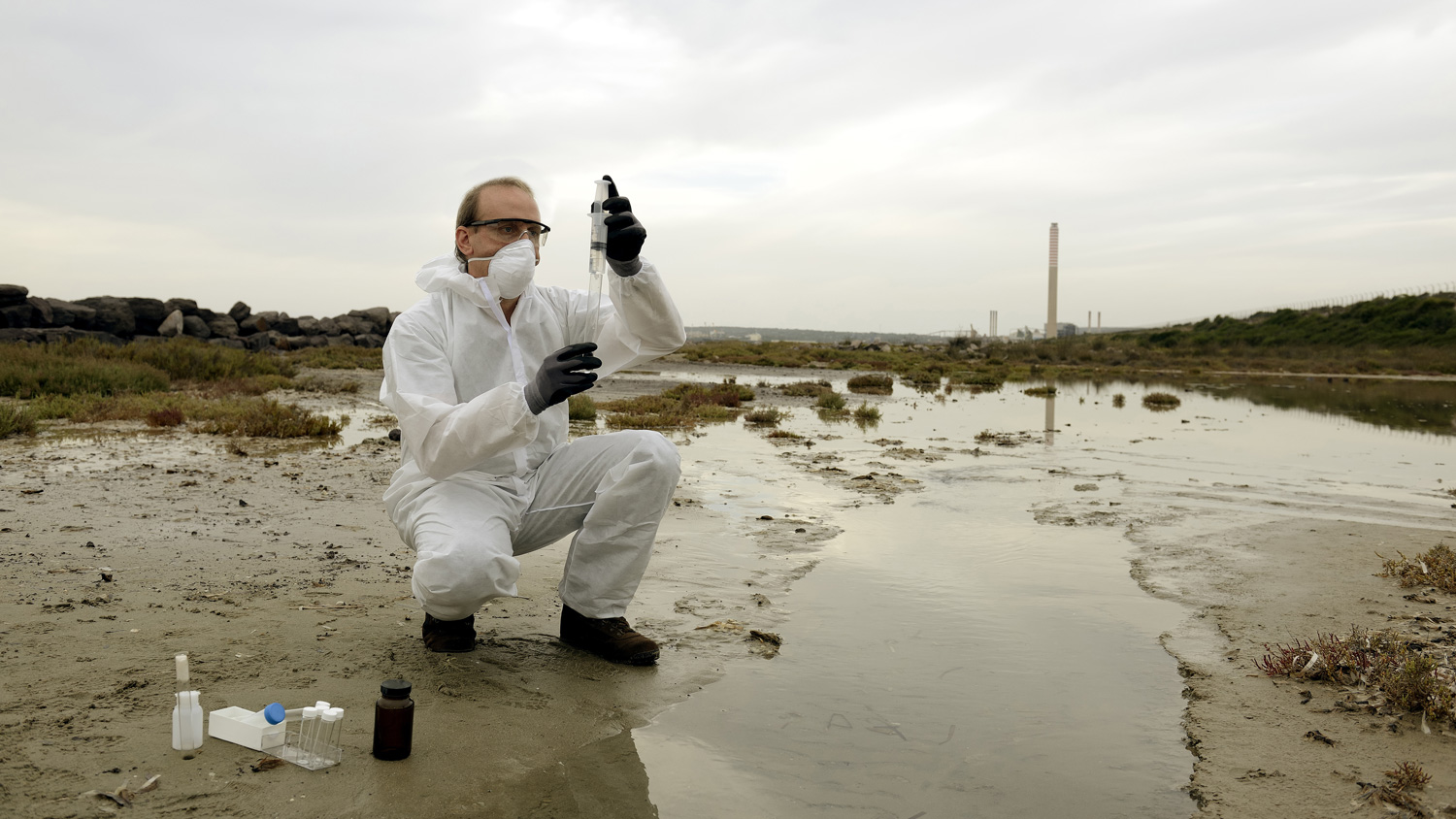
The UK government has announced it will not match new EU restrictions on various potentially hazardous chemicals, including the “rubber crumbs” used t...
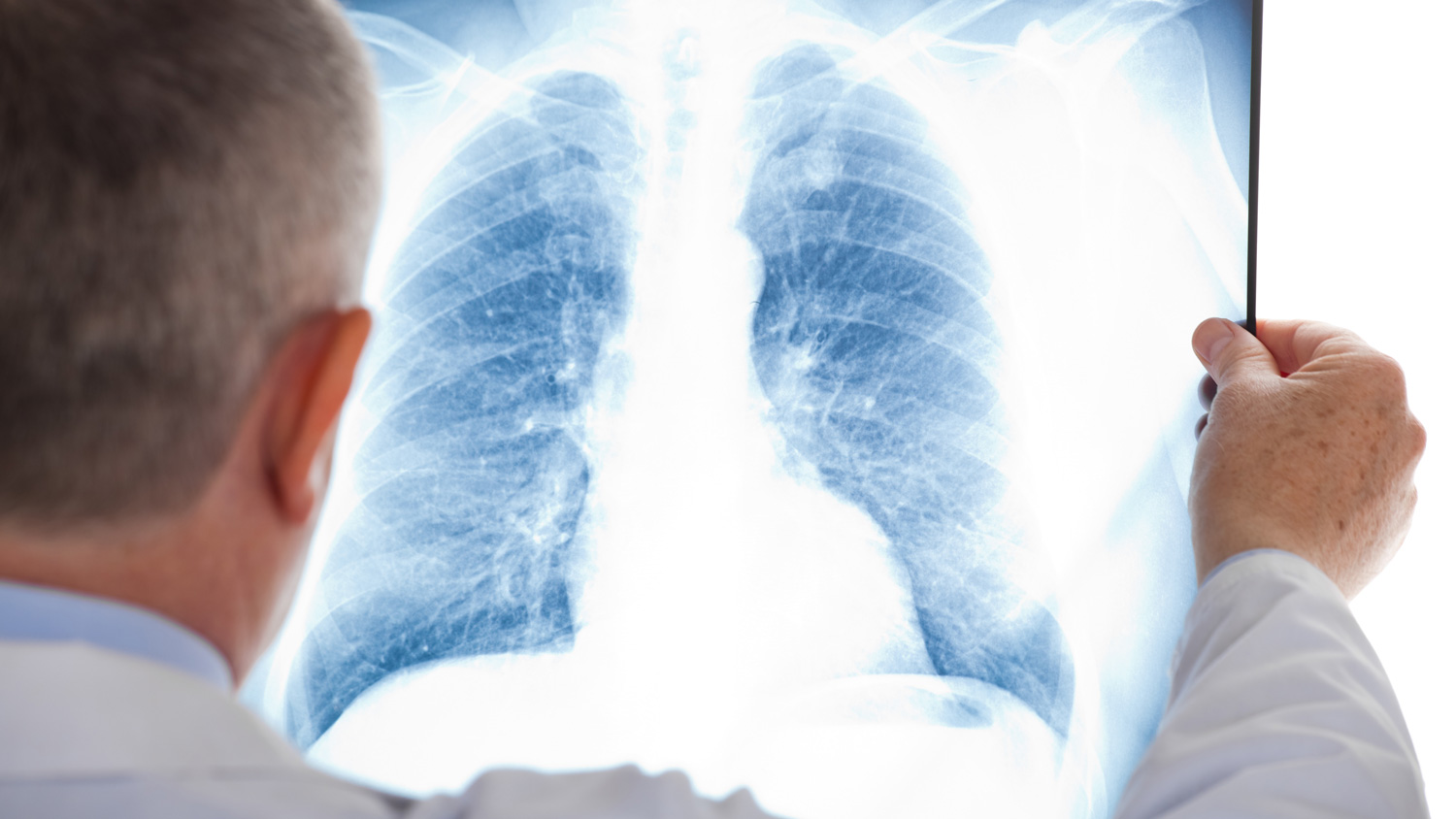
Global Asbestos Awareness Week 2023, organised by the Asbestos Disease Awareness Organisation, takes place this week (1-7 April), aiming to raise awar...