RISK
GUIDE
Common hazards in the workplace - a manager's guide
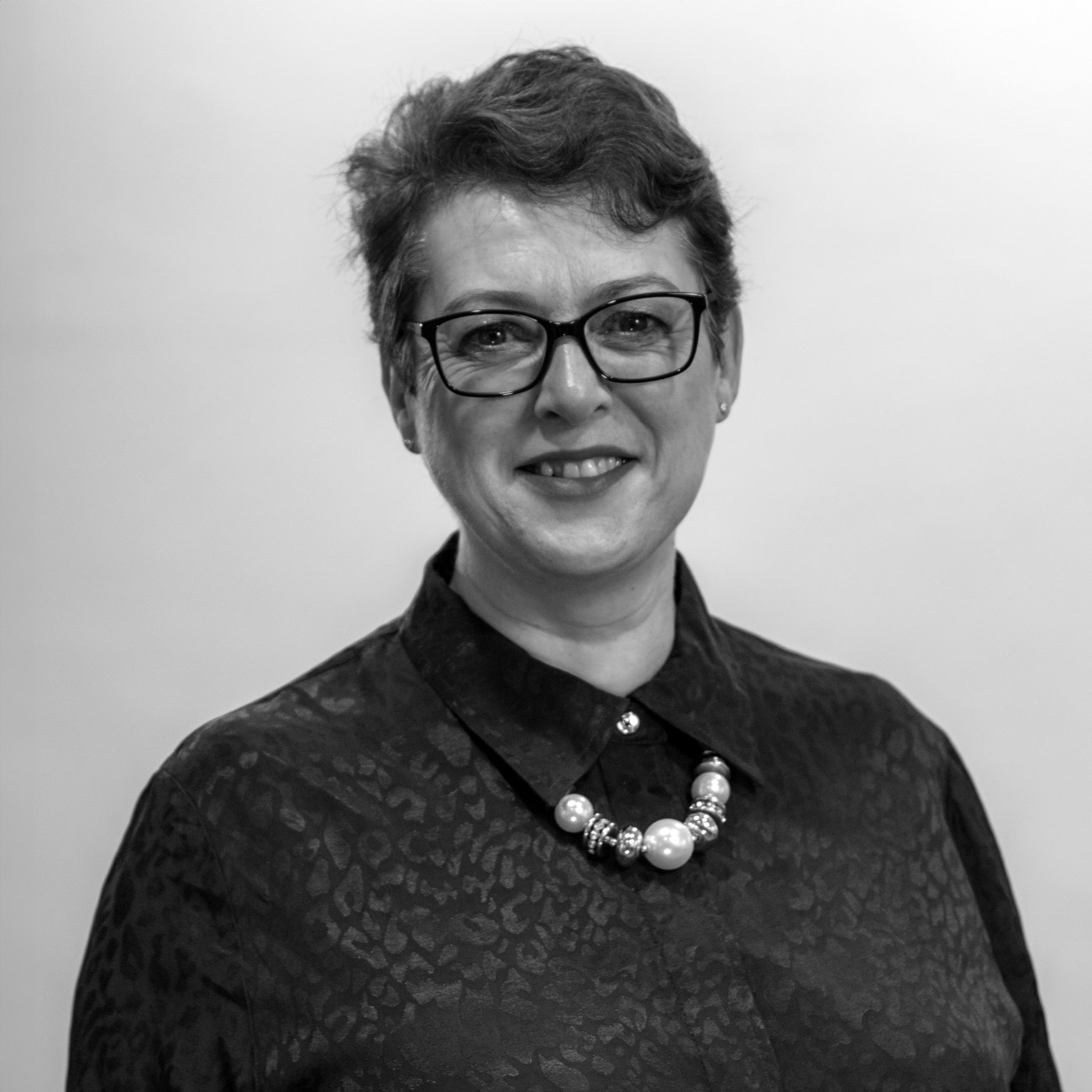
Published by Kate Gardner,
11 Dec 2024
Introduction
A hazard is something with the potential to cause harm. Harm means physical or mental damage or injury, as well as reduced quality of life and performance. Hazards in the workplace are potentially everywhere, and they most certainly should not be ignored or taken lightly.
Some industries naturally carry more risks but hazards can occur in workplaces of all types. As part of managing the health and safety of your business, you must control the risks in your workplace. To do this you need to think about what might cause harm to people and decide whether you are taking reasonable steps to prevent that harm.
This guide takes you through the main hazards found in the workplace and control measures to manage them.
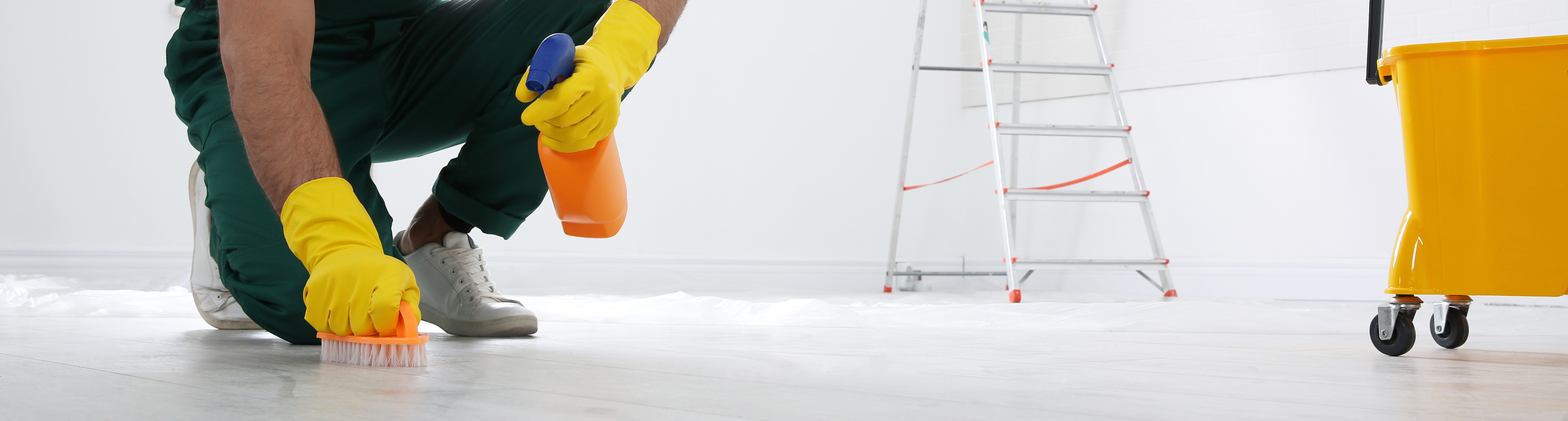
How is harm gauged?
Harm can be gauged in the following ways:
- How much? (Quantity)
- How often? (Frequency)
- How long? (Duration)
- How susceptible is a person to the type of harm? (Condition)
The harm arising from a great many common hazards can be understood in these terms.
One way of classifying hazards is to group them by the general category of harm they cause, such as:
- Mechanical
- Physical
- Chemical
- Biological
- Environmental
- Organisational
Let's go through these in turn.
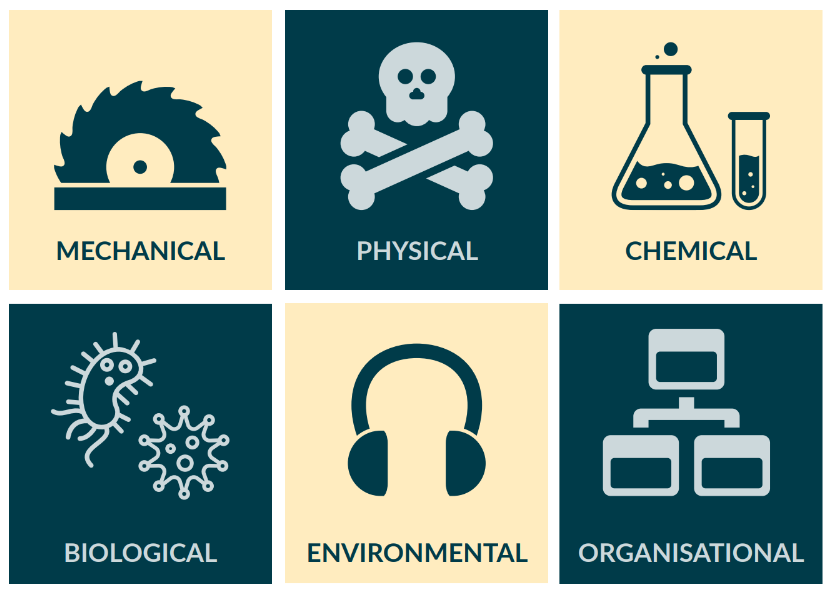
Mechanical hazards
A mechanical hazard is any hazard involving a machine or process. Mechanical hazards are created by the powered operation of apparatus or tools, which may be machine-generated or human.
Mechanical hazards can be categorised according to the type of injury caused:
- Crushing – when part of the body is caught between a moving part of a machine and a fixed object.
- Shearing – when part of the body is subjected to a scissor action from equipment.
- Cutting and severing – when part of the body comes into contact with a saw or knife.
- Entanglement – when clothing or hair comes into contact with rotating objects or catches.
- Drawing-in or trapping – when part of the body is caught between two counter-rotating parts.
- Impact – when a moving object strikes part of the body.
- Stabbing and puncture – when flying or ejected objects penetrate the body.
- Friction and abrasion – when moving or abrasive surfaces make contact with parts of the body.
- High-pressure fluid injection – when a sudden release of fluid under pressure causes tissue damage.
Control measures include:
Ensure that all equipment and machinery is used safely in the workplace.
Make sure employees know:
- How to operate equipment;
- What safety precautions are required;
- What pre-use checks might be required; and
- Where to find any operating instructions / manuals.
Equipment provided for use at work should be:
- Suitable for its intended use;
- Safe for use, maintained in a safe condition and, in certain circumstances, inspected to ensure this remains the case;
- Used only by people who have received adequate information, instruction and training; and
- Accompanied by suitable safety measures, e.g. protective devices, markings, warnings.
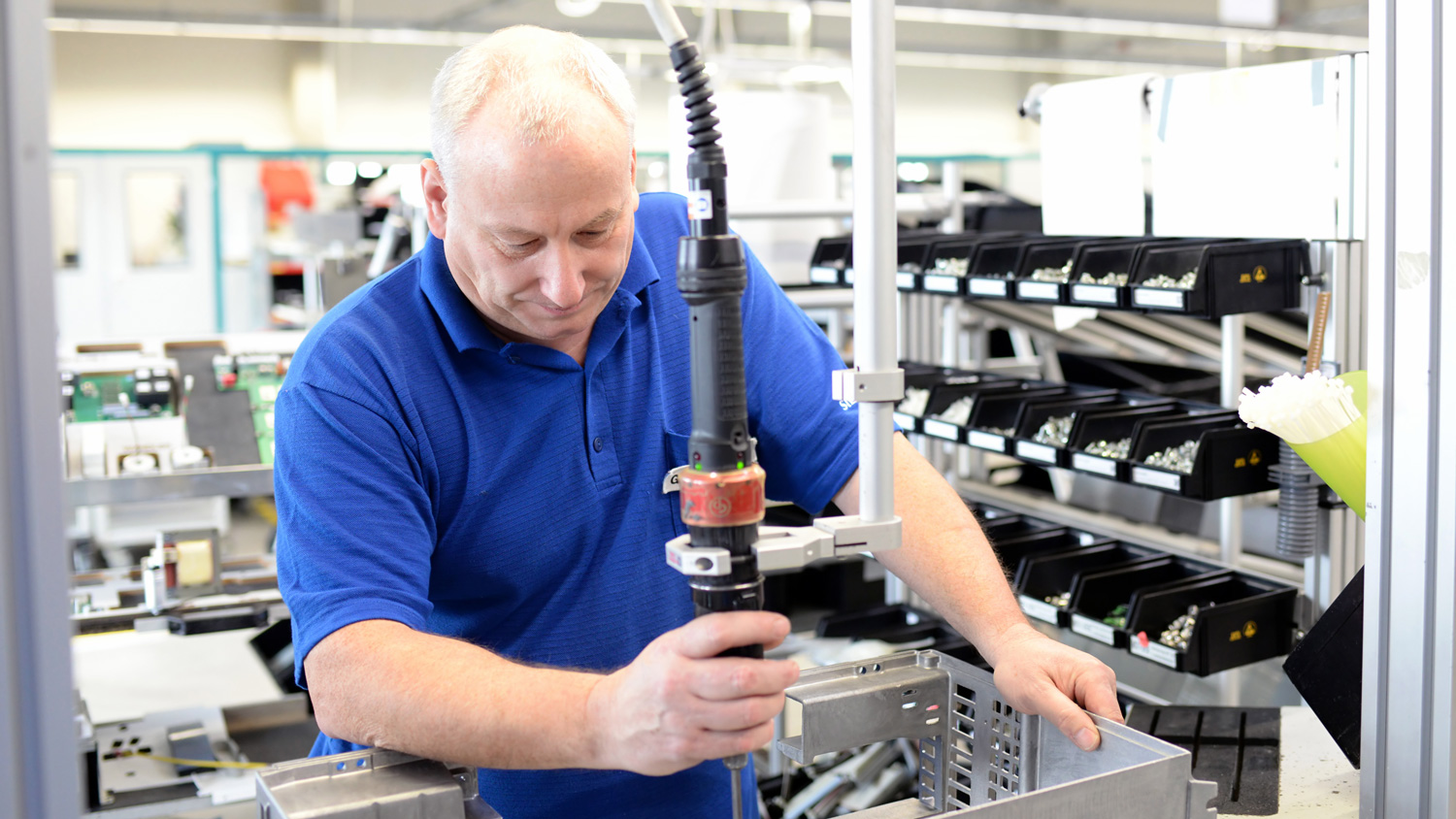
Physical hazards
Physical hazards are those substances or conditions that may harm a person’s physical safety. A physical hazard is a naturally-occurring process that has the potential to cause injury, illness and death, including:
- Tripping;
- Slipping;
- Falling from a height or on a level; and/or
- Being struck by a falling object.
Physical hazards are usually overlooked because of familiarity, or a resistance to spend time and money on improvements. However, slips and trips are the most common cause of major injuries at work.
Physical hazards also include ergonomic hazards – a physical factor within the environment that harms the musculoskeletal system. Working conditions or body positions often put strain on the body when a worker’s capacity for work is restricted by the type of work. Ergonomic hazards include repetitive movement, manual handling, workplace / job / task design, uncomfortable workstation height and poor body positioning.
Fire is included amongst physical hazards, as is noise, pressure and vibration.
Control measures include:
- Recognise the risk.
- Provide a safe system of work and make sure it’s followed.
- Provide adequate information, training, instruction and supervision.
- Use appropriate equipment properly
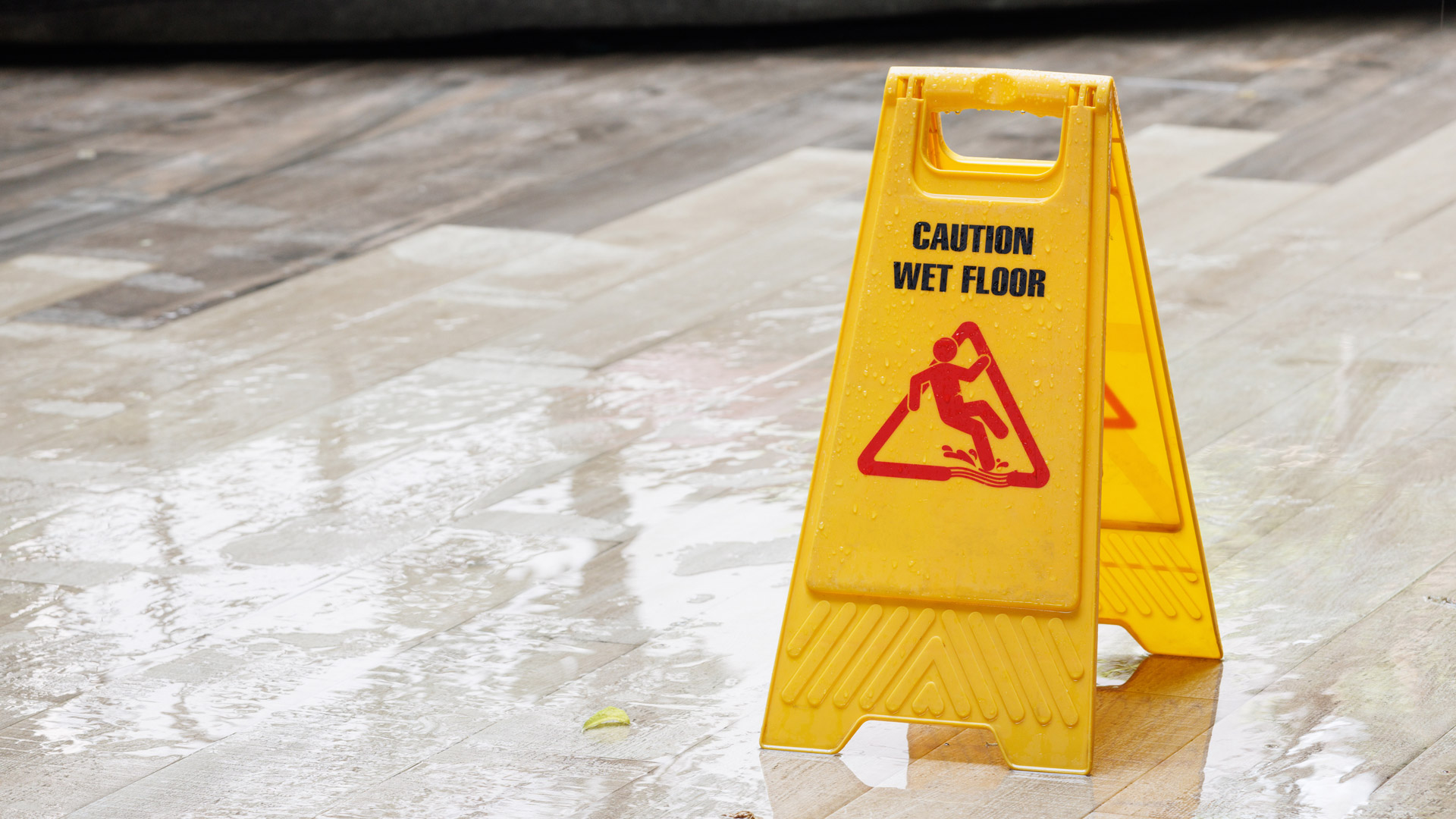
Chemical hazards
Chemicals are considered a hazard due to their intrinsic properties to cause harm to humans, property or the environment. Chemical hazards can be presented by substances that are:
- Used directly in work activities (for example, adhesives, paints, cleaning materials).
- Generated during work activities (for example, fumes from soldering and welding).
Chemicals can harm a person’s health when entering the body by absorption through the skin, ingestion through the mouth, and inhalation through the lungs.
Most people associate chemicals with certain professions and workplaces such as laboratories; however, chemicals are found in many common workplace products. While these chemicals have a variety of beneficial uses, they can also be extremely harmful if they are misused.
Control measures:
The hierarchy of control should be used when controlling exposure to hazardous substances.
- Eliminate the use of the substance. Do you need to use it?
- Reduce the hazard by substituting with a less harmful substance. Can you replace it with a less harmful product?
- Prevent contact by isolating or enclosing the process.
- Employ safe systems of work by ensuring good welfare and personal hygiene and adequate washing facilities.
- Supply PPE – provide personal protective equipment, such as gloves, goggles and masks,
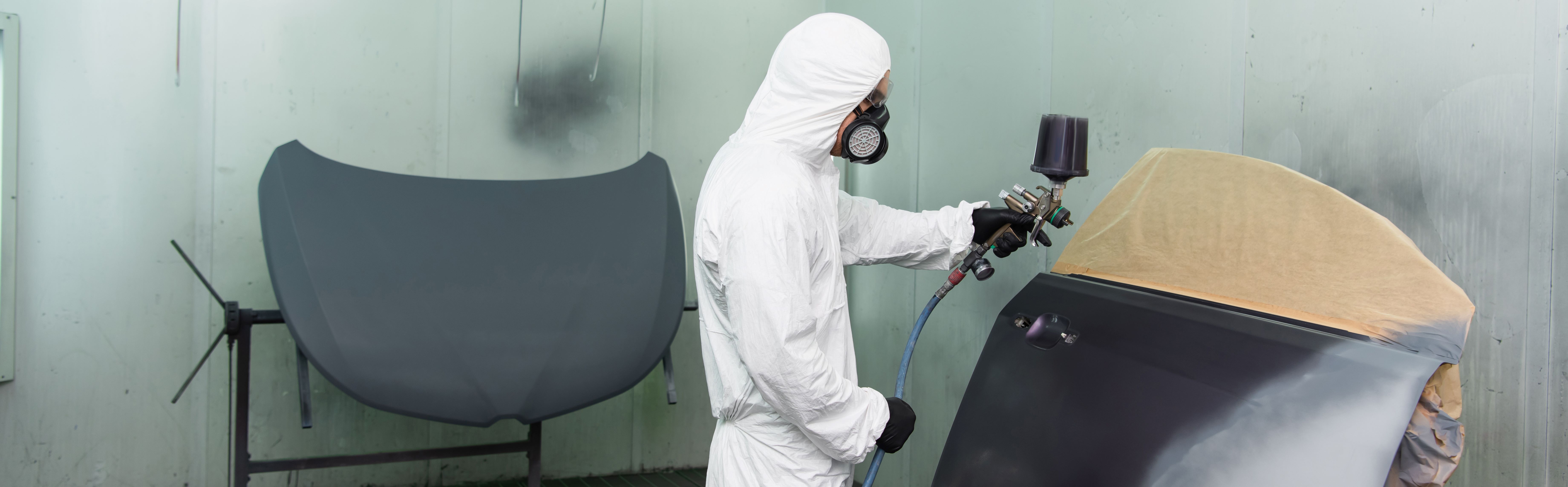
Biological hazards
Biological hazards are organic substances or microorganisms that pose a threat to the health of humans and other living organisms. Biological hazards also include toxins that are produced by organisms.
Biological hazards pose risks for many workers in a variety of ways. People working with microorganisms (such as in laboratories) are at a high risk of exposure, but other examples of work activities that may bring people into contact with biological hazards include:
- Working with animals – for example, farming.
- Working with people who might be infectious – for example, healthcare professionals.
- Handling waste materials – for example, refuse disposal.
- Working in an environment or with equipment that could be contaminated – for example, sewer maintenance.
Control measures:
Again, the hierarchy of control can be used here.
- Eliminate exposure, if possible.
- Reduce the hazard by substituting the biological substance with something less harmful.
- Prevent contact by isolating or enclosing the process.
- Employ safe systems of work by ensuring good welfare and personal hygiene and adequate washing facilities.
- Supply PPE – provide personal protective equipment, such as gloves, goggles and masks.
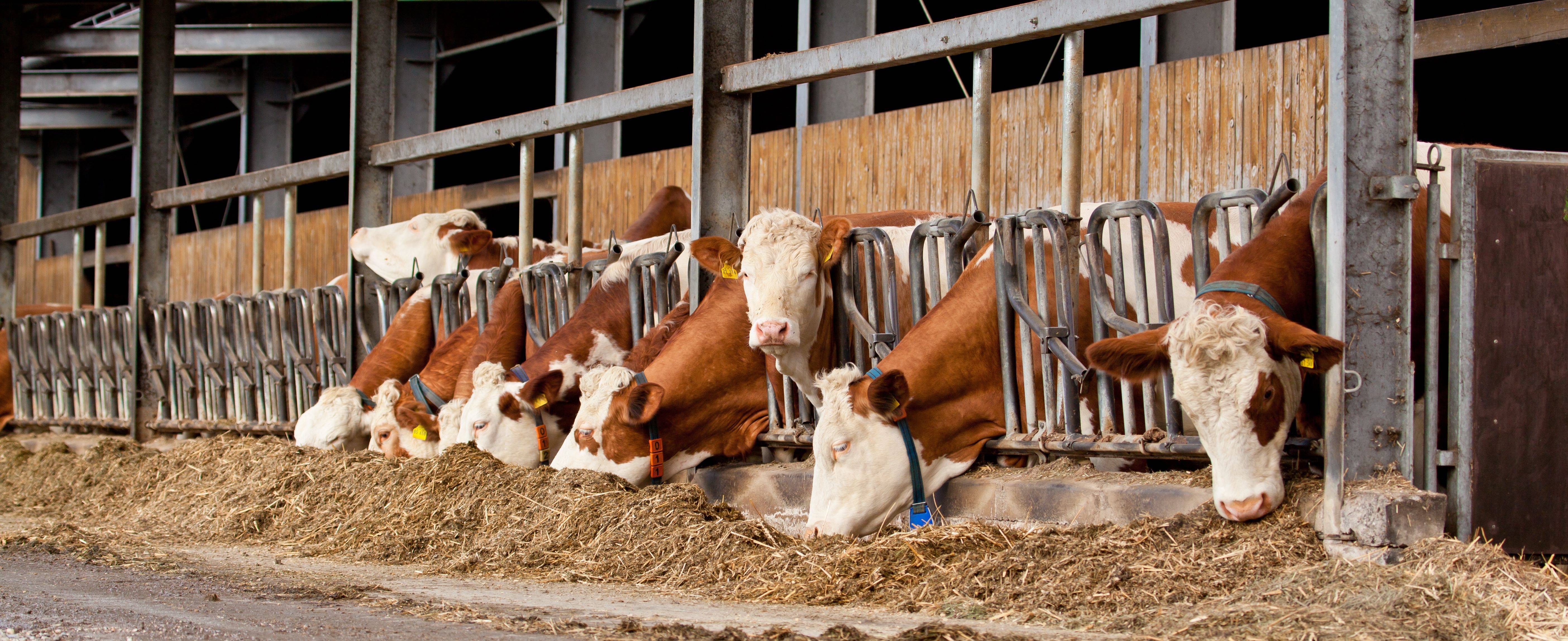
Environmental hazards
Environmental hazards have the potential to affect the environment and adversely impact people’s health. These hazards come in various forms and are often unnoticed until an accident occurs. Environmental hazards can include poor lighting, unreasonable temperatures and dust.
Understanding the various environmental hazards that exist and taking precautions can help prevent accidents. Balancing work activities and work rates with the right temperature, humidity, air movement, clothing, food and drink intake, body build and psychosocial factors is important for workers’ efficiency, comfort and safety.
Control measures include:
- Enclosed workspaces should be sufficiently ventilated, which means the air is replaced with fresh air on a consistent basis.
- The temperature in all internal rooms must be reasonable, which will vary according to what kind of activity is taking place.
- Noise should be monitored and managed according to the hierarchy of control – from elimination at source down to providing PPE as a last resort.
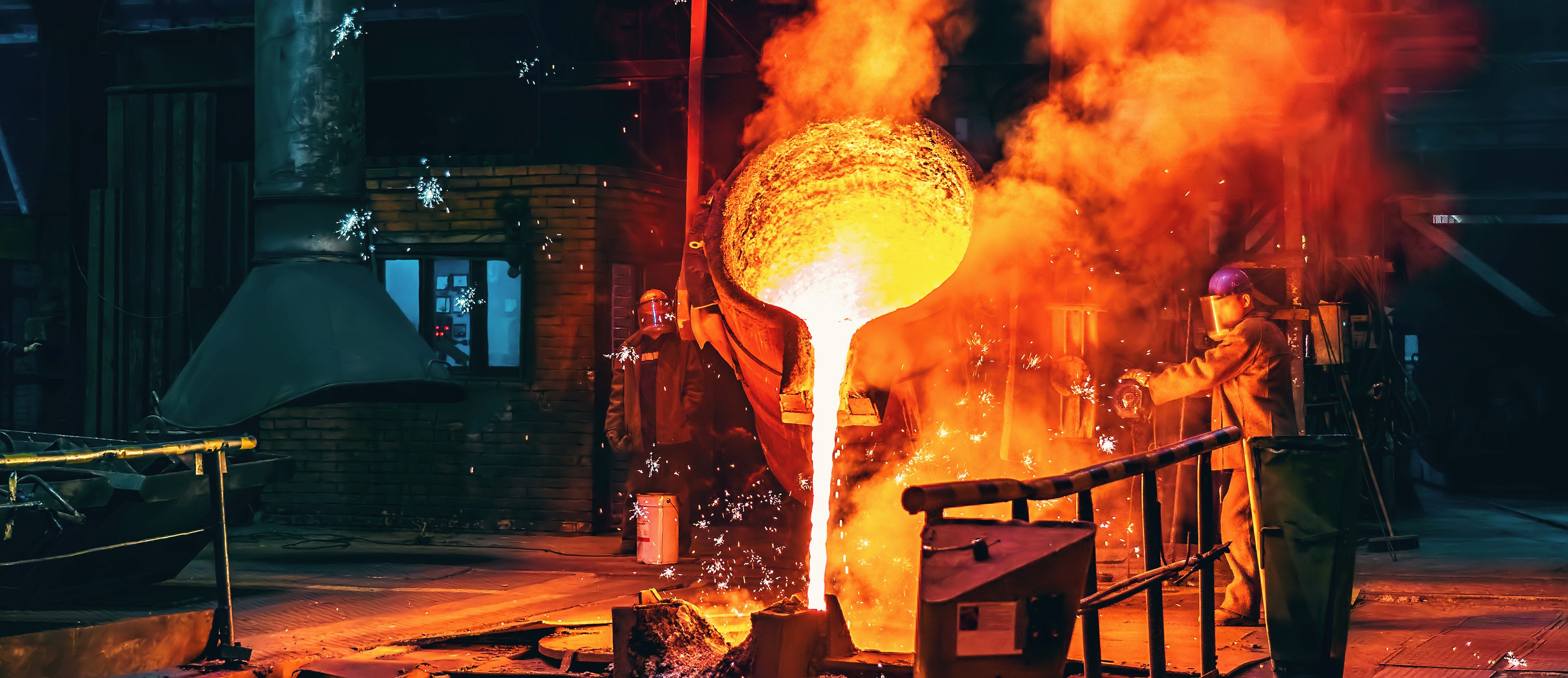
Organisational hazards
Organisational hazards are associated with behaviour, workload, time constraints and deadlines. Studies have shown that the following have the potential to be stressful:
- Temporal aspects of work – for example, shift work, overtime.
- Work content – for example, nature of tasks and level of autonomy.
- Interpersonal issues within a team – for example, interaction with co-workers, equality of workload.
- Interpersonal issues with supervisors – for example, provision and receipt of feedback.
- Organisational structures.
The ideal workload should be organised and balanced, to avoid fatigue on the one hand, and on the other, to ensure employees are engaged and being productive.
Control measures:
It’s important that managers understand how the following can impact their staff:
- Demands – workload, work patterns and the work environment.
- Control – how much say the person has in the way they do their work.
- Support – encouragement, sponsorship and resources provided by the organisation, line management and colleagues.
- Relationships – promoting positive working to avoid conflict and dealing with unacceptable behaviour.
- Role – whether people understand their role within the organisation and whether the organisation ensures that they do not have conflicting roles.
- Change – how organisational change (large or small) is managed and communicated in the organisation.
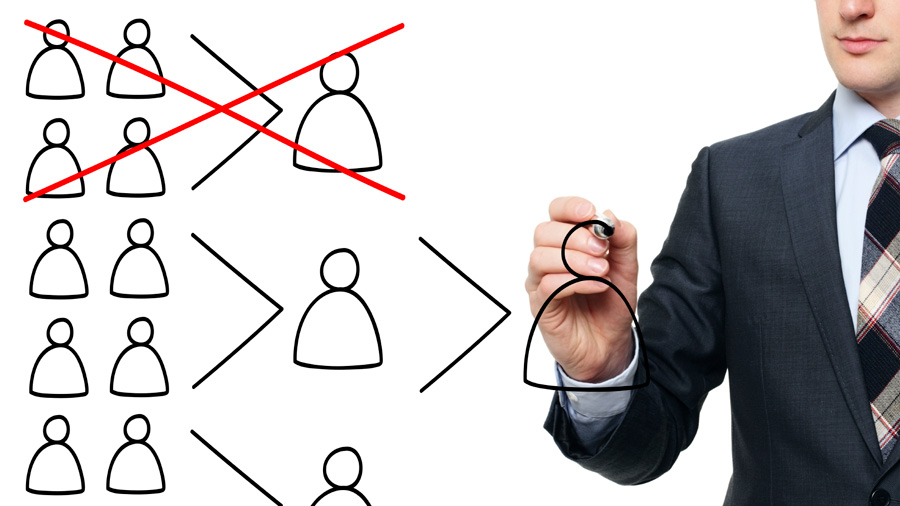
Conclusion
When classifying hazards like this there is potential for some ambiguity. For example, a toxin produced by a micro-organism that is present in inhalable dust could easily be classified in more than one category: there are environmental, biological and chemical components. Almost every hazard situation is going to have an organisational component.
However, the main benefit of the six categories is that it is hard to think of any hazard that does not fit into one of the categories. So, if you examine a workplace to find several examples in each category of hazard, you will have a very thorough risk assessment as a result.
Key takeaways
-
A hazard is something with the potential to cause harm. Harm means physical or mental damage or injury, as well as reduced quality of life and performance.
-
One way of classifying hazards is to group them by the general category of harm they cause, such as mechanical, physical, chemical, biological, environmental, organisational.
-
A mechanical hazard is any hazard involving a machine or process.
-
Physical hazards are those substances or conditions that may harm a person’s physical safety.
-
Chemicals are considered a hazard due to their intrinsic properties to cause harm to humans, property or the environment.
-
Biological hazards are organic substances or microorganisms that pose a threat to the health of humans and other living organisms.
-
Environmental hazards have the potential to affect the environment and adversely impact people’s health.
-
Organisational hazards are associated with behaviour, workload, time constraints and deadlines.
-
A lot of the control measures that apply to one hazard will work just as well to another.
-
If you examine a workplace to find several examples in each category of hazard, you will have a very thorough risk assessment as a result.
SOURCES:
You might also be interested in
RELATED CONTENT
RELATED COURSES
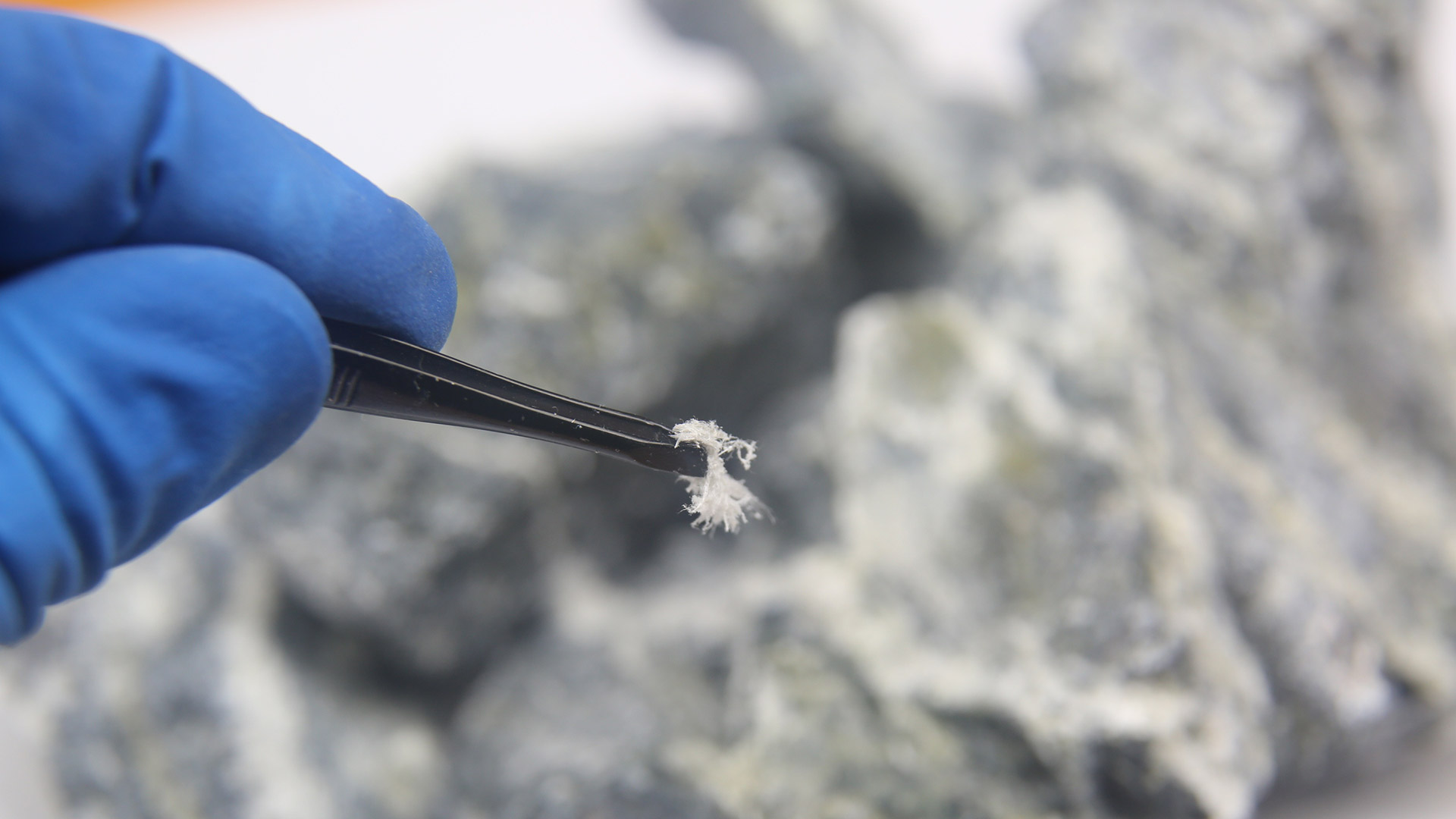
The asbestos course looks at how to manage asbestos in the workplace and recognise the risks.
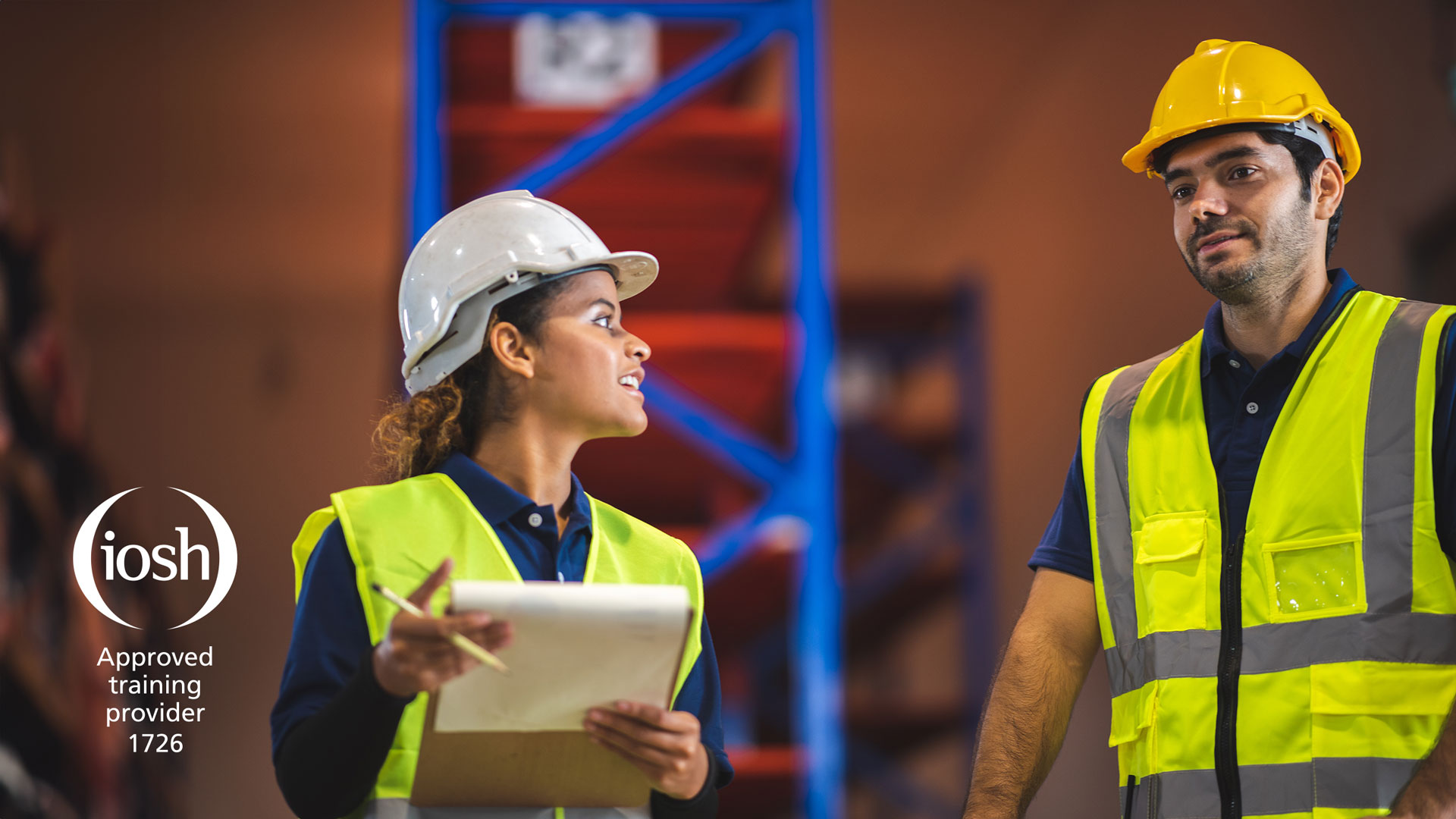
The world’s best-known health and safety certificate, designed for managers and supervisors in any sector or organisation.
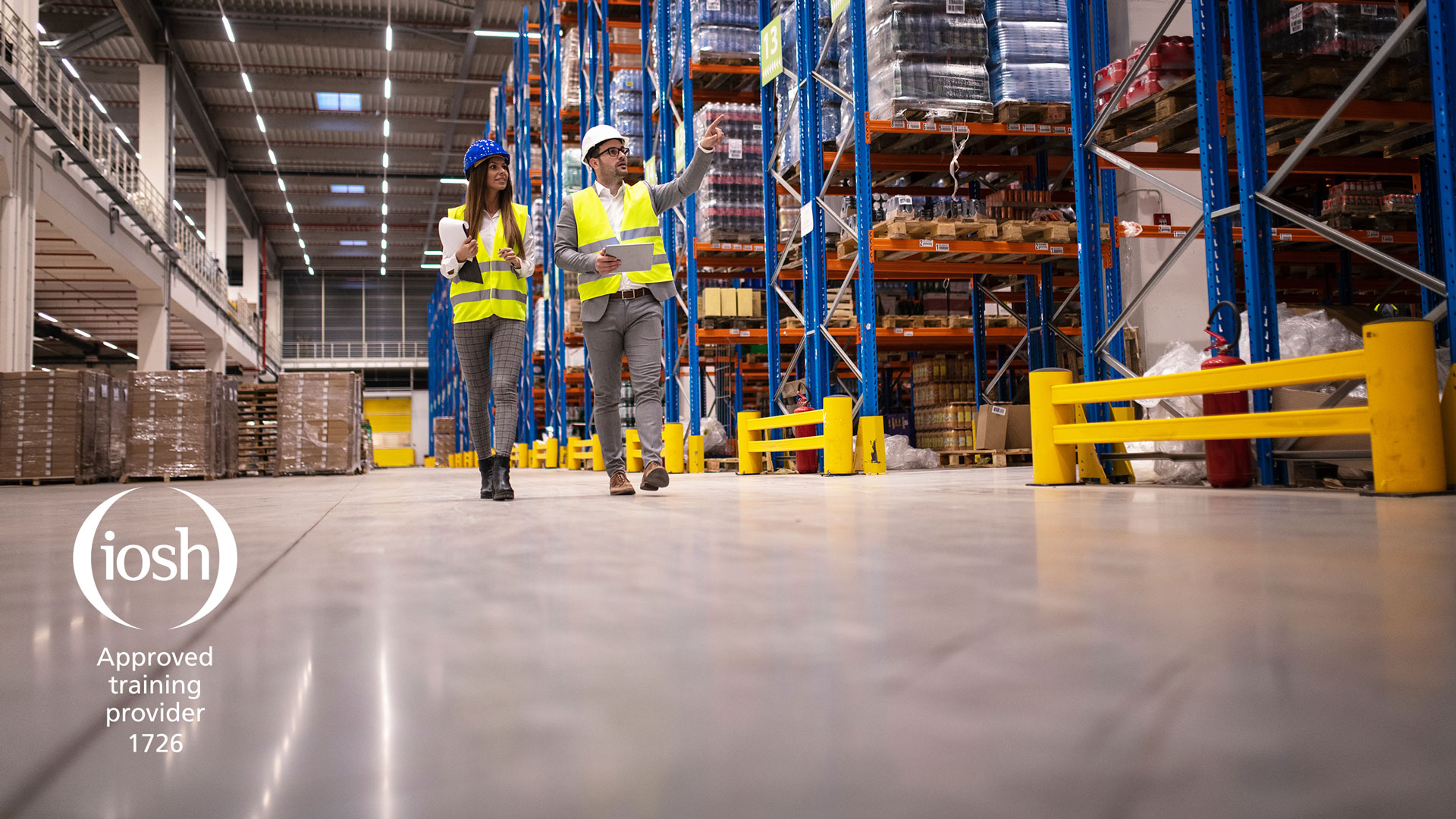
IOSH Managing Safely Refresher is designed to provide continued support to managers dealing with workplace health and safety issues.
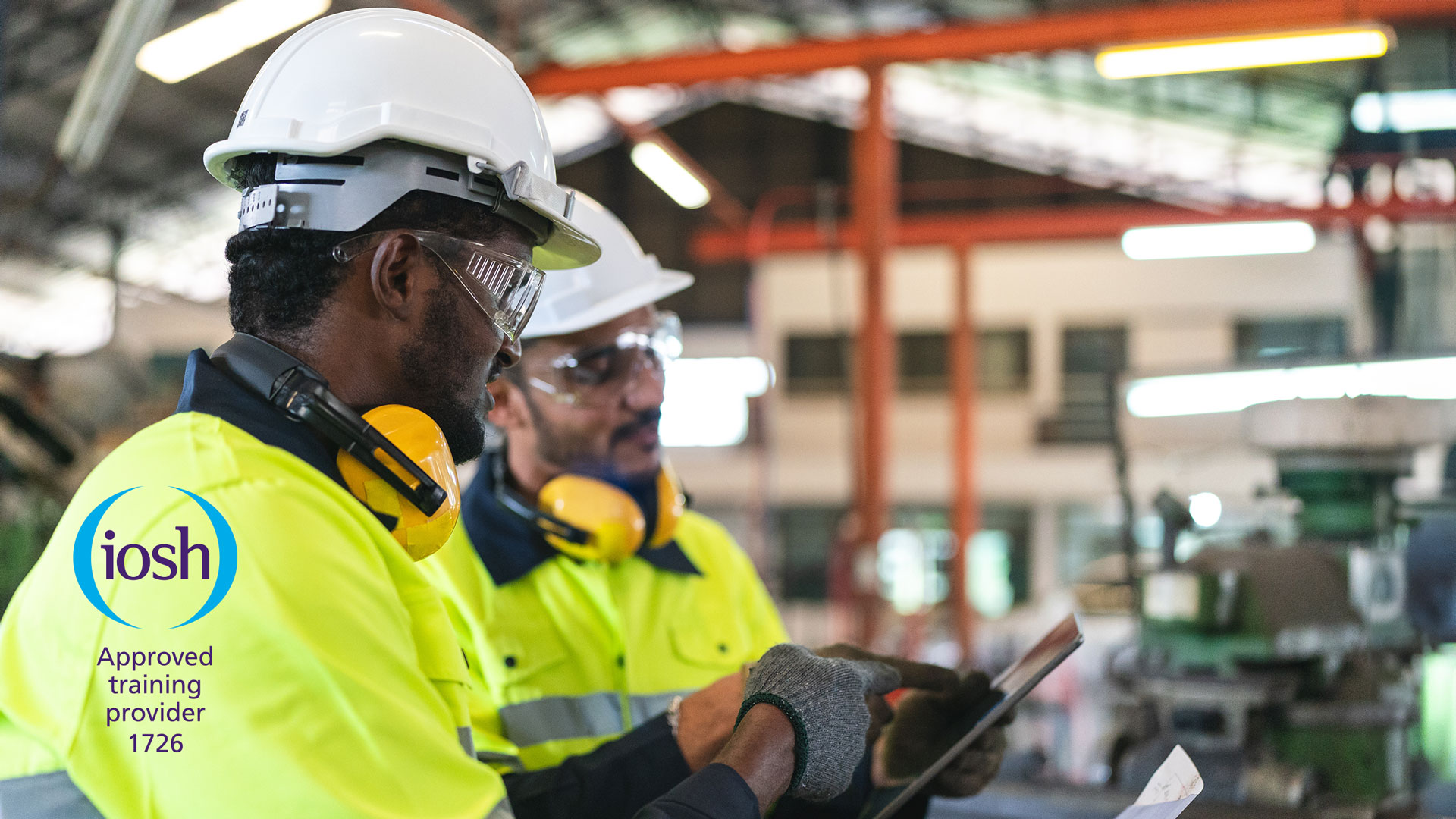
IOSH Working Safely is a one-day introductory health and safety training course for people at any level, in any sector.
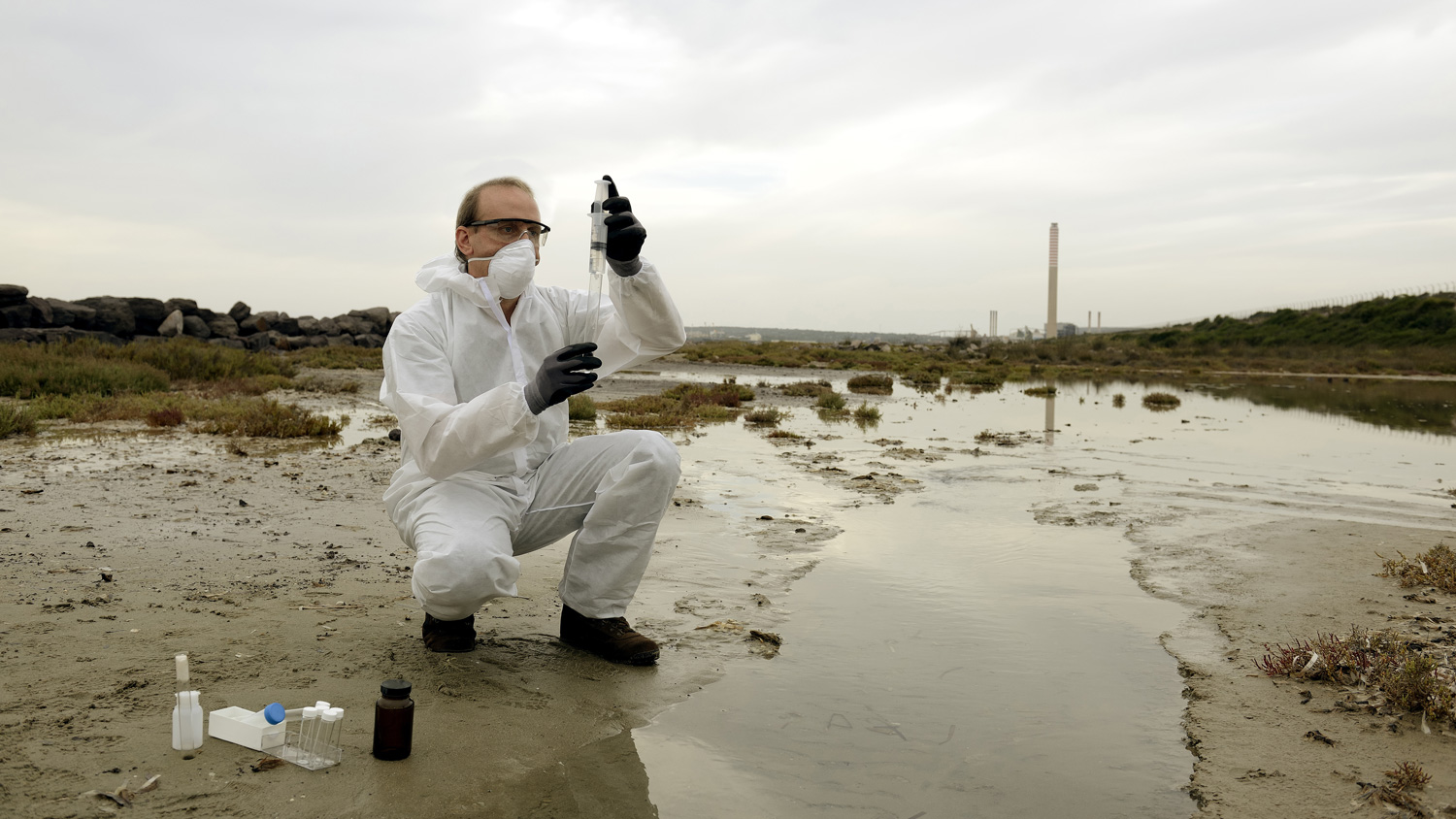
The UK government has announced it will not match new EU restrictions on various potentially hazardous chemicals, including the “rubber crumbs” used t...
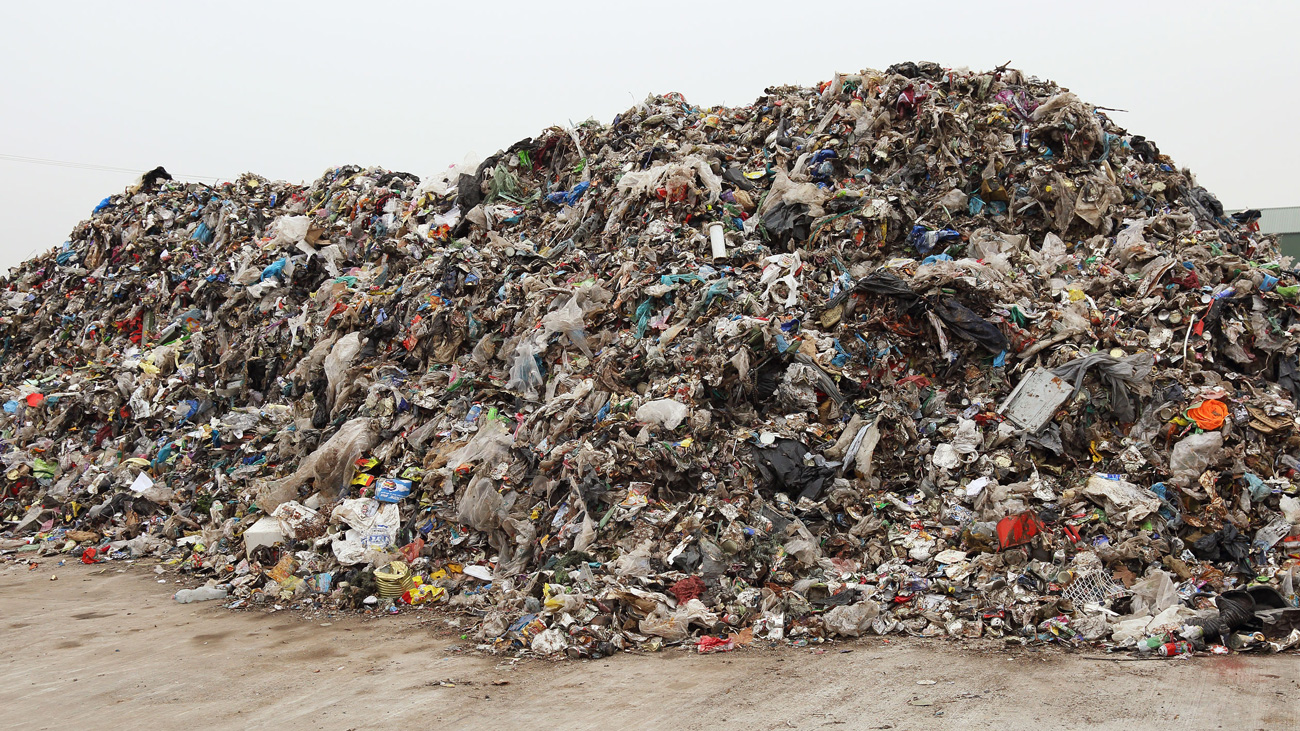
A survey of nearly 1,700 people across the recycling and waste management sector by the Environmental Services Association (ESA) has suggested the ind...
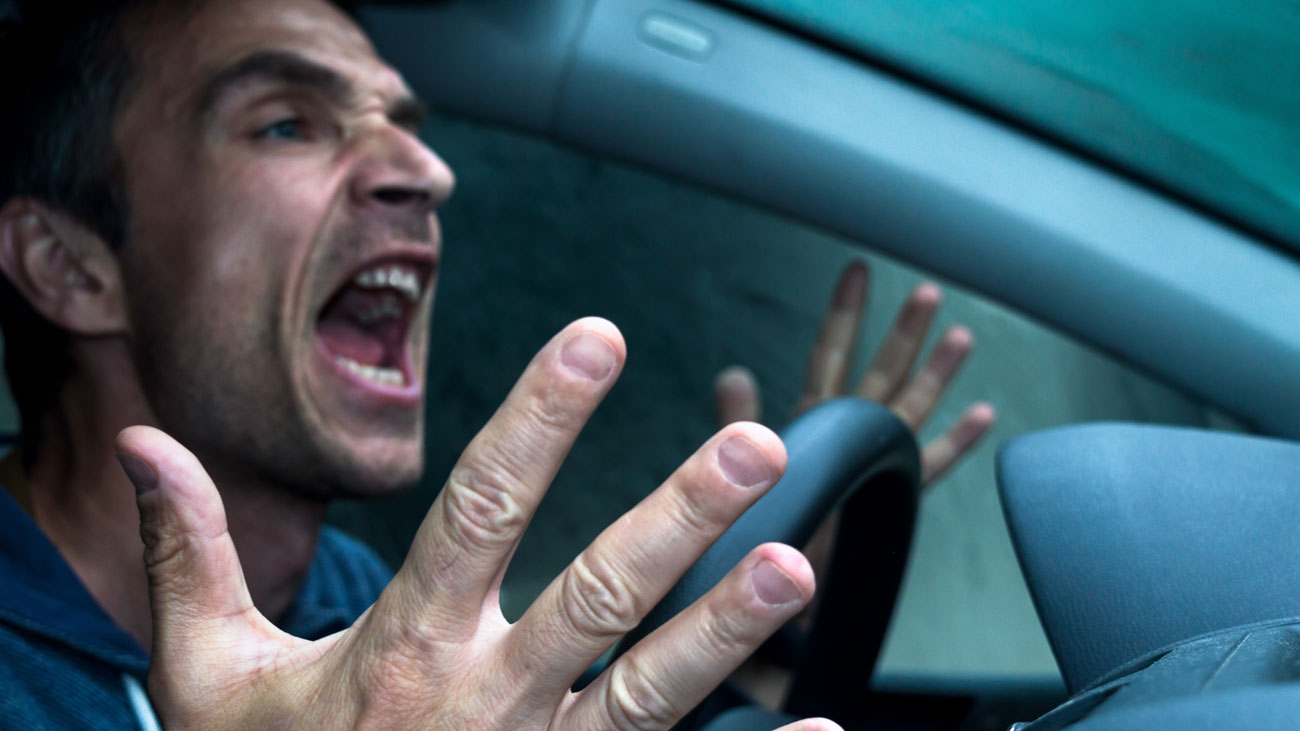
Friday is the most hazardous day of the week for fleet drivers with the highest number of accidents, speeding events, and incidences of aggressive dri...
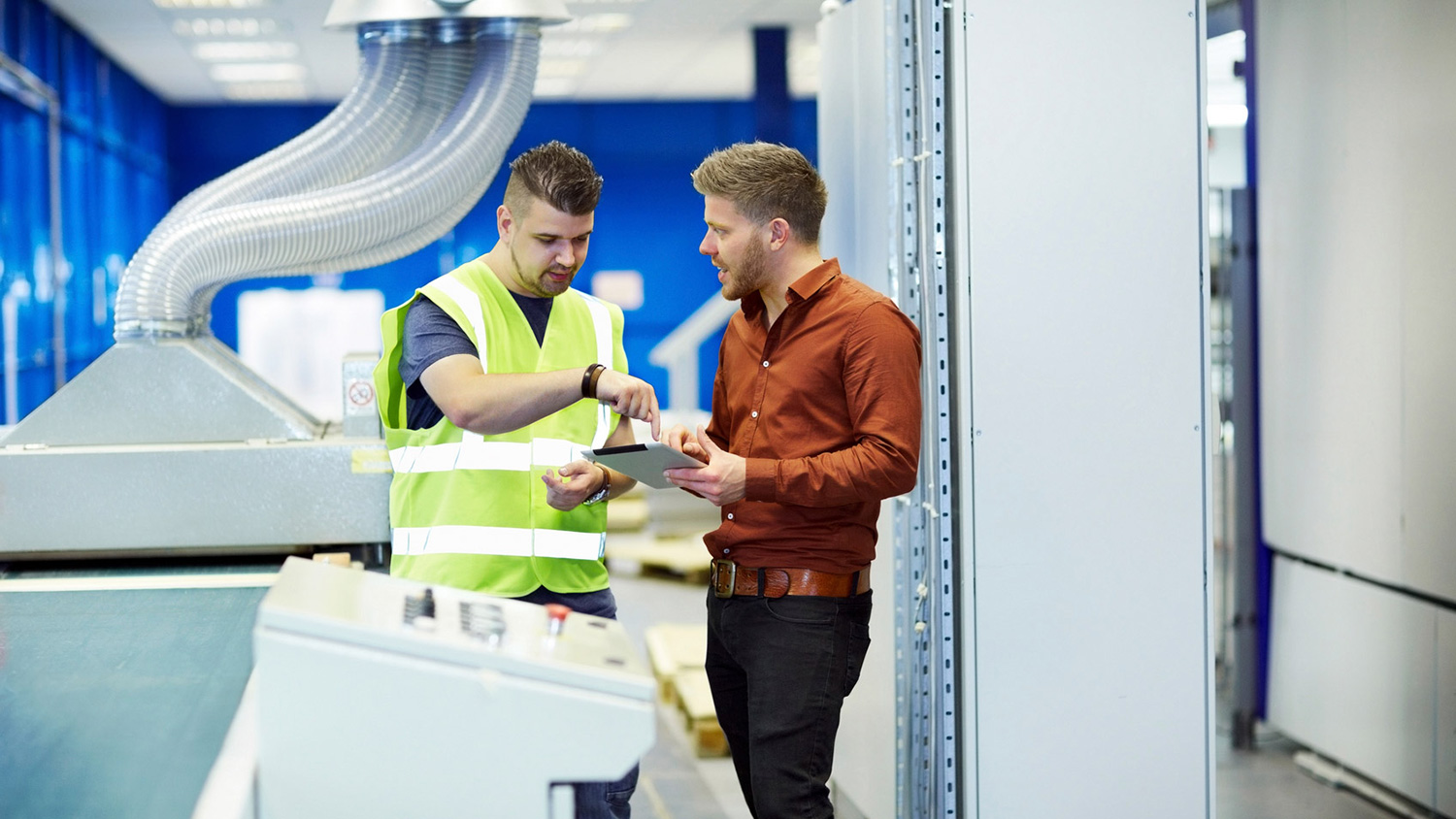
For industries and employers whose activity involves a fast-moving environment where things change rapidly and decisions need to be taken on the spot,...