RISK
GUIDE
The hierarchy of risk control - a manager's guide
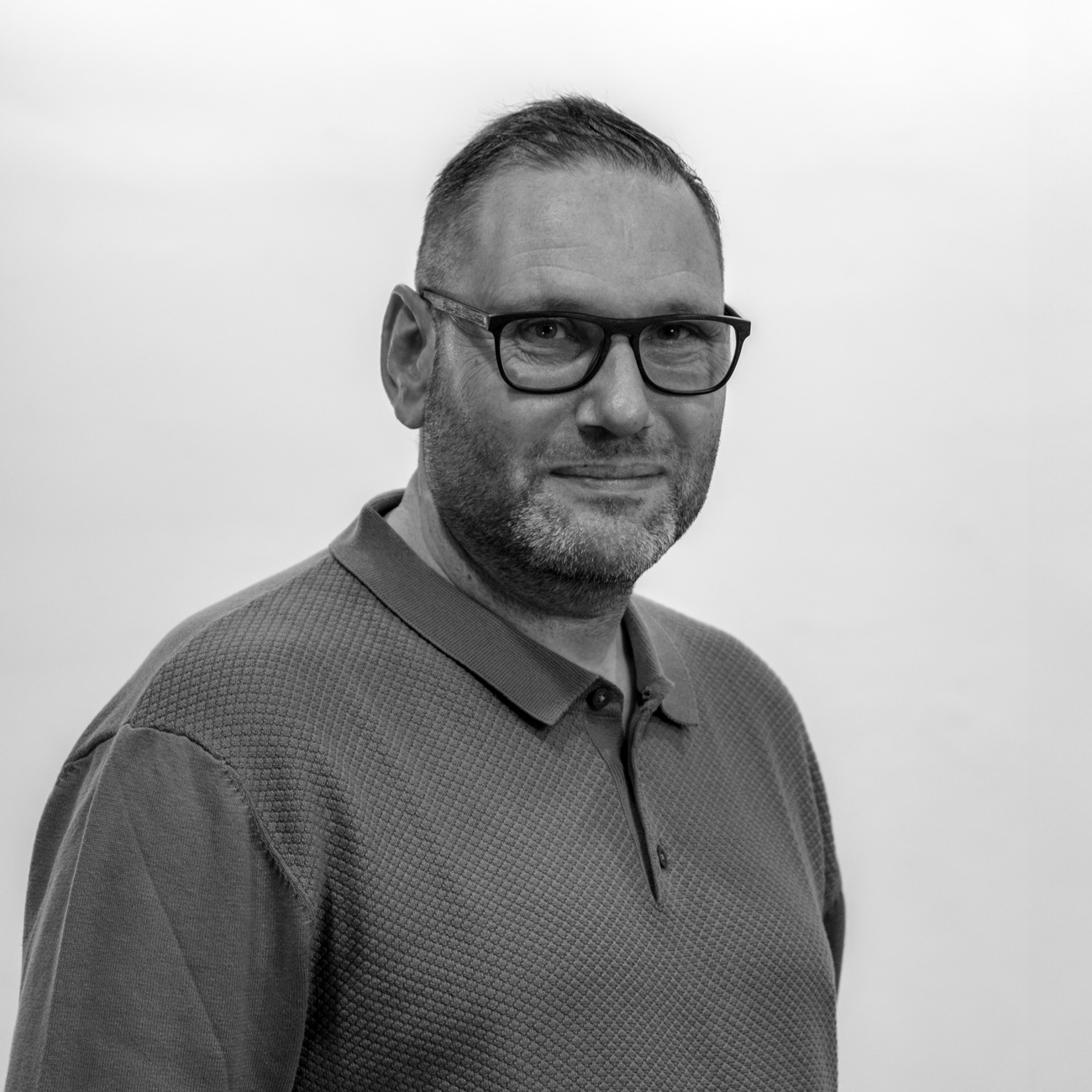
Published by Jamie Robinson,
1 Nov 2024
Introduction
Implementing control measures reduces the likelihood and consequences of injury or ill health in the workplace. But how do control measures help to reduce risk, and in what order should they be used?
To help decide what safety precautions should be considered, there is a simple process known as the hierarchy of risk control.
Controls at the top of the hierarchy are the preferred options and are often referred to as Safe Place Controls because they are less reliant on people doing something and they generally can protect more people.
Safe systems of work and PPE are often referred to as Safe Person Controls.
This guide looks at the control measures in the hierarchy and how they can be applied.
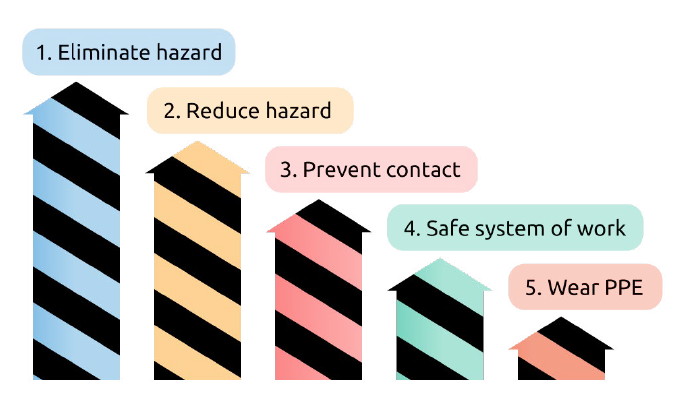
Control measures - safe place controls
Let's look first at the so-called 'safe place controls' that make up the first three levels of the hierarchy.
1. Eliminate the hazard
This is the most effective method of reducing hazards in the workplace. Employers should always consider whether the job needs to be done in the first place, thereby eliminating the hazard altogether.
Examples include not working at height if the job can be done from the ground, not using dangerous chemicals unless they are essential, keeping people out of areas where vehicles are manoeuvring, or not using a piece of machinery unless it’s necessary. Obviously, eliminating the hazard is not always possible.
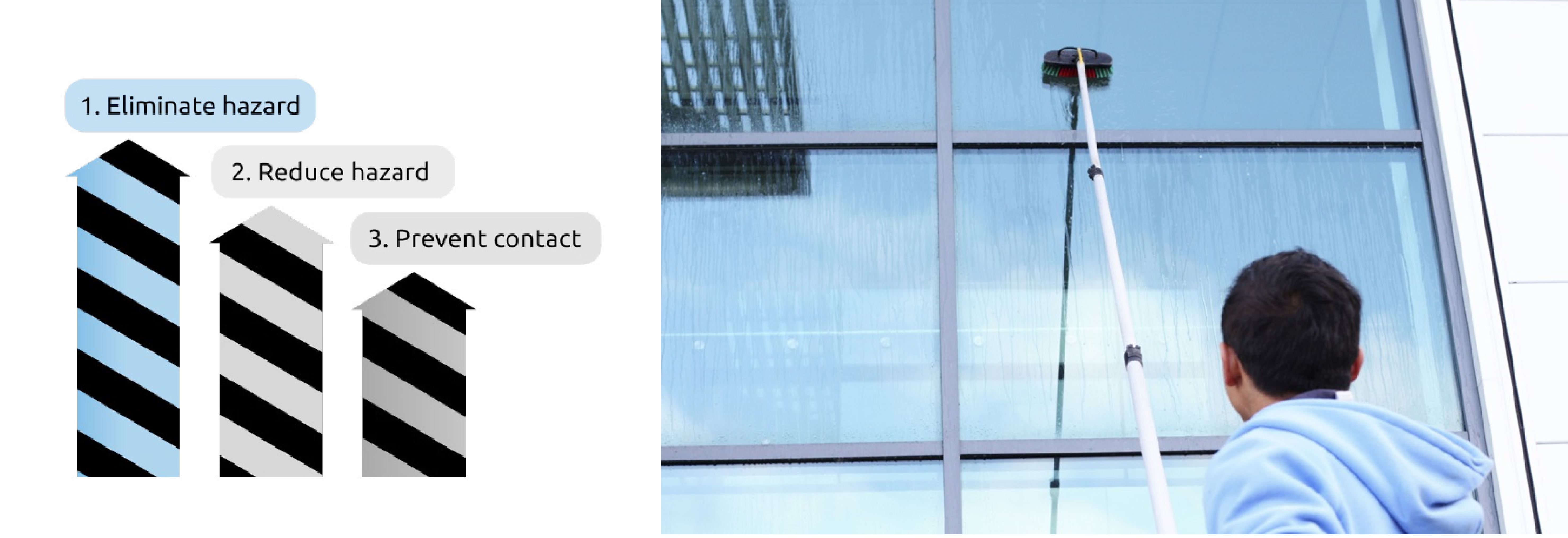
2. Reduce the hazard
A hazard can be reduced by substituting it with a less hazardous solution. In many cases it may be possible to substitute, reduce or replace the machine, material, activity or other feature that introduces the hazard, by an alternative method of work. This could include replacing a solvent-based paint with a water-based paint, or swapping from a petrol-driven lawn mower to an electric one. It could also include reducing the amount of time spent doing a certain activity.
Whenever substitution is considered, the effects of the new method of work must also be considered. For example, using a forklift truck may make carrying a heavy object easier, but the truck itself introduces new hazards and risks, which could potentially be more dangerous.
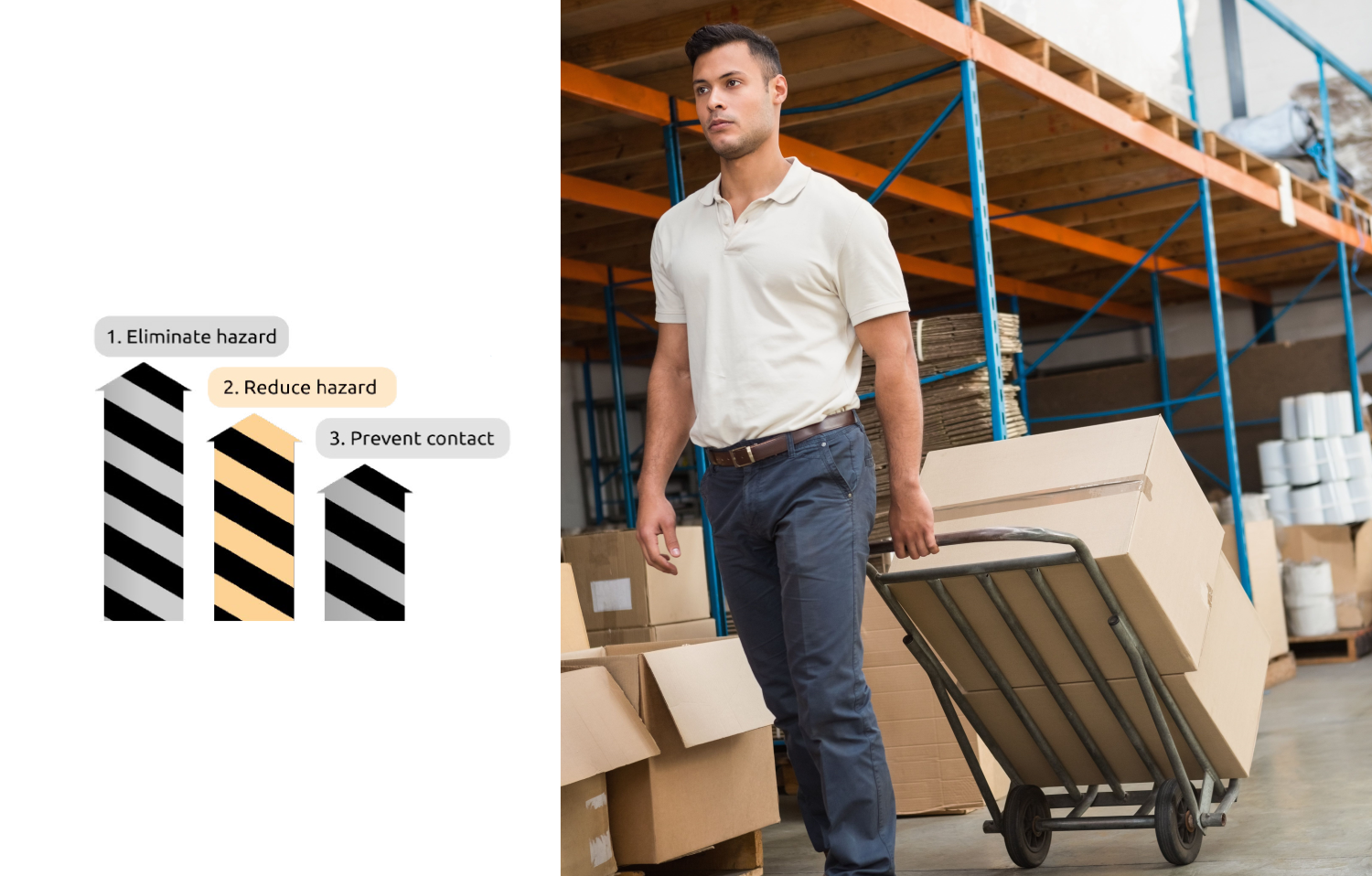
3. Preventing people coming into contact with the hazard
Preventing people coming into contact with a hazard can be done in one of two ways – putting distance between people and the hazard or enclosing the hazard.
In some cases, it may be possible to isolate the hazard from the employee (such as by providing fixed guarding to moving parts of a machine). In other cases, it may be possible to carry out the activity in a specific area, thereby enclosing the hazard and reducing exposure to fewer employees (for example, by providing a paint spray booth for the painting of cars or undertaking welding in a specially designed workshop).
It may also be possible for the hazard to be removed by some form of engineering control (such as providing local ventilation to remove hazardous fumes).
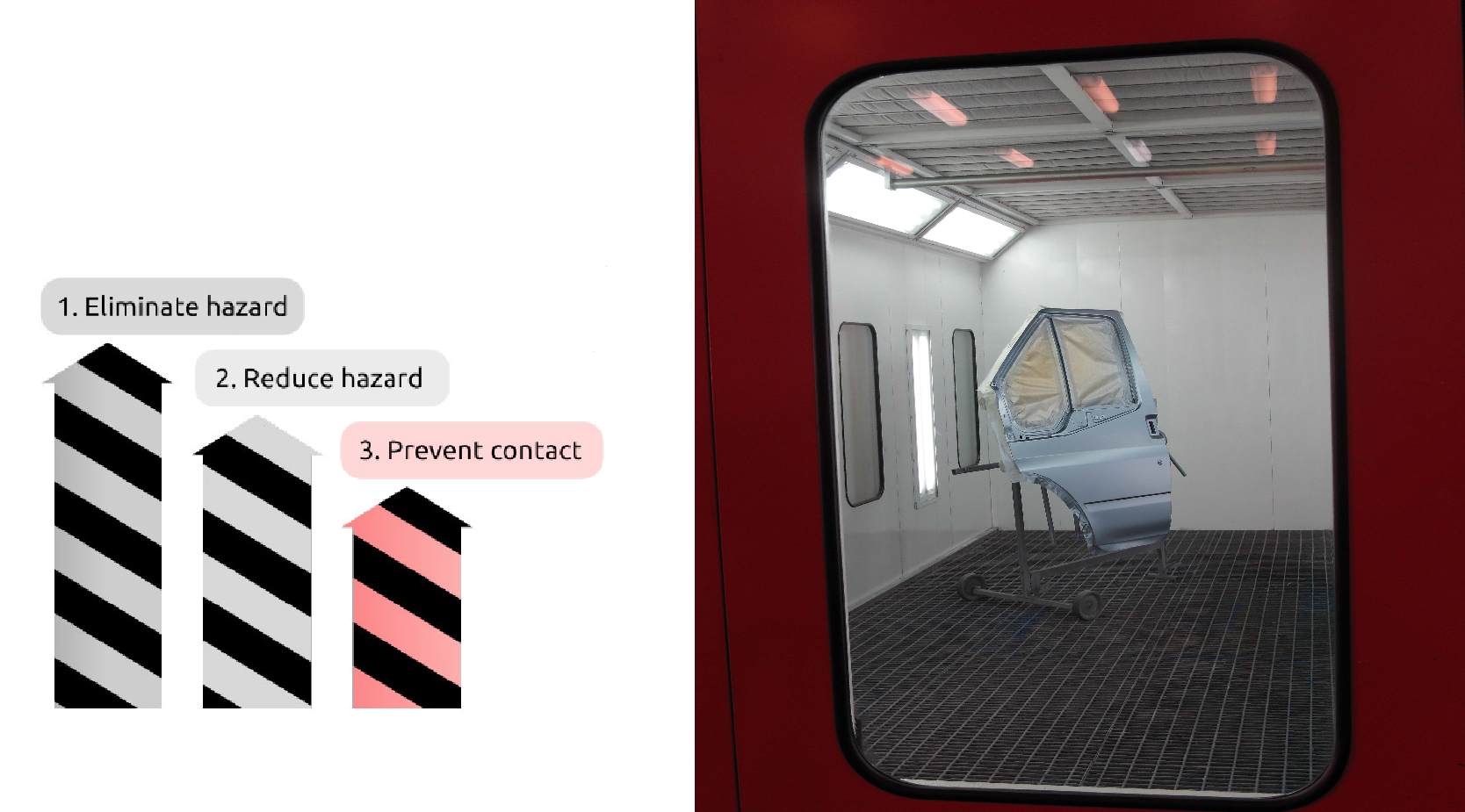
Control measures - safe person controls
Now let's looks at the so-called 'safe person controls' that make up the lower two levels of the hierarchy.
4. Safe systems of work
The introduction of safe systems of work will often make activities much safer. The extent of the safe system of work will depend on the nature of the activity and how dangerous the activity might be.
Permit-to-work systems are detailed formal written systems that are used for controlling works that are particularly hazardous, such as working with high voltage electricity or in confined spaces. The permit specifies the exact work that is to be carried out, along with the precautions that must be taken.
In addition to these systems, there may also be times when you need to limit a person’s exposure to a particular hazard (chemicals, noise and dust, etc.). The longer their exposure, the greater the likelihood of developing health problems. This could be achieved by having several people working for short periods rather than one person working for several hours; however, it relies very much on each individual sticking to a specific time allocation.
All employees must understand the importance of following safe working procedures. The level of training will vary depending on the nature of the job, the level of risk and the competency of the person.
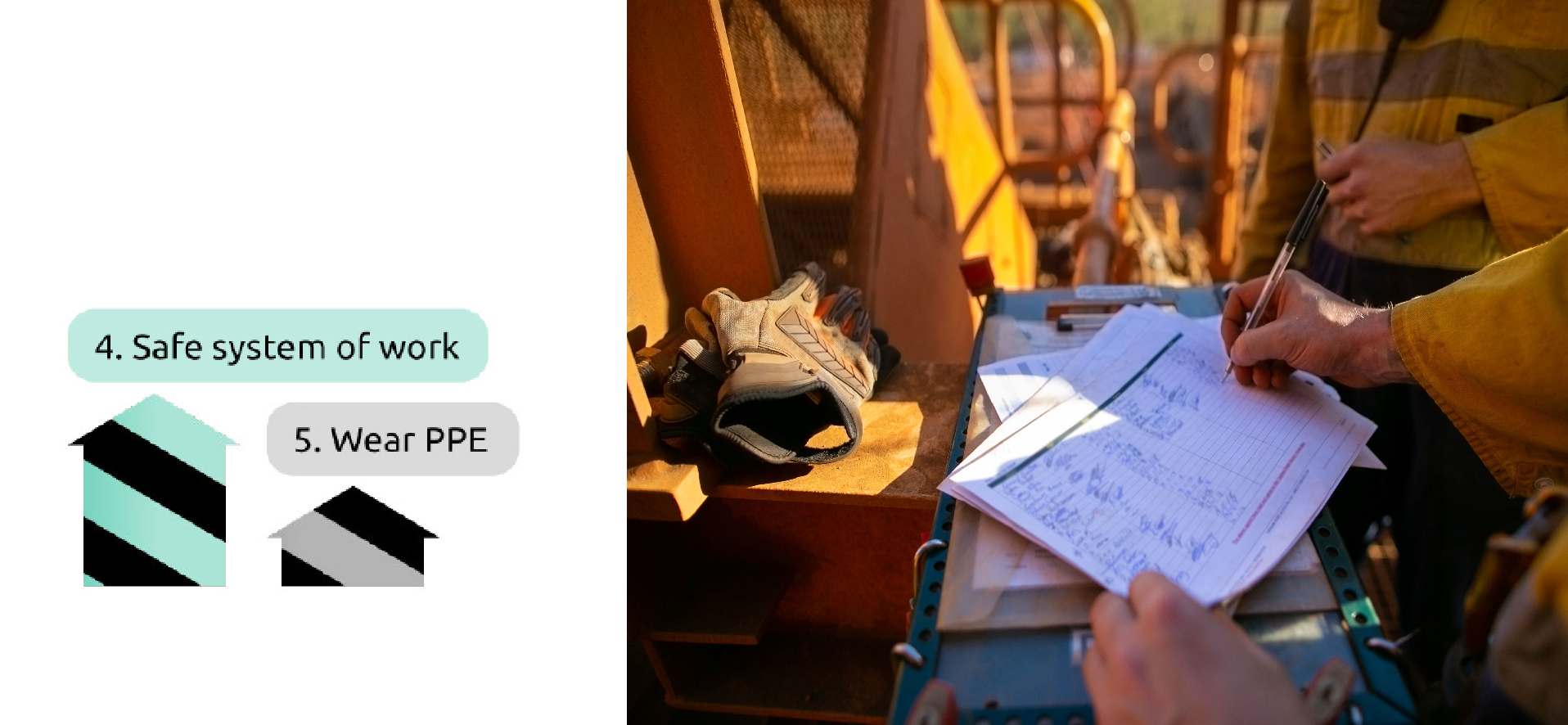
5. Wear PPE
Personal protective equipment (PPE) should always be considered as a last resort as it relies on people to use it properly. Only when there is no other alternative should PPE be provided.
The characteristics of the PPE should be clearly defined to ensure that it is suitable to withstand the risks it is to encounter. Employees should be actively involved in the selection of PPE to ensure that it is easy to use and maintained in an effective condition.
PPE includes goggles, respiratory protection, gloves, safety shoes and head protection.
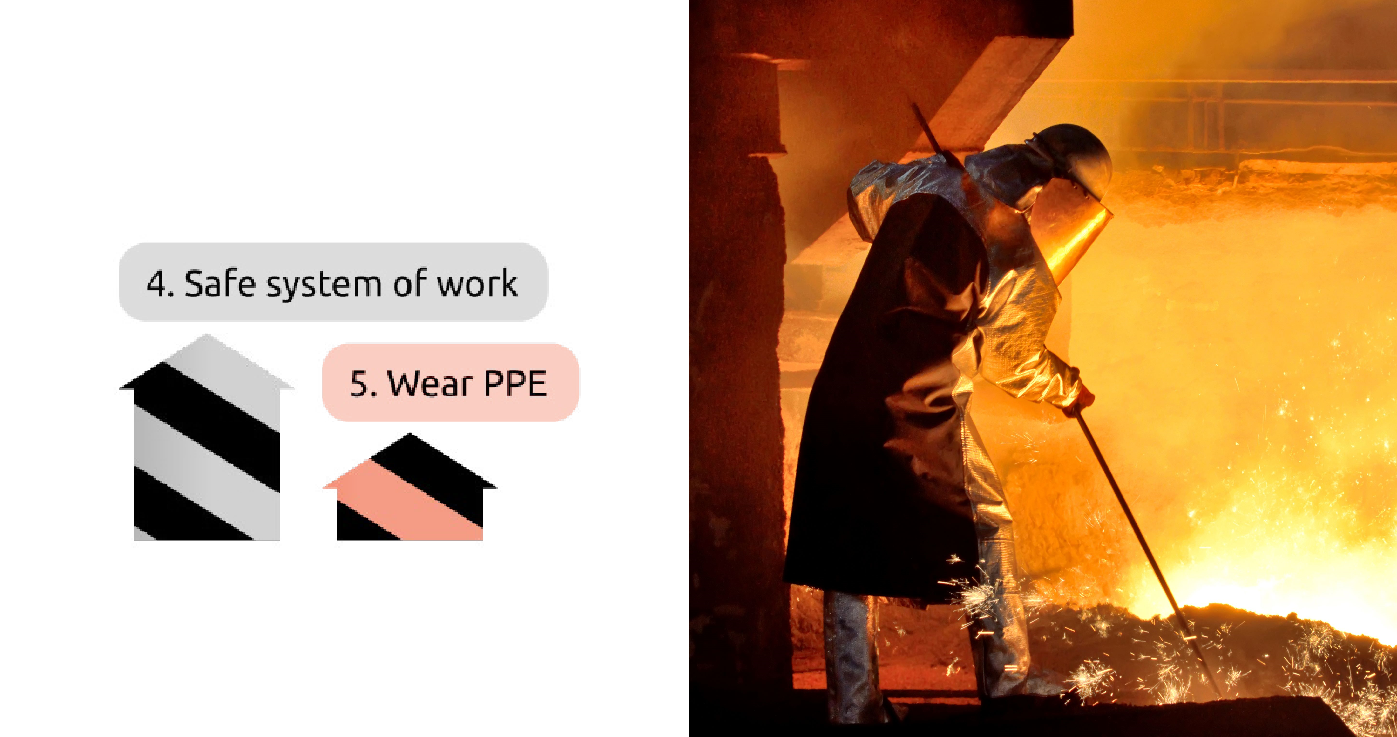
The benefits
The hierarchy of risk control shows the order in which you should try to choose your control measures, making it clear that you should start from the top of the hierarchy and work down. In practice, eliminating a hazard cannot always be done, so generally you will find yourself choosing a combination of control measures in order to reduce the risk to an acceptable level. Other factors may also influence your choice.
The number of people you’re trying to protect. How many people need protecting from the hazard? It is better to use a risk control measure that protects everyone who might be affected, rather than relying on people using their own protection.
Reliance on behaviour. Is the control measure only effective if used correctly? It’s always better to use something that doesn’t rely on human intervention.
Maintenance. If the control measure requires regular maintenance in order for it to stay effective, it may not always work.
Cost. How much does the risk control measure cost? Think about overall costs, including running and maintenance expenses.
Reduction of risk. Some risk control measures reduce risk more than others but may not necessarily be the right choice.
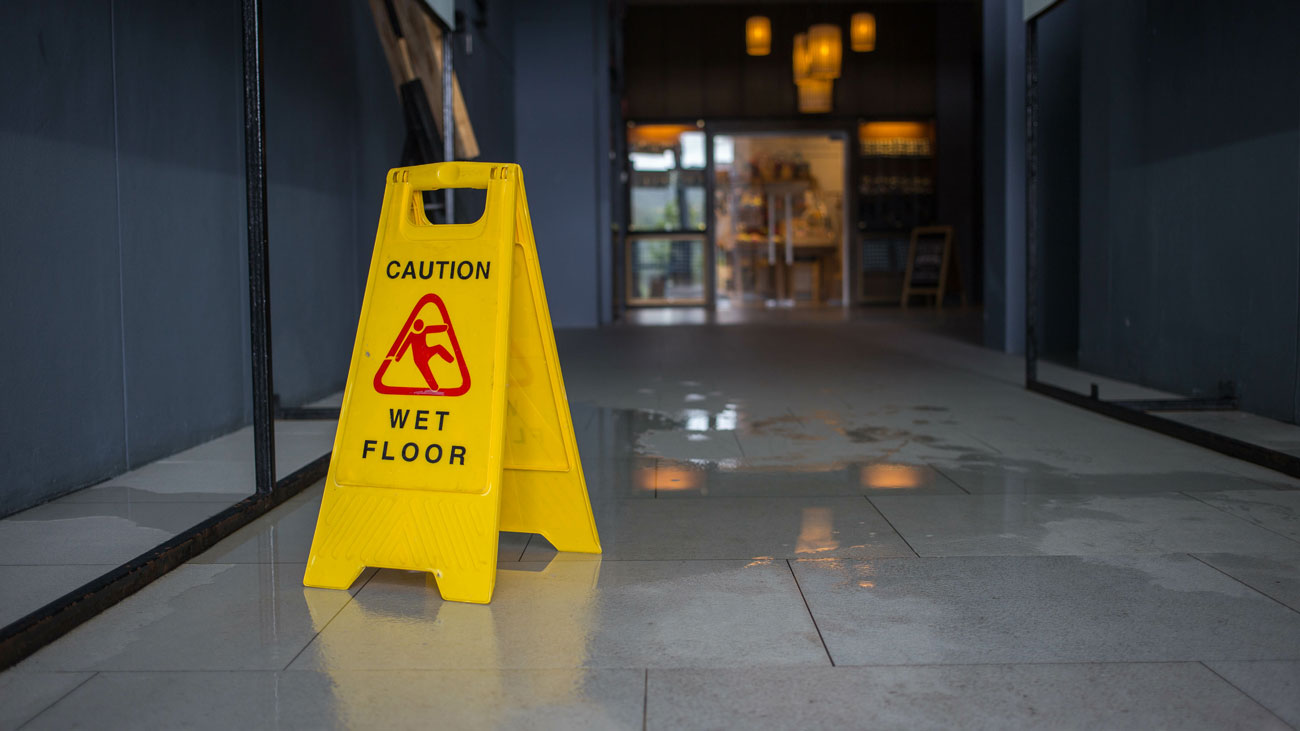
Key takeaways
-
Eliminating the hazard is the most effective method of reducing hazards in the workplace. Employers should always consider whether the job needs to be done in the first place, thereby eliminating the hazard altogether.
-
A hazard can be reduced by substituting it with a less hazardous solution. In many cases it may be possible to substitute, reduce or replace the machine, material, activity or other feature that introduces the hazard, by an alternative method of work.
-
Preventing people coming into contact with a hazard can be done in one of two ways – putting distance between people and the hazard or enclosing the hazard.
-
The introduction of safe systems of work will often make activities much safer. The extent of the safe system of work will depend on the nature of the activity and how dangerous the activity might be.
-
Personal protective equipment (PPE) should always be considered as a last resort as it relies on people to use it properly. Only when there is no other alternative should PPE be provided.
-
In practice, eliminating a hazard cannot always be done, so generally you will find yourself choosing a combination of control measures in order to reduce the risk to an acceptable level.
SOURCES:
You might also be interested in
RELATED CONTENT
RELATED COURSES
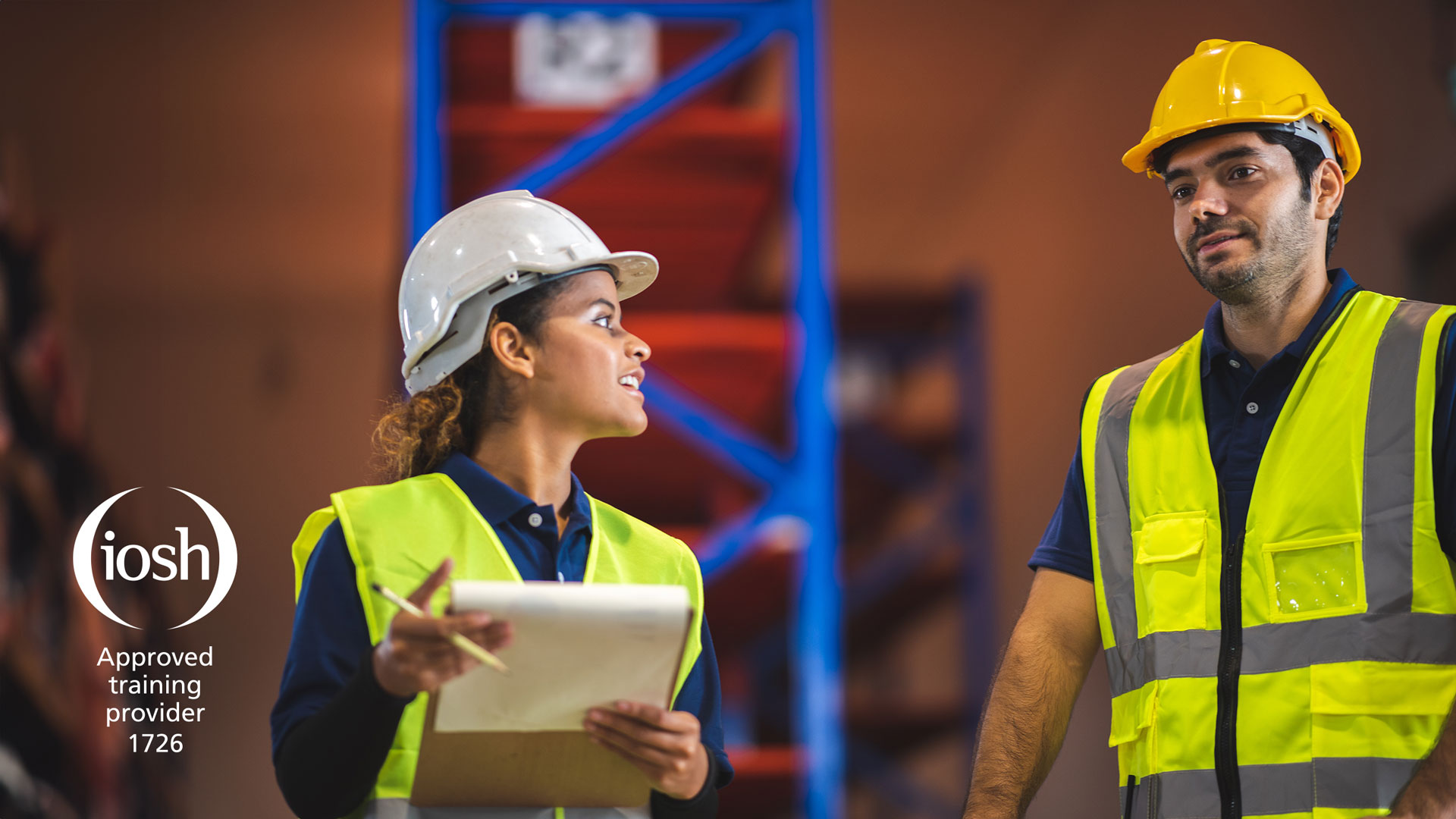
The world’s best-known health and safety certificate, designed for managers and supervisors in any sector or organisation.
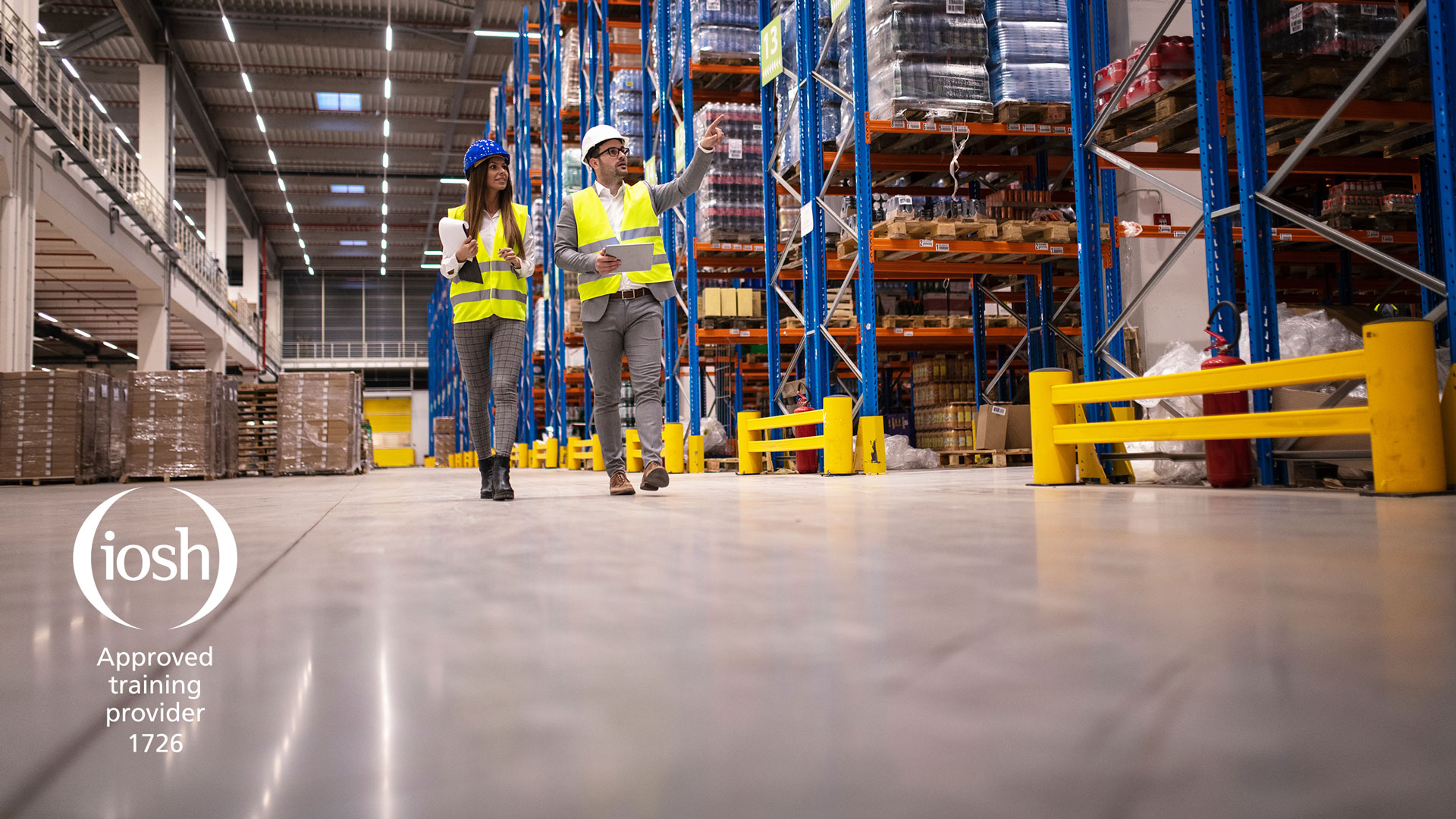
IOSH Managing Safely Refresher is designed to provide continued support to managers dealing with workplace health and safety issues.
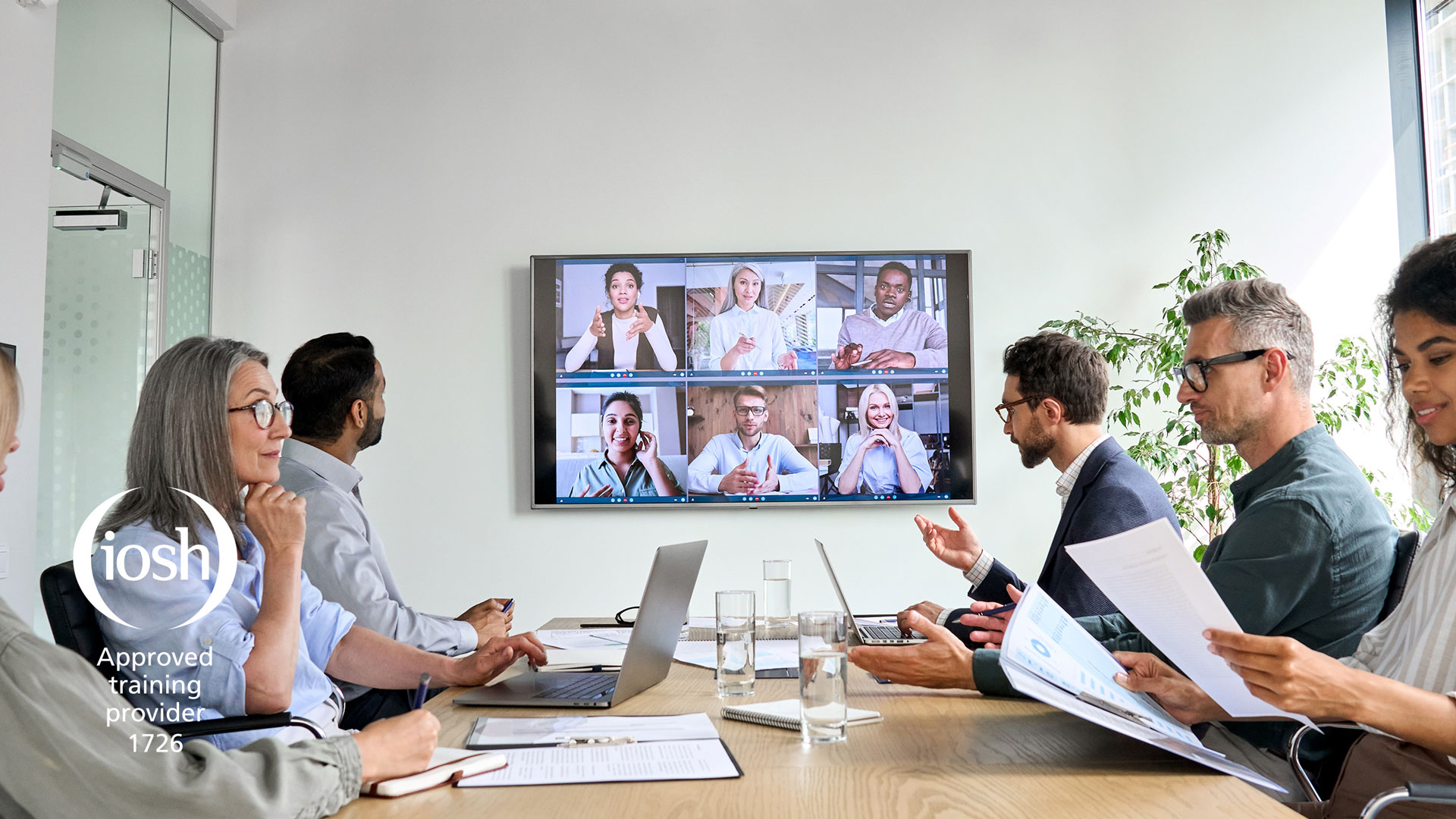
IOSH Safety for Executives and Directors is designed for those who have operational or strategic accountability for a company.
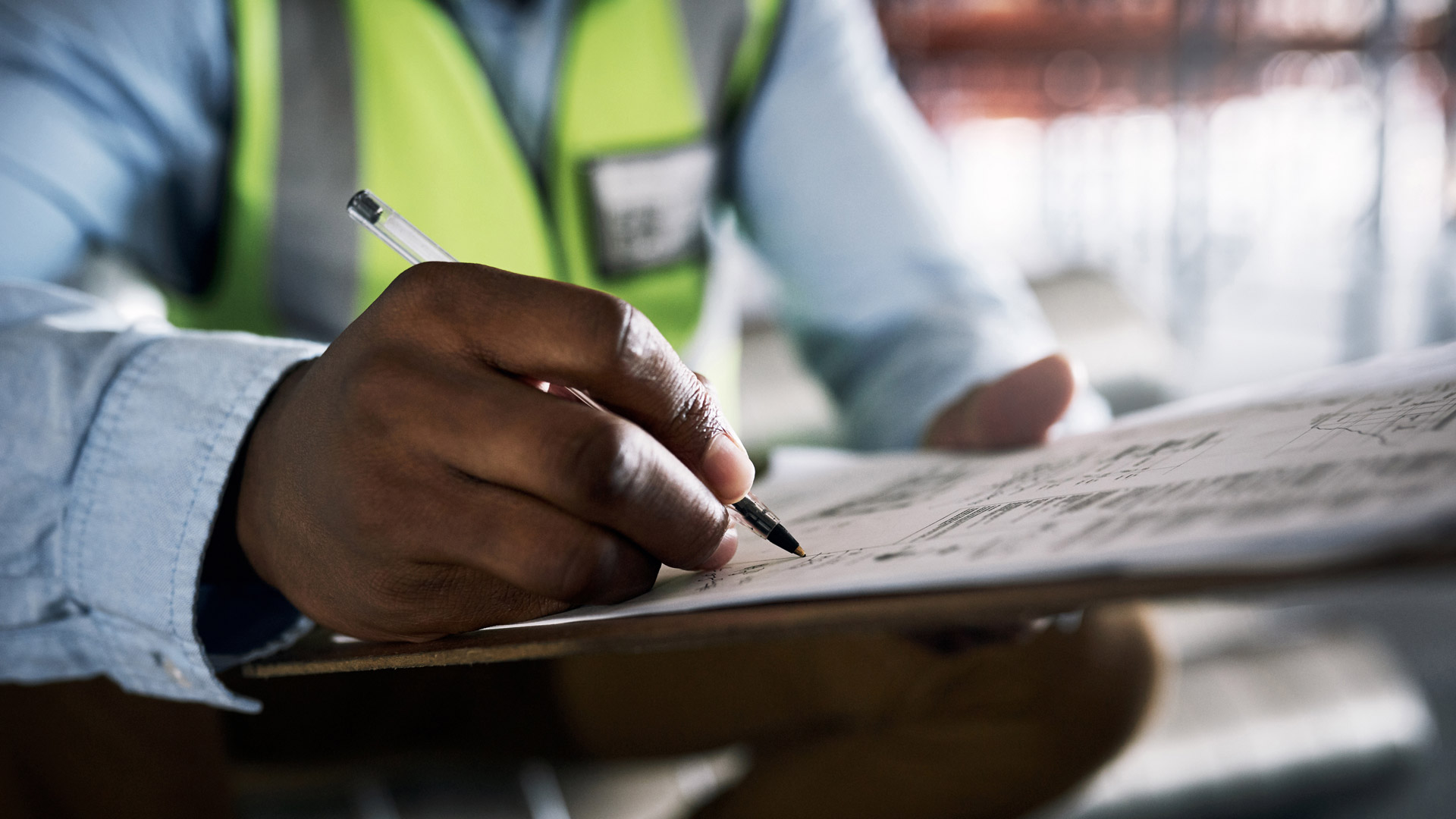
The Risk Assessment and Method Statement (RAMS) course examines the HSE’s recognised five-step approach to risk assessment.
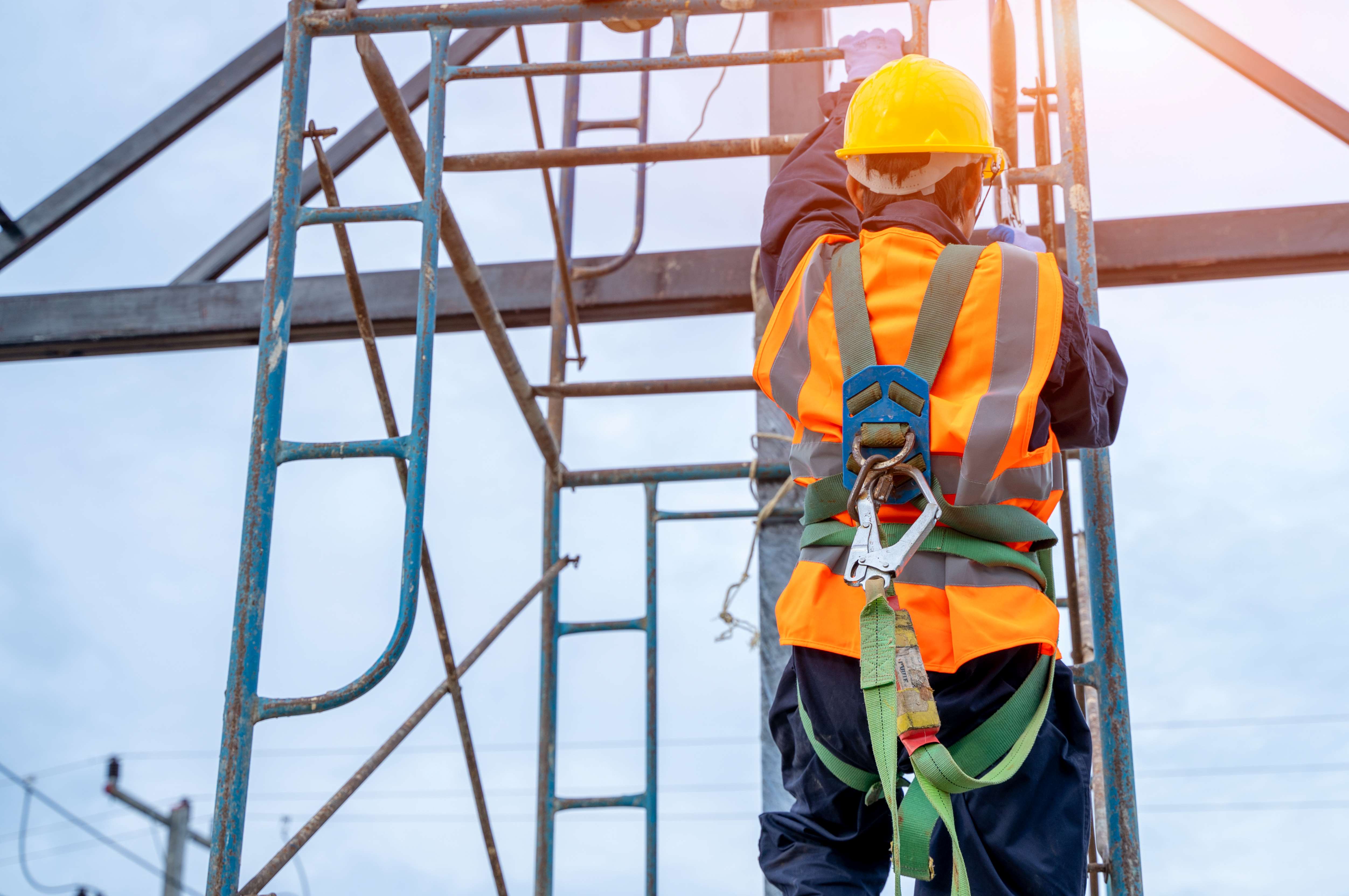
A Cheshire-based electrical transmission company has been fined £240,000 after a man was left paralysed from the chest down after a fall at work.
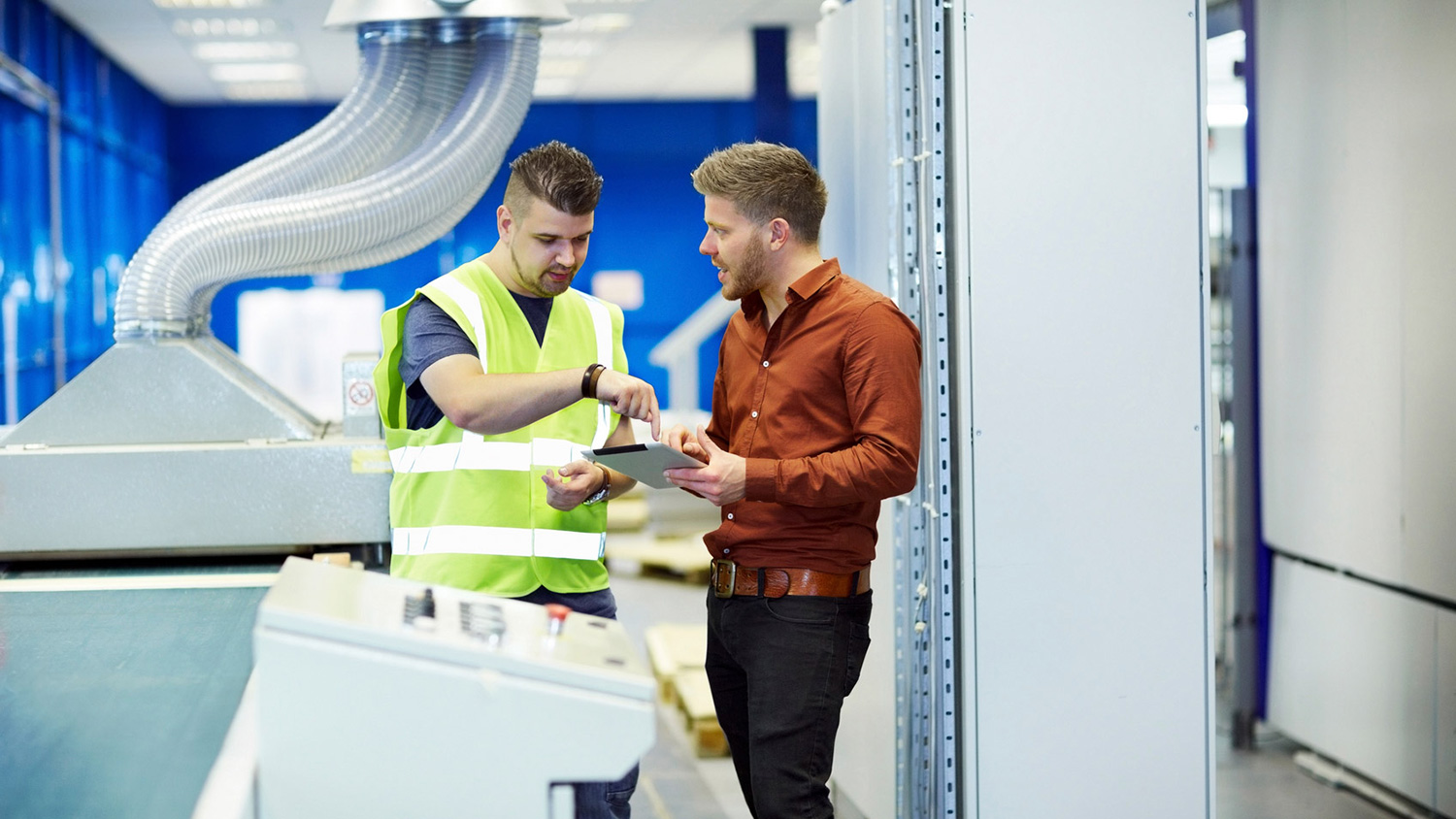
For industries and employers whose activity involves a fast-moving environment where things change rapidly and decisions need to be taken on the spot,...
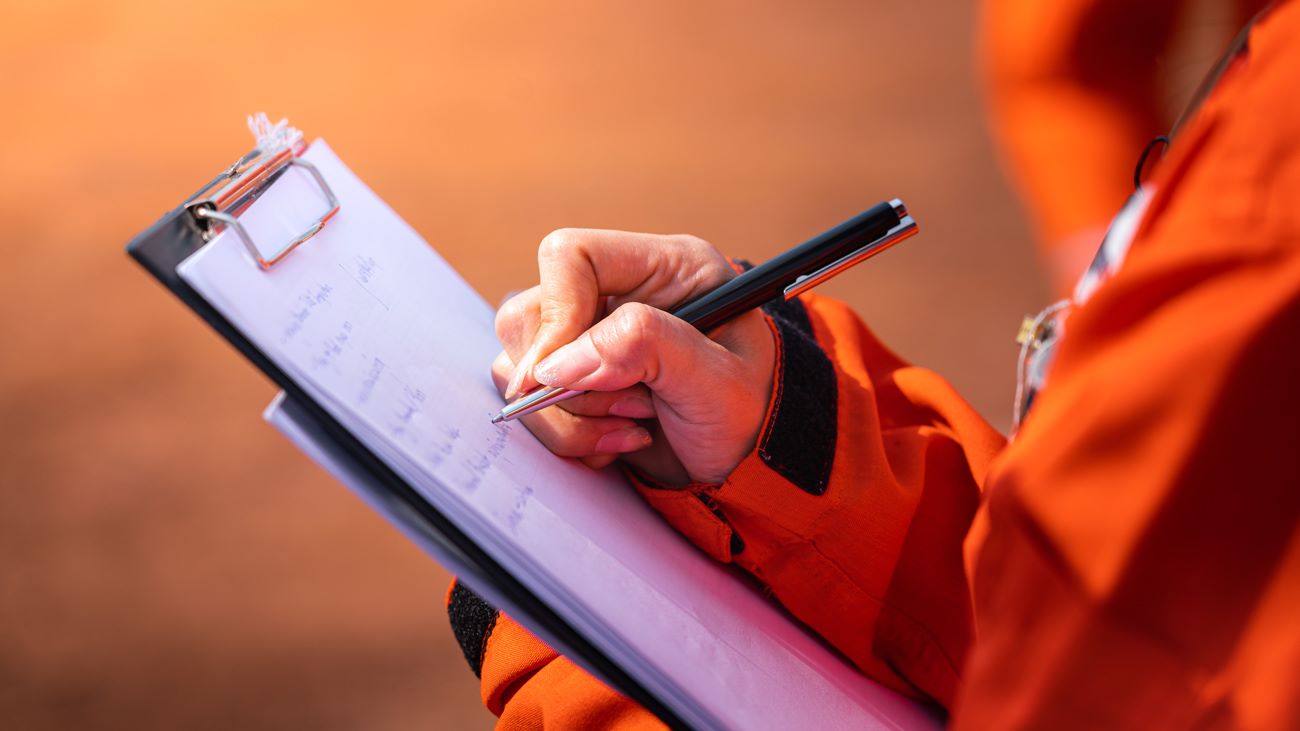
We all make assessments many times each day about the potential consequences that may arise from our actions.
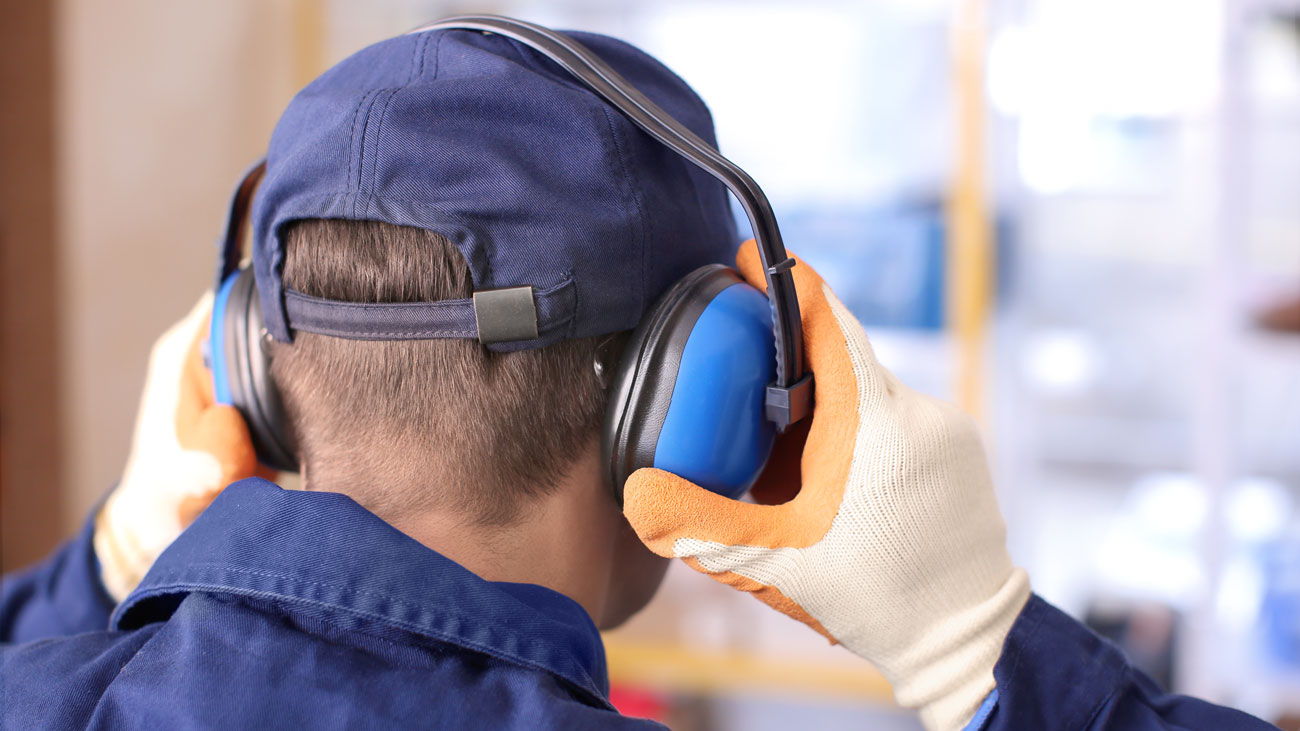
The British Safety Industry Federation (BSIF) has issued a warning to those overseeing personal protective equipment (PPE) and safety product procurem...